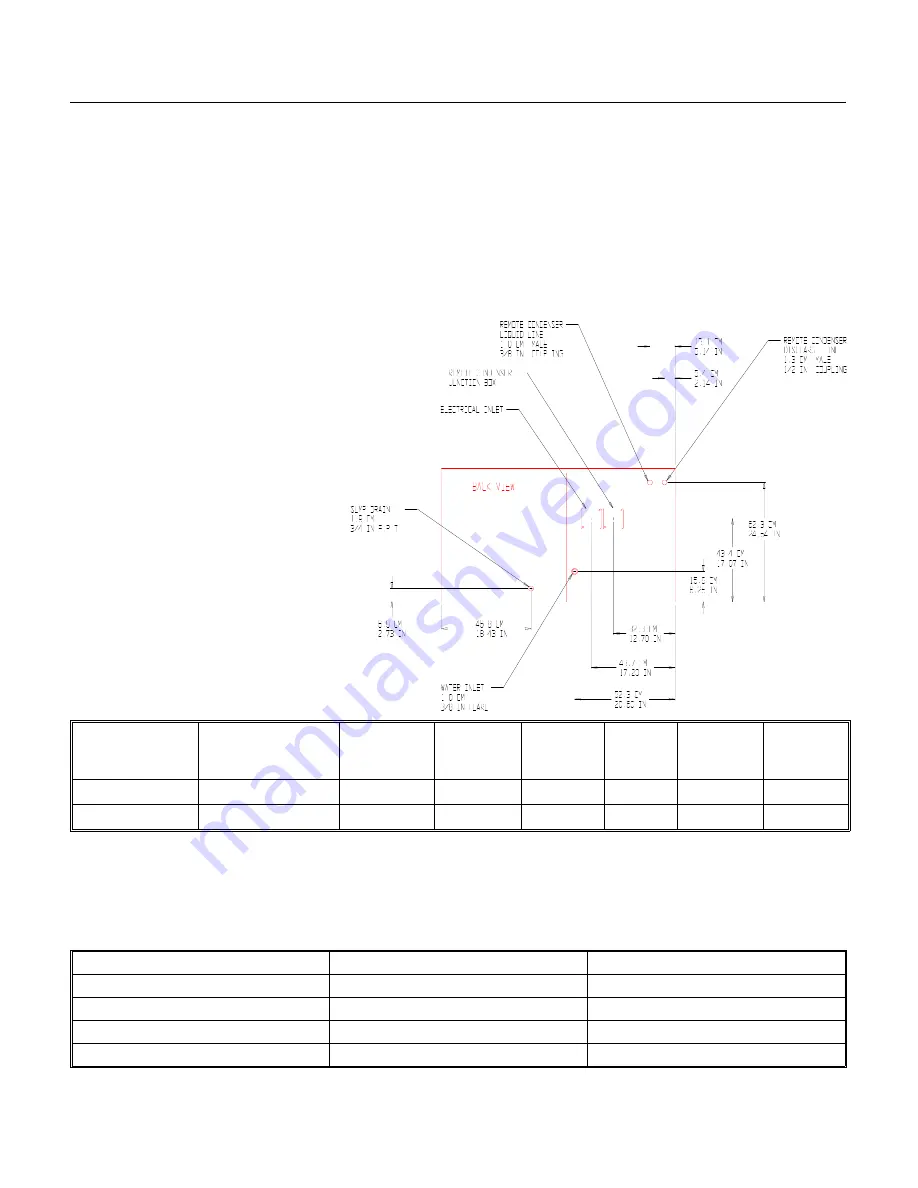
Model Number
Dimensions
(without bin)
W" x D" x H"
Basic
Electrical
Refrigerant
Type
Minimum
Circuit
Ampacity*
Maximum
Fuse
Size
Refrigerant
Charge**
R-22
Condenser
Type
CMS1202RE-3B
48 x 24
3
⁄
8
x 27
1
⁄
2
208-230/60/3 R-22
15.2
20
256 oz.
Remote Air
CMS1202RE-32B 48 x 24
3
⁄
8
x 27
1
⁄
2
208-230/60/1 R-22
21.2
30
256 oz.
Remote Air
* Minimum Circuit Ampacity is used to determine wire size and type per the National Electric Code.
** The unit is shipped with the full charge in the receiver. For re-charging purposes, if the nameplate charge
is different than this number, go by the nameplate.
Use Scotsman remote condenser RC1422. Use precharged tubing kit RT2225 (25’) or RT2240 (40").
This ice system (except remote condenser) is designed to be installed indoors, in a controlled environment.
MINIMUM
MAXIMUM
Air Temperature
50
0
F.
100
0
F.
Water Temperature
40
0
F.
100
0
F.
Water Pressure
20 psi
80 psi
Voltage
-5%
+10%
Scotsman Ice Systems are designed
and manufactured with the highest
regard for safety and performance.
They meet or exceed the standards of
U.L., N.S.F., and C.S.A.
Scotsman assumes no liability or
responsibility of any kind for products
manufactured by Scotsman that have
been altered in any way, including the
use of any parts and/or other
components not specifically approved
by Scotsman.
Scotsman reserves the right to make
design changes and/or improvements
at any time. Specifications and
designs are subject to change without
notice.
FOR THE INSTALLER
The CMS1202R will fit the following Scotsman ice
storage bins:
••
BH900
••
BH1000 (with bin top KBT21)
••
BH1360
and it will stack (with kits) onto the following ice
machines:
••
CMS1402 (with stacking kit KSCMS48)
••
CMS1202 (with stacking kit KSCMS48)
A remote condenser and precharged tubing kit are
required to assemble this ice system.
The normal finish for the machine is enamel
sandalwood. An optional stainless steel panel kit
(SPKCM1402) can be field installed. It contains a
stainless steel top, left side panel, an overlay right
side panel, and front panel.
This manual covers both A and B models (B
models have 2 front panels).
CMS1202R
September 1993
Page 2