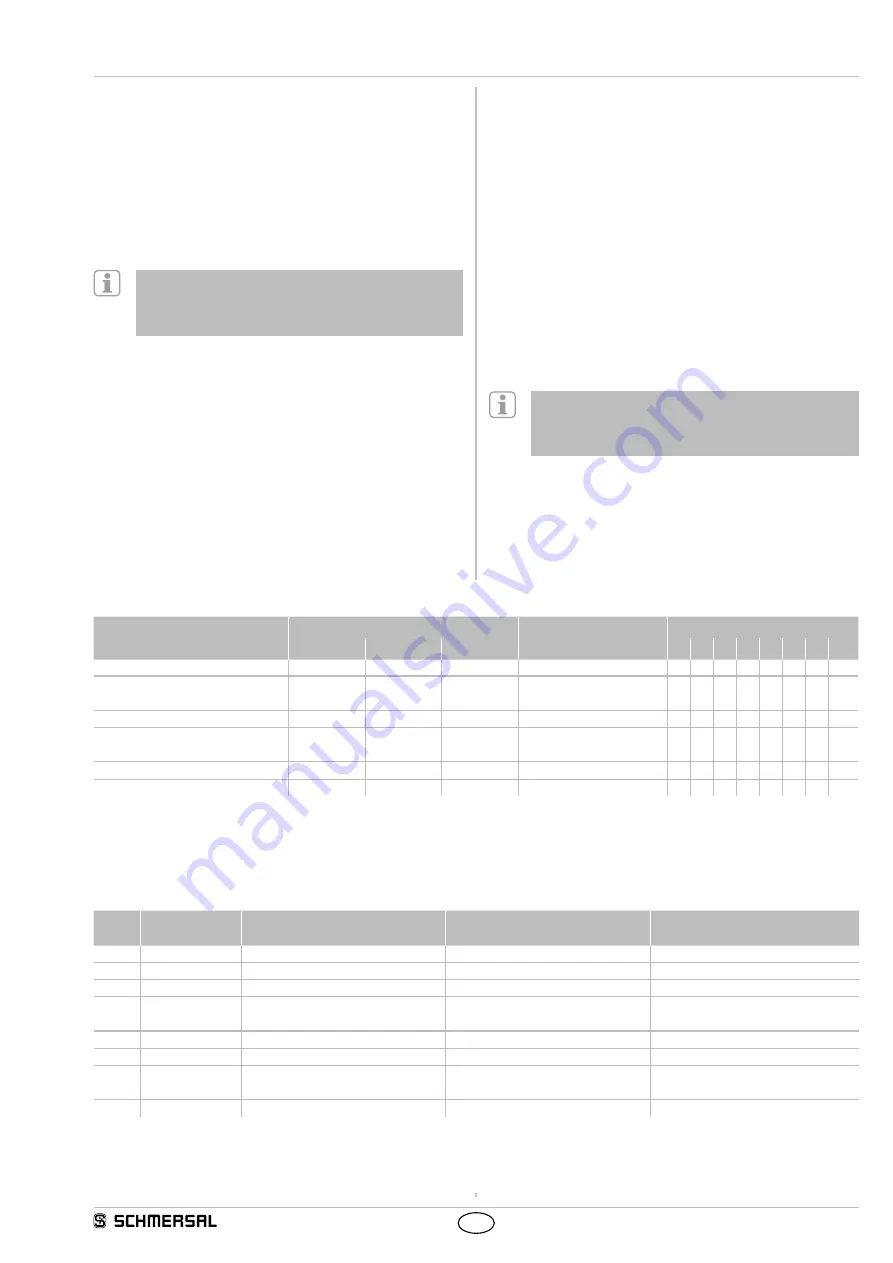
7
CSS 34F0
CSS 34F1
Operating instructions
Safety sensor
EN
5.3 Safety-sensors with serial diagnostic function
Safety sensors with serial diagnostic cable have a serial input and
output cable instead of the conventional diagnostic output. If CSS
sensors are daisy-chained, the diagnostic data are transmitted through
the series-wiring of the inputs and outputs.
