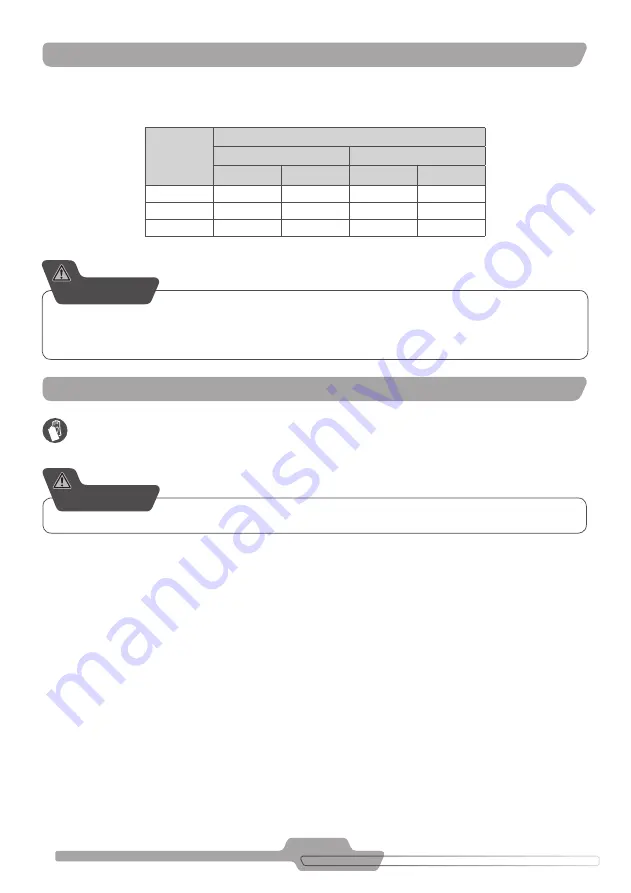
43
11. DRILLING PRECISION
Every drill bit makes a hole slightly larger than its diameter. In the guiding table below you have the rate of this
increase in the size of the hole caused by the drill bit.
TABLE 11.1 - HOLE PRECISION GUIDING TABLE
DRILL BIT
DIAMETER (mm)
INCREASE IN THE SIZE OF THE HOLE
LIGHT METAL
STEEL
SOFT
HARD
SOFT
HARD
5
0,45
0,25
0,16
0,12
10
0,75
0,40
0,18
0,14
15
0,90
0,48
0,20
0,16
It’s also necessary to consider that if the flutes are unequally sharpened, the difference
in size will be much greater than the indicated in the table. The drill bit cannot spin in the chuck, because it
will cause the drill bit to lose its precision and the chuck to lose the jaws’ proper contact surfaces even after
replacing the drill bit.
IMPORTANT
12. PREVENTIVE MAINTENANCE
To guarantee the perfect functioning and increase the lifespan of your equipment,
follow the recommendations below:
ATTENTION
Wear appropriate “leather” gloves when performing maintenance or cleaning up the product in order to
avoid injuries
1. Daily
1.1 Lubricate the spindle (FSB 16) of the spindle with a drop of SAE 30 oil before operating it.
1.2 Clean the machine after each work session, using products which do not harm the equipment and the operator.
2. Weekly
2.1 Verify the voltage and the state of the belt(s) (Figures 8.3 and 8.4).
3. Monthly
3.1 Lubricate the rack (hose), using oil.
4. Quarterly
4.1 Retighten the screw and nuts.
4.2 Check the action of the return spring of the pinion (Figure 12.1), if necessary adjusting it in an anticlockwise
direction.
5. Six monthly
5.1 Wash and lubricate the upper and lower bearings (Figure 12.1). For lubrication use grease with a base of NLGI
2 degree lithium soap with the addition of extreme pressure (EP). Ref.: Shell Alvania EP-2, Texaco Multifak EP-2
6. Every 1000 hours or 12 months (whichever occurs first)
6.1 Replace the return spring and lubricate the pinion.
6.2 Replace the shock absorber (rubber ring) of the return of the Rack set.
Содержание FSB 16 TORK
Страница 2: ......