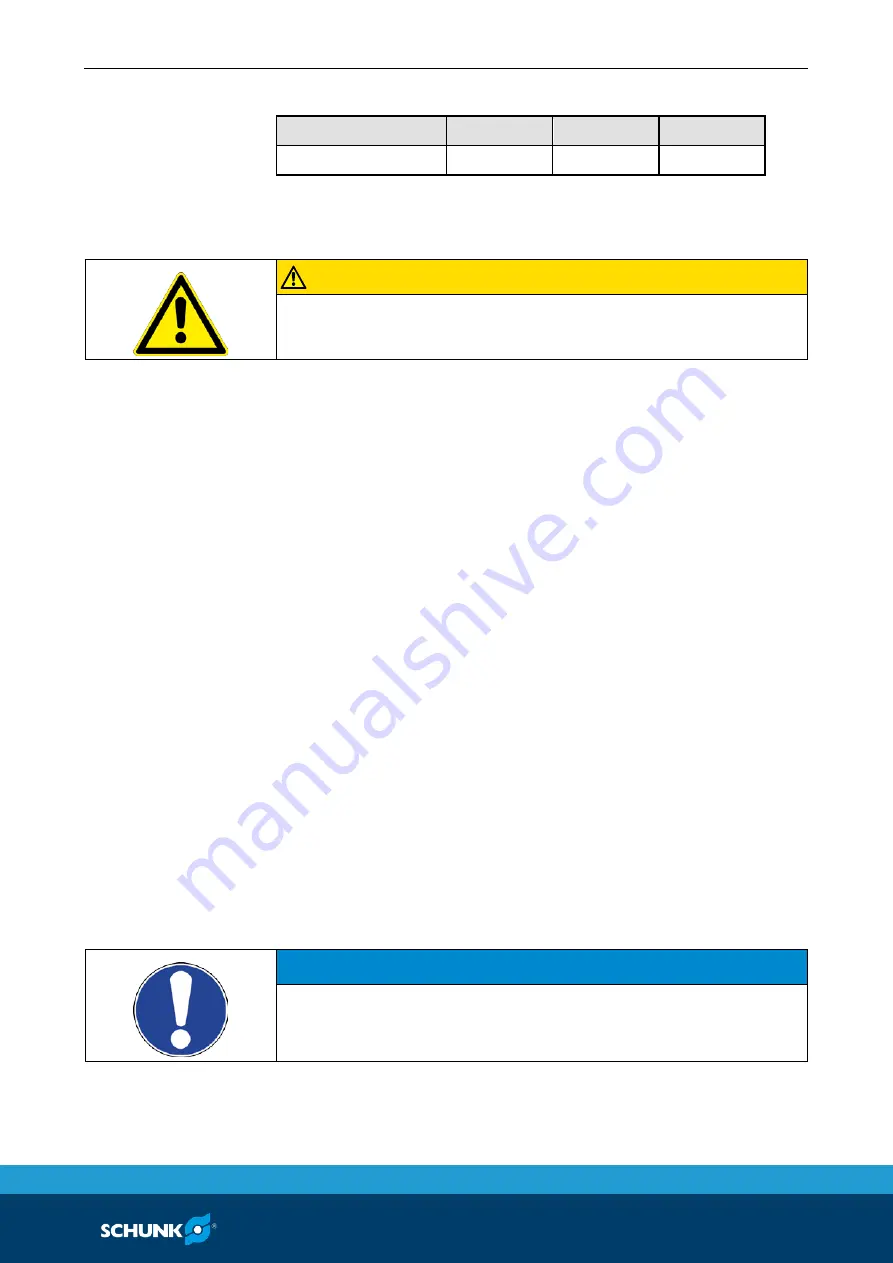
Maintenance
04.00|ROTA FSW |en
33
Chuck ROTA FSW
220-A8
290-A11
400-A15
Number of strokes 2
3
4
(For product information about LINO MAX, see the "Accessories"
chapter of the SCHUNK lathe chuck catalog or contact SCHUNK).
CAUTION
Allergic reactions due to grease in contact with skin!
Wear gloves.
Maintenance instructions
The ROTA FSW chuck quick-change's reliability and safety can only
be guaranteed if the maintenance instructions are complied with.
• For lubrication, we recommend our tried and tested special
grease, LINO MAX 200. Unsuitable lubricants can have a
negative impact on the functioning of the chuck quick-change
(clamping force, coefficient of friction, wear characteristics).
(For product information about LINO MAX 200, see the
"Accessories" chapter in the SCHUNK lathe chuck catalog or
contact SCHUNK).
• The flexible adapter and draw tube adapter must be replaced
every 250,000 clamping cycles or 5,000 clamping device
changes at the latest, whichever occurs first. For this purpose,
the O.D or I.D. clamping on the fitted clamping device and
changes thereof must be documented, monitored reliably and
proof must be available. Corresponding counters on the ma-
chine must be set up during initial assembly or when changing
the flex adapter and the draw tube adapter or the counter
readings noted.
In order to replace the flex adapter and the draw tube adapter,
these parts must be ordered from SCHUNK and can be replaced
upon request by the SCHUNK service team.
NOTICE
Loss of function in the event of heavy soiling!
It is essential that the cleaning intervals are observed.
To avoid precision errors, connection and adjustment surfaces
must be cleaned.
The oiling of flat surfaces and clamping pieces only serves as cor-
8.2