Max. 30 CSS 34 sensors can be wired in series with one CSS 34F0/F1.
For the evaluation of the serial diagnostics line either the PROFIBUS-
Gateway SD-I-DP-V0-2 or the Universal-Gateway SD-I-U-... are
used. The PROFIBUS-Gate way is integrated as slave in an available
PROFIBUS DP system.
Detailed information regarding the use of serial diagnostics
can be found in the operating instructions manuals of the
FIELDBUS Gateway as well as in the Online Catalogue on
the Internet, check out: www.schmersal.net.
In this way the diagnostic signals can be evaluated with a PLC. The
following operational information is automatically and permanently
written in an input byte of the PLC for each CSS 34 sensor of the
series-wired chain:
Bit 0: safety outputs enabled
Bit 1: safety sensor actuated, actuator identified
Bit 3: feedback circuit open or button not actuated
Bit 4: both safety inputs live
Bit 5: safety sensor actuated in hysteresis area
Bit 6: error warning, switch-off delay activated
Bit 7: error, safety outputs switched off
In the event of a communication error between the field bus Gateway
and the safety sensor, the switching condition of the safety output of the
safety sensor is maintained.
Fault
A fault has occurred, which causes the safety outputs to be disabled.
The fault is reset, when the cause is eliminated and bit 7 of the request
byte changes from 1 to 0 or the safety guard is opened. Faults at
the safety outputs are only deleted upon the next release, as the
fault rectification cannot be detected sooner. For devices with serial
diagnostic, a bit can be set/deleted in the call telegram to reset the fault.
For devices with serial diagnostic, a bit can be set/deleted in the call
telegram to reset the fault.
Error warning
A fault has occurred, which causes the safety outputs to be disabled
after 30 minutes. The safety outputs initially remain enabled. This
enables the shutdown of the process in a controlled manner. An error
warning is deleted when the cause of error is eliminated.
Diagnostic error (warning)
If an error (warning) is signalled in the response byte, detailed fault
information can be read out.
Accessories SD interface
For ease of wiring and series-wiring of SD devices,
considerable accessories are available. Detailed information
is available on the Internet, www.schmersal.net.
Table 2: Function of the visual diagnostic LEDs, the serial status signals and the safety outputs by means of an example
System condition
LED
Safety outputs
serial diagnostic byte bit no.
green
red
yellow
Y1, Y2
7 6 5 4 3 2 1
0
Supply voltage on, not actuated
On
Off
Off
0 V
0
0
0
0
0
0
0
0
Actuated, feedback circuit open /
not actuated
On
Off
Flashes
(5Hz)
0 V
0
0
0
1
1
0
1
0
Actuated, safety outputs enabled
On
Off
On
24 V
0
0
0
1
0
0
1
1
Actuated in limit area
On
Off
Flashes
(1Hz)
24 V
0
0
1
1
0
0
1
1
Actuated, warning
On
On/flashes
On
24 V
0
1
0
1
0
0
1
1
Actuated, fault
On
On/flashes
On
0 V
1
1
0
1
0
1
1
0
The shown bit order of the diagnostic byte is an example. A different combination of the operational conditions will lead to a change of the bit order.
Table 3: I/O data and diagnostic data
Communication directions: Request byte:
from the PLC to the local safety sensor
Response byte:
from the local safety sensor to the PLC
Warning/error byte:
from the local safety sensor to the PLC
Bit n° Request byte
Response byte
Diagnostic
error warning
Diagnostic
error
Bit 0:
Error reset
Safety output activated
Error output Y1
Error output Y1
Bit 1:
---
Actuator detected
Error output Y2
Error output Y2
Bit 2:
---
---
Cross-wire short
Cross-wire short
Bit 3:
---
Start function missing / feedback circuit
open
Temperature too high
Temperature too high
Bit 4:
---
Input condition X1 and X2
---
Actuator fault, coding error
Bit 5:
---
Actuated in limit area
Internal device error
Internal device error
Bit 6:
---
Error warning
Communication error between the field
bus Gateway and the safety switch
---
Bit 7:
Error reset
Error (enabling path switched off)
Operating voltage too low
---
The described condition is reached, when Bit = 1