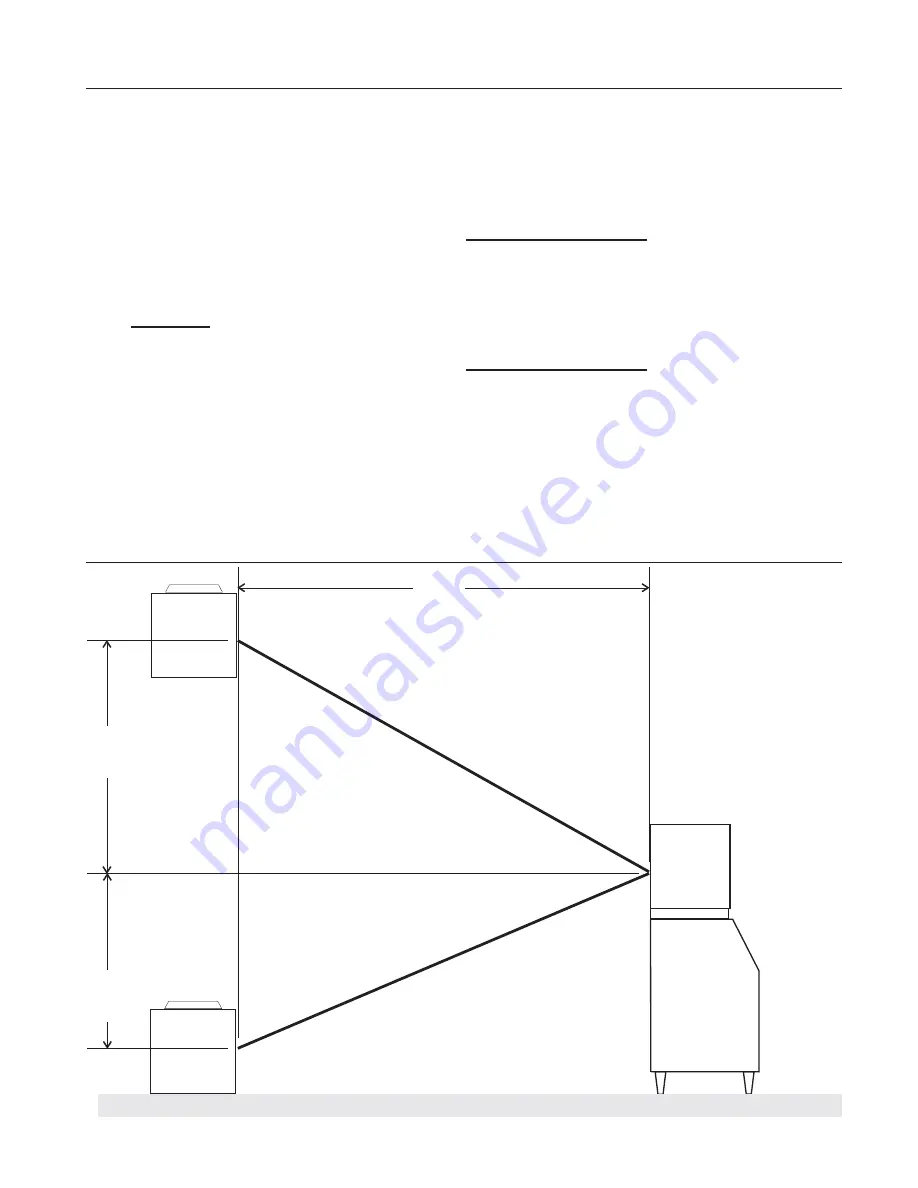
Remote Condenser Location
Use the following for planning the placement of
the condenser relative to the ice machine
Location Limits - condenser location must not
exceed ANY of the following limits:
•
Maximum rise from the ice machine to the
condenser is
35 physical feet
•
Maximum drop from the ice machine to the
condenser is
15 physical feet
•
Physical line set maximum length is
100 feet
.
•
Calculated line set length maximum is
150.
Calculation Formula:
•
Drop = dd x 6.6 (dd = distance in feet)
•
Rise = rd x 1.7 (rd = distance in feet)
•
Horizontal Run = hd x 1 (hd = distance in
feet)
•
Calculation: Drop(s) + Rise(s) + Horizontal
Run = dd+rd+hd = Calculated Line Length
Configurations that do NOT meet these
requirements must receive prior written
authorization from Scotsman.
Do NOT:
•
Route a line set that rises, then falls, then
rises.
•
Route a line set that falls, then rises, then
falls.
Calculation Example 1:
The condenser is to be located 5 feet below the ice
machine and then 20 feet away horizontally.
5 feet x 6.6 = 33. 33 + 20 = 53.
This location would
be acceptable
Calculation Example 2:
The condenser is to be located 35 feet above and
then 100 feet away horizontally.
35 x 1.7 = 59.5. 59.5 +100 = 159.5.
159.5 is
greater than the 150 maximum and is NOT
acceptable.
Operating a machine with an unacceptable
configuration will void the refrigeration system
warranty.
22
.87"
17
.15"
40.35"
hd
rd
dd
Remote
Condenser
Located ABOVE
Ice Machine
Remote
Condenser
Located BELOW
Ice Machine
Condenser Distance &
Location Schematic
Max 35’
Max 15’
CME1356R and CME1656R
May 2001
Page 11