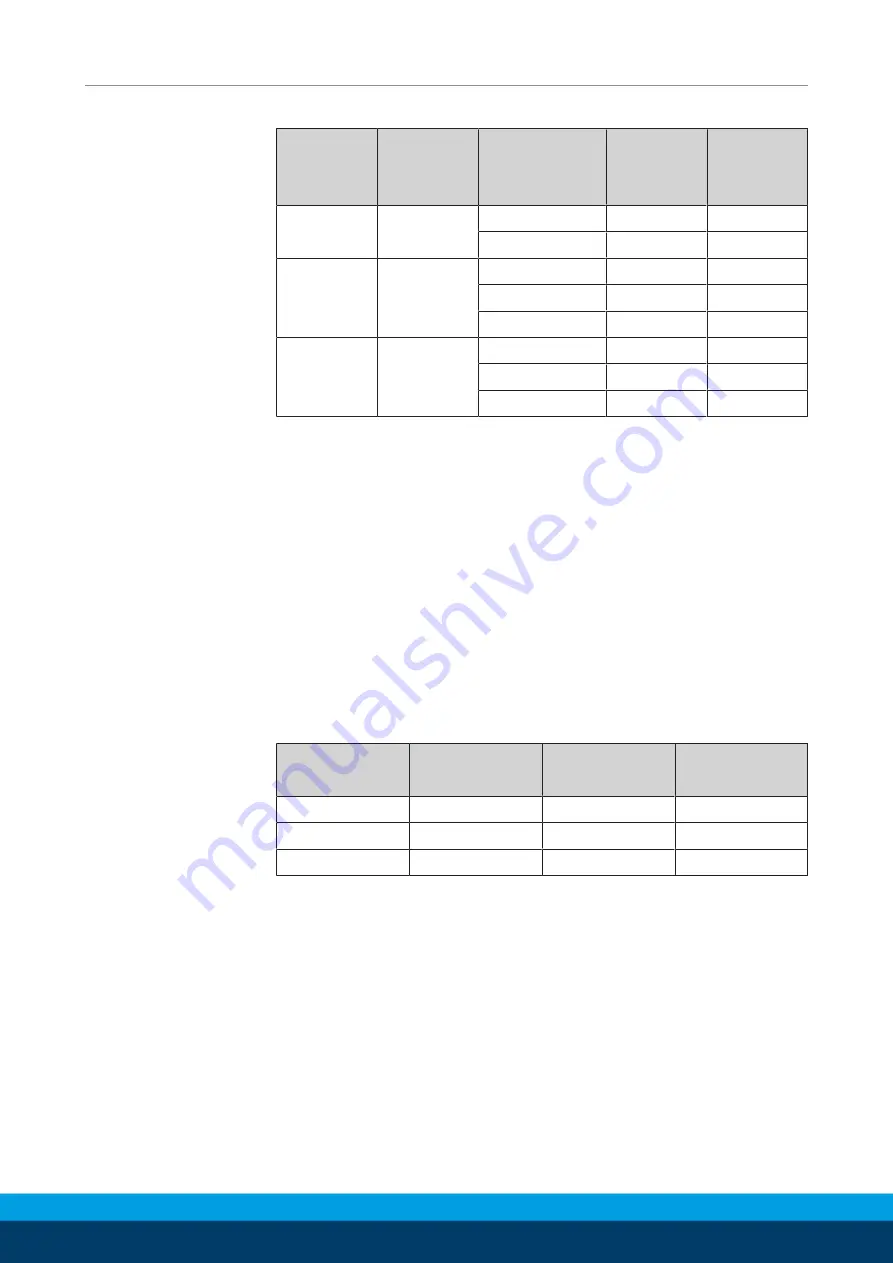
Maintenance
44
11.00 | EGN | Assembly and Operating Manual | en | 389056
Size of the O-rings
Sealing kit
ID no.
2 x O-ring
[mm]
Installation
dimensions
min. [mm]
Installation
dimensions
max. [mm]
EGN 80-SD
1316610
Ø 22 x 1.5
0.95
1.35
Ø 22 x 1.0
0.65
0.9
EGN 100-SD 1304644
Ø 25 x 1.5
0.95
1.35
Ø 26 x 1.2
0.8
1.05
Ø 25 x 1.0
0.65
0.9
EGN 160-SD 1304653
Ø 37.82 x 1.78
1.2
1.6
Ø 37.10 x 1.6
1.05
1.4
Ø 40 x 1.5
0.95
1.35
Testing the function of the gripper
Ø
Test function of the gripper with the "Motion Tool SCHUNK
(MTS)" configuration and commissioning tool, see enclosed
DVD.
✓
Carry out speed movement with parameters according to the
following table.
✓
For installation and operation, see "Motion Tool SCHUNK
(MTS)" software manual.
✓
The gripper must reach the end positions "opened" and
"closed".
Ø
If the gripper does not reach the end positions, contact SCHUNK
Service.
Test parameters
Gripper
End positions
[mm]
Speed [mm/s]
Current [A]
EGN 80-SD
0 … 16
2.0
1.2
EGN 100-SD
0 ... 20
2.0
1.3
EGN 160-SD
0 … 32
2.0
1.8