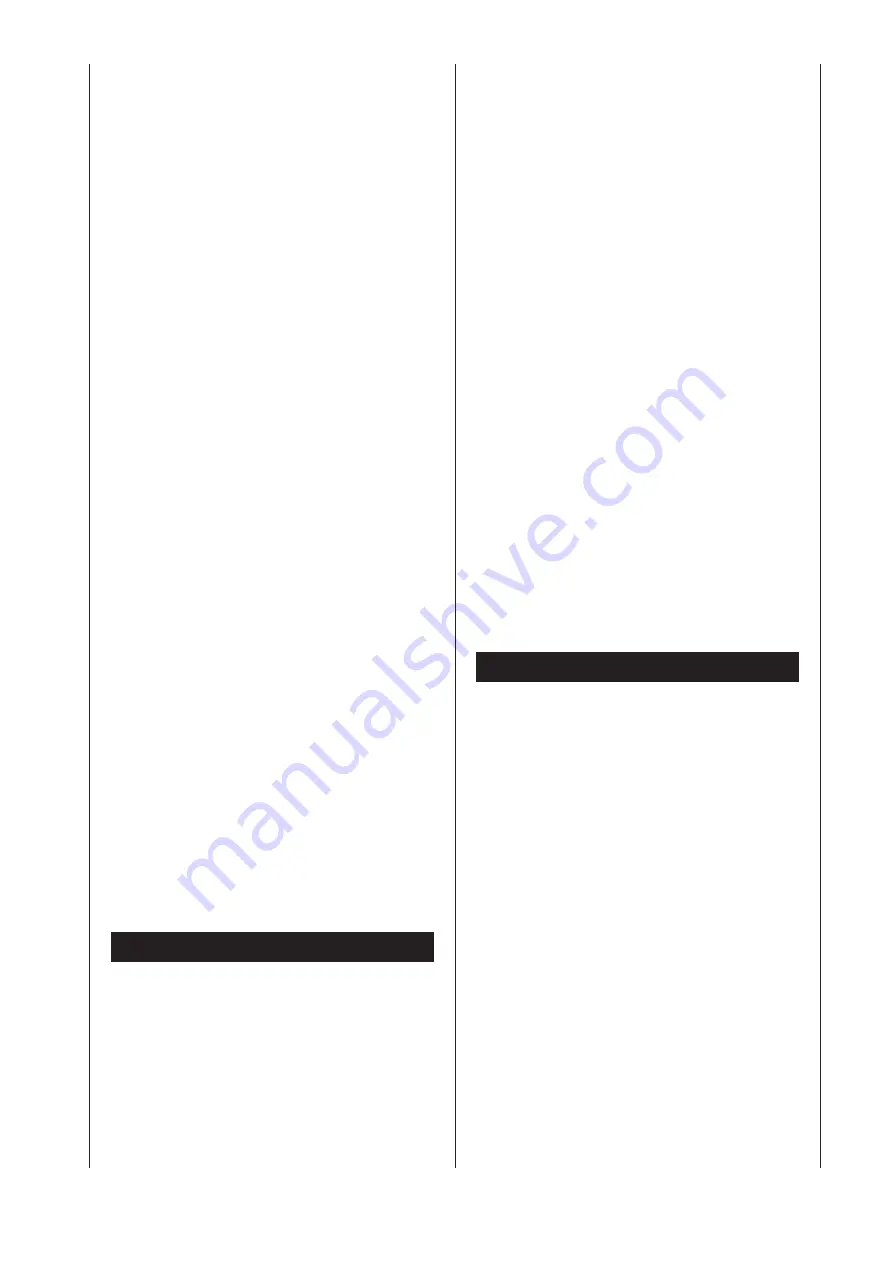
14 english
• Loosen the saw blade by unscrewing tightening screw
B.
• Fit the new saw blade.
• Turn the band wheel by hand in the cutting direction,
while at the same time using handle B to tighten the
blade. The tightness depends on the width of the saw
blade. Wider saw blades have to be tighter than narrow
ones.
Attention: Overtightening the blade will lead to premature
breaking of the blade!
After you have finished working with the band saw, the saw
blade should always be loosened! Do so by moving lever
A to „–“.
Side-to-side corrections, Fig. 8
• The saw blade should run more or less in the middle of
the wheel belts.
• Turn the upper wheel belt manually in the cutting direc
-
tion, and make side-to-side corrections by the grip (1).
• After successful adjustment, tighten the wing-bolts (2)
The upper saw blade leader can be adjusted by up to
250
mm of the height of the work piece
(3).Keeping the distance
to the work piece as small as possible allows the optimal
leading of the blades and a secure working situation!
Adjustment of rotational speed, Fig. 9
Warning:
Unplug the machine!
• Open the saw blade, protection unit and secure it with
a block.
• Release grip A on the motor side; release the belts.
Change the belts if necessary.
• Now, adjust the desired rotational speed:
Step 1 = 1200 m/min.
Step 2 = 800 m/min.
• Tighten the belts and grip A once again. Then close the
saw blade, protection unit.
Counter pressure bearing, Fig. 10
The counter pressure bearing (1) assumes the feed pres
-
sure from the work piece.
Adjust the upper and lower counter pressure bearings so
they lightly touch the saw blade backs.
Guide rollers, Fig. 10
Adjust the upper and lower guide rollers (2) to the breadth
of each of the saw bands. The front corner of the guide roll-
ers should only reach to the highest tooth base of the saw
blade. If the guide rollers lightly touch the saw blade, re-
tract them with the knurled screