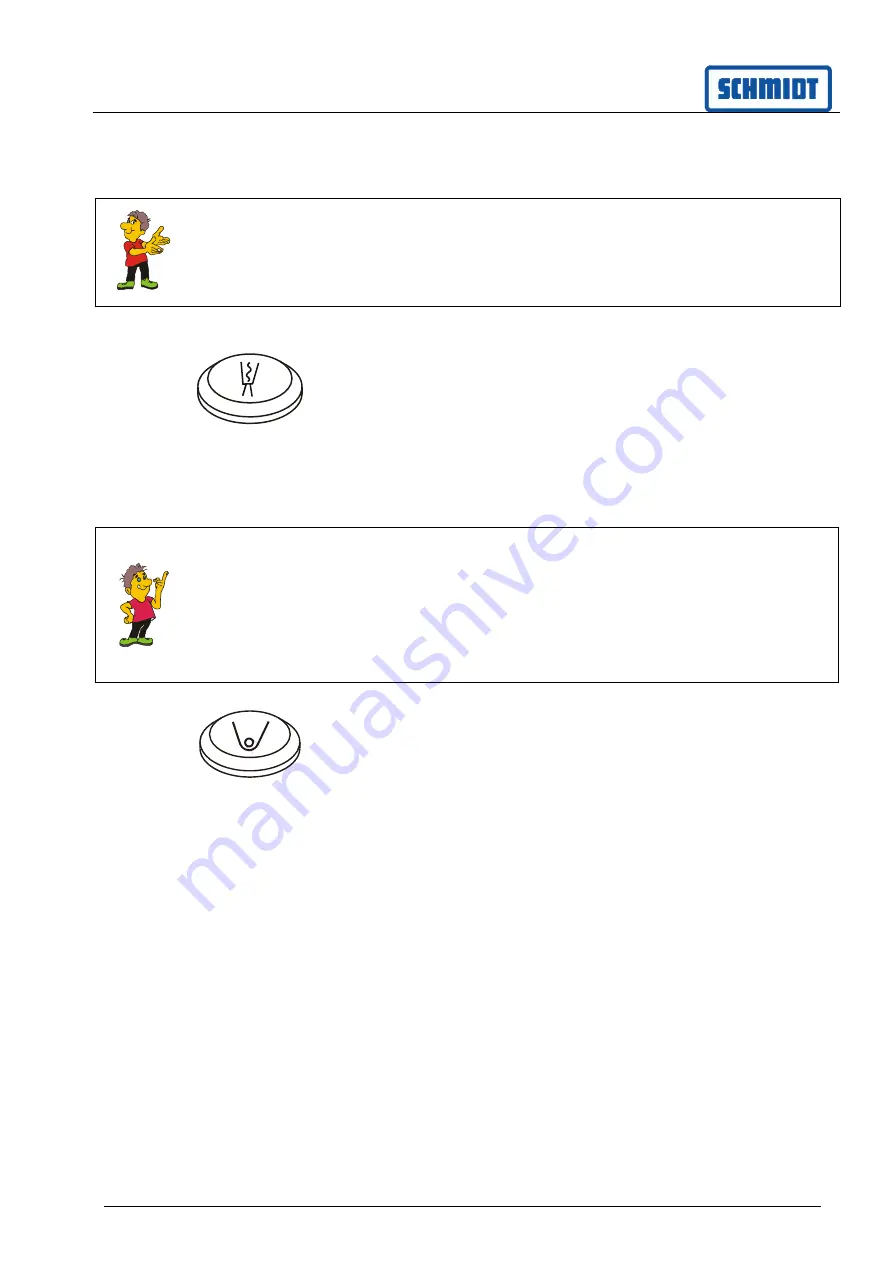
Translation of Original Operating Instructions
Airport Sweeper / Airport Stand Cleaner
2017-02-02 78
8.5.8
Putting the foam path marking into
operation
TIP
The path marker is only engaged if at least
one of the following functions is switched on.
Sweeping with disc brushes
Sweeping with the rear sweeper unit
Cleaning with the blowing equipment
The path marker is preselected or press.
The path marker is pre selected.
Path marking is switched on by
putting the suction, sweeper or blower unit into
operation.
Turning off the path marking
Press the button
8.5.9
Putting the front pick-up into
operation
NOTE
Used only on
take-off and landing strips
on even terrain
in the case of large pieces of waste, e.g., stones,
screws
Use the front pick-up briefly only and then
switch off again.
The suction function of the rear sweeper must
be switched on.
The front pick-up is preselected or press.
The front pick-up is preselected.
The front pick-up lifts or lowers.