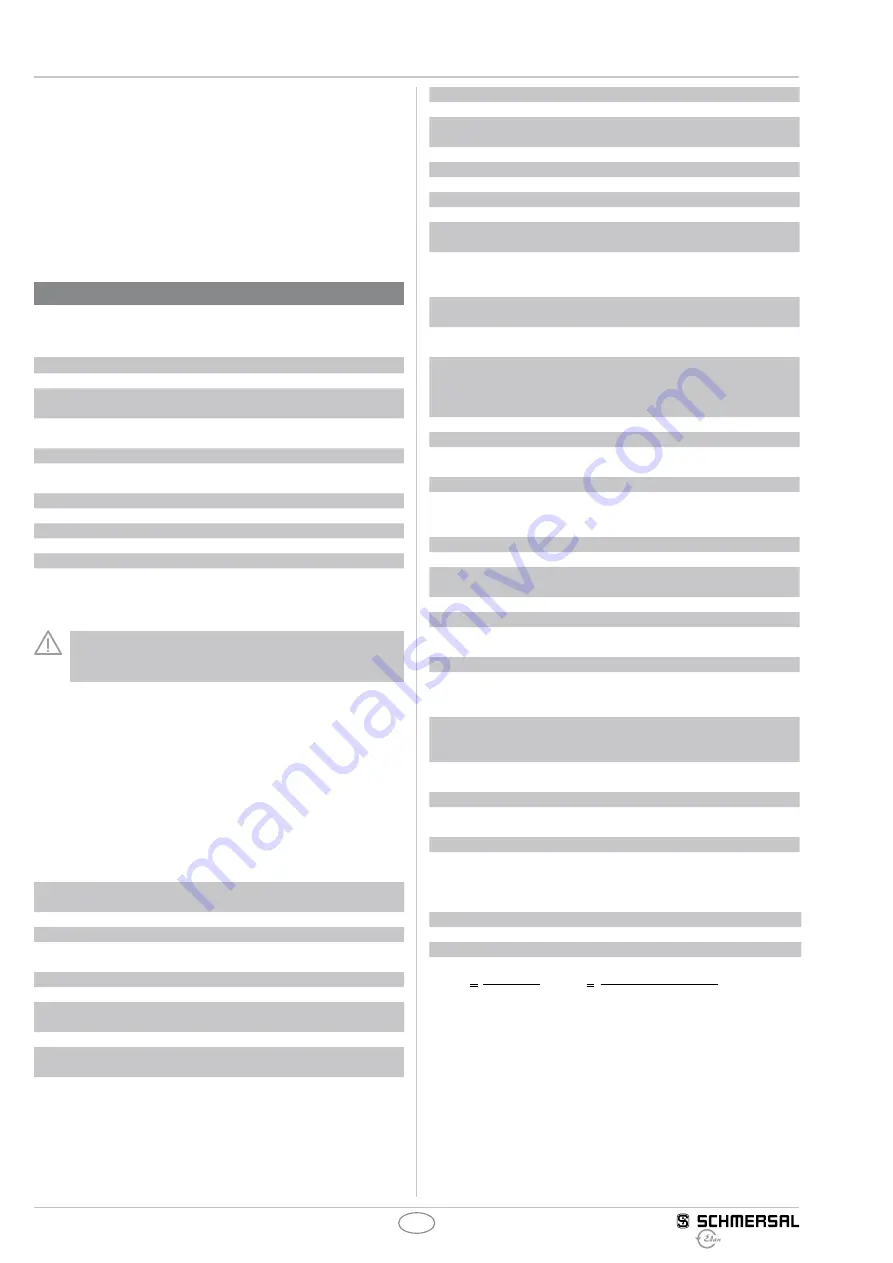
2
Operating instructions
Emergency stop command device
EDR EFR
EN
1.7 Exclusion of liability
We shall accept no liability for damages and malfunctions resulting from
defective mounting or failure to comply with this operating instructions
manual. The manufacturer shall accept no liability for damages resulting
from the use of unauthorised spare parts or accessories.
For safety reasons, invasive work on the device as well as arbitrary re-
pairs, conversions and modifications to the device are strictly forbidden;
the manufacturer shall accept no liability for damages resulting from
such invasive work, arbitrary repairs, conversions and/or modifications
to the device.
2 Product description
2.1 Ordering code
This operating instructions manual applies to the following types:
EDR
➀ ➁ ➂ ➃
No. Option
Description
➀
R
Latching only in combination with EFR,
turn and pull to unlock
RZ
Latching only in combination with EFR,
turn to unlock
Z
Turn to unlock, without EFR
RS
With cylinder lock, unlocking only by key,
only by pulling, with EFR
➁
50
Head diameter 49 mm
40
Head diameter 38.5 mm
➂
Mounting hole 22.3 mm
VH
Mounting hole 30.5 mm
➃
RT
Red colour
Not all component variants, which are possible according to this order
code, are available.
Only if the information described in this operating instructions
manual is realised correctly, the safety function and therefore
the compliance with the Machinery Directive is maintained.
2.2 Special versions
For special versions, which are not listed in the order code below 2.1,
these specifications apply accordingly, provided that they correspond to
the standard version.
2.3 Destination and use
The EDR series emergency stop command devices are designed for
use in emergency stop circuits to EN 13850.
2.4 Technical data
Standards:
IEC 60947-5-1, IEC 60947-5-5,
IEC 60947-1, EN ISO 13850
Design:
round
Mounting
∅:
22.3 mm
Spacing:
for head Ø 40 mm: 50 × 40 mm,
for head Ø 50 mm: 50 × 50 mm
Front plate thickness:
1 … 6 mm
Mounting position:
any
Climate resistance
to DIN EN 60068:
Part 2-30
Ambient temperature:
–25°C … +75°C
Protection class
to IEC 605290:
IP 65
Fully insulated:
yes
Material mushroom button:
Al anodised
Fixing:
with mounting flange
Max. tightening torque for
the ELM fixing screws:
0.6 Nm
Actuating force:
approx. 25 N
Mechanical life:
1 x 10
5
operations
Rohs compliant:
yes
Contact elements
Standards:
IEC/EN 60947-5-1
Rated operating
voltage U
e
max.:
400 V
Rated insulation voltage U
i
for degree of pollution 3
to EN 60 947-1:
400 V
Rated impulse withstand
voltage U
imp
:
4 kV
Thermal nominal
current I
the
(in air):
10 A
Rated operating current I
e
depending on the utilisation
category and rated operating
voltage U
e
:
8 A, AC-15, 250 VAC
5 A, DC-13, 24 VDC
Contact reliability:
5 VDC / 1 mA
Max. fuse rating:
gG 10 A
Evidence of the
positive break:
2.5 kV impulse voltage
Positive break travel:
approx. 2 mm after the opening point
Air clearances and
creepage distances
to DIN EN 60664 1:
4 kV/3
Switching points:
depending on the contact execution
Temperature range:
–25°C … +60°C
Climate resistance
to DIN EN 60068:
Part 2-30
Mounting position:
any
Mechanical life:
10 x 10
6
operations
Actuating force
at stroke end:
approx. 9 N
Terminal labelling:
to IEC 60947-1
Termination:
Screw connection
Flat plug-in connector
Clamp connection
Cable section:
solid wire: 2 × (2 … 2 mm
2
)
stranded wire (with conductor ferrules):
2 x (0.5 … 1.5 mm
2
)
Tightening torque for
the connecting screw:
max. 1 Nm
Shock-protection:
available (to EN 50 274 and BGV A2)
Protection class:
Connections: IP 20 (finger-safe)
Switching elements: IP 40
Approvals:
cULus (save cage clamp connection)
2.5
Safety classification
Standards:
EN ISO 13849-1
B
10d
(NC contact):
100,000
Service life:
20 years
MTTF
B
d x
x
h
s/h
3600
d
10d
op
op
op
n
0,1 x n
op
t
cycle