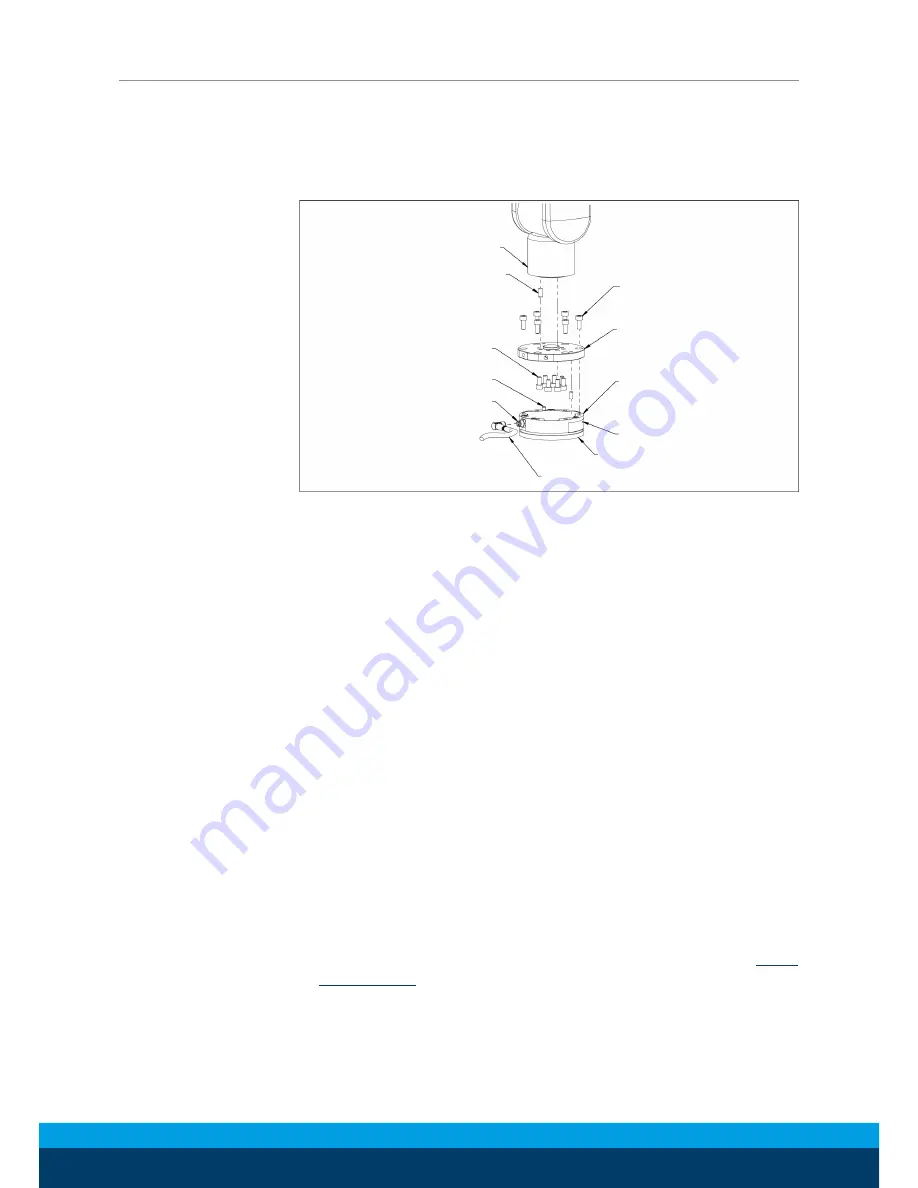
Installation
14
02.00 | FT-AXIA 80 EtherCat | Assembly and operating manual | en | 1009369
4.3 Installing the Sensor to the Robot
Tools required: 4 mm hex wrench, torque wrench
Supplies required: Clean rag, Loctite 242® or fasteners with pre-ap-
plied adhesive
Robot
Dowel Pin
(Customer Supplied)
M5 Socket Head
Cap Screw (6x)
Dowel Pin (2x)
Power and EtherCAT
Connection
Power and EtherCAT cable
(Customer Supplied)
Mounting Side to Customer Tooling
Axia 80
Mounting Side
to Robot or Interface Plate
Interface Plate (example)
Mounting Fasteners
(Customer Supplied)
Ø
To attach the mounting adapter plate to the robot, remove the
six M5 socket head cap screws that secure the adapter plate to
the mounting side of the Axia80 sensor.
Ø
Ensure the mounting surface of the mounting adapter plate and
robot are clean and free of debris.
Ø
If applicable, secure the mounting adapter plate to the robot
arm with customer supplied fasteners and dowel pin.
Ø
M5x 12 socket head cap screws class 12.9 (6x), with pre-applied
adhesive require no additional Loctite for initial installation.
When reusing fasteners, always apply Loctite 242 to the M5
socket head cap screws.
Ø
Using a 4 mm hex wrench, secure the sensor to the mounting
adapter plate with the six M5x 12 socket head cap screws, class
12.9. Tighten to 9 Nm.
Ø
Once the sensor is installed on the robot, the customer tooling
or tool interface plate can be installed.
NOTICE! The tool must not touch any other part of the sensor
except the tool side; otherwise, the sensor will not properly
detect loads.
Ø
Connect a power and EtherCAT cable from the sensor’s connec-
tion to the customer application.
Ø
Properly restrain and route the power and EtherCAT cable
Rout-
ing the Cable
[
}
12].
Ø
After installation is complete, the sensor is ready for normal op-
eration.