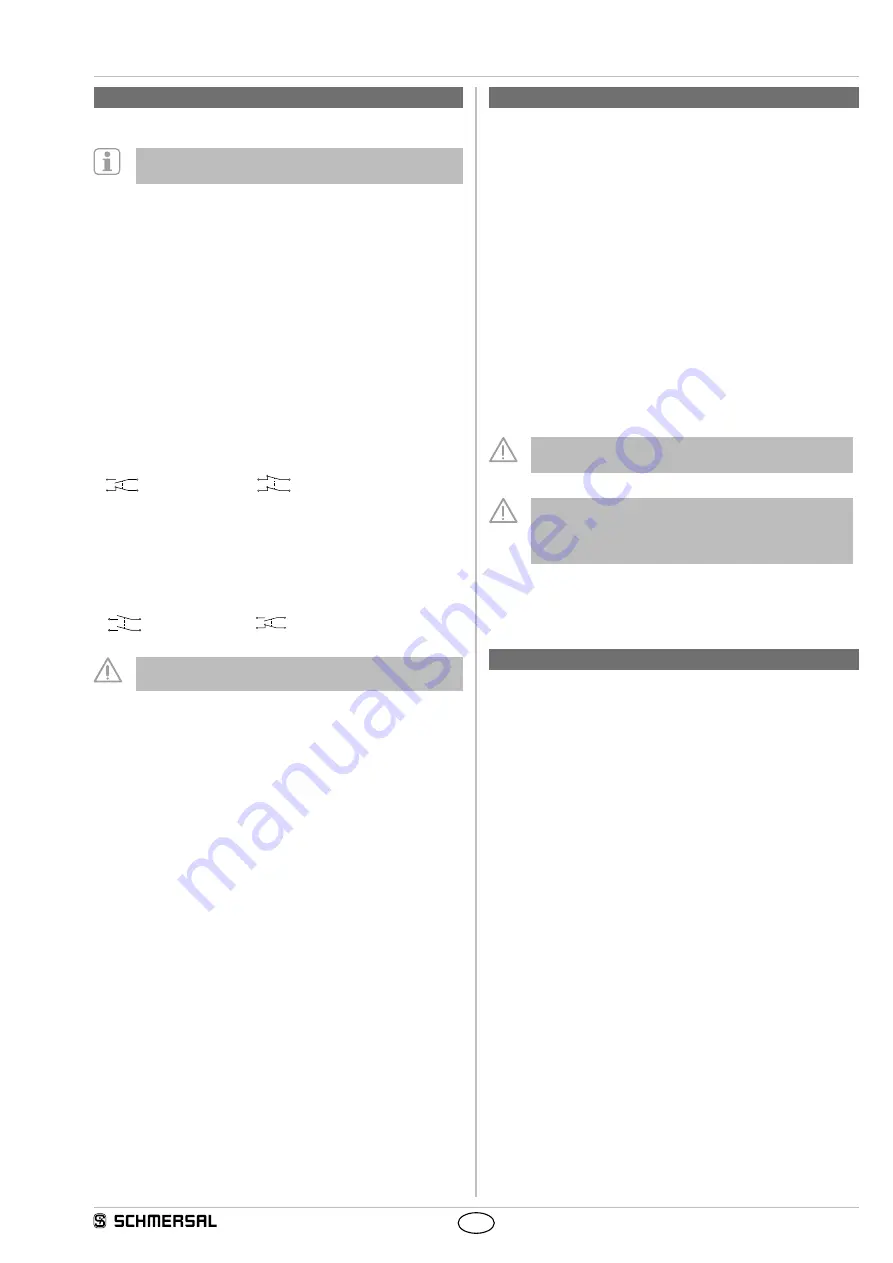
5
EX-T 335
Operating instructions
Position switches
EN
4. Electrical connection
4.1 General information for electrical connection
The electrical connection may only be carried out by
authorised personnel in a de-energised condition.
The contact labelling can be found in the wiring compartment of the switch.
Do not install cable loops in the inside space of the enclosure. Bare wires
must not protrude beyond the clamping disc. Lead the cable insulation
up to the clamping disc. All screws and/or nuts of the terminals, also the
unused, must be screwed tight.
Cable glands (included in delivery) are only authorised for permanent
cables. The constructor must provide for the necessary strain relief.
After wiring, dust and soiling must be removed from the wiring
compartment.
4.2 Contact variants
Contacts are shown with safety guard closed.
1 NO / 1 NC
2 NC
EX-T335-11Y
EX-T335-02Y
13
21
14
22
A
11
21
12
22
A
A
2 NO
1 NO contact / 1
NC contact with
overlapping
EX-T335-20Y
EX-T335-11YUE
13
23
14
24
13
21
14
22
Position switches with two NO contacts (-20) are not suitable
for safety functions.
5. Set-up and maintenance
5.1 Functional testing
The safety function of the safety components must be tested. The
following conditions must be previously checked and met:
• The installation is executed according to the instructions.
• The connection is executed correctly.
• The cable is correctly executed and connected.
• Check the free movement of the actuating element.
• The safety component is not damaged.
• Remove particles of dust and soiling.
• Check cable entry and connections in de-energised condition.
5.2 Maintenance
In case of correct installation in accordance with the instructions
described above, the component requires little maintenance. For use in
extreme conditions, we recommend routine maintenance including the
following steps:
1. Check the correct fixing of the actuator and the safety switchgear.
2. Lubricate the shaft or plunger
3. Remove particles of dust and soiling
4. Check cable entry and connections in a de-energised condition
Do not open the device when live.
Throughout the operative life cycles of the safety switchgear,
suitable constructive and organisational measures are to be
taken to prevent against tampering and to prevent the safety
device being overridden.
Damaged or defective components must be replaced.
For explosion protection reasons, the component must be
exchanged after max. 1 million operations.
6. Disassembly and disposal
6.1 Disassembly
The safety switchgear must be disassembled in a de-energised
condition only.
6.2 Disposal
The safety switchgear must be disposed of in an appropriate manner in
accordance with the national prescriptions and legislations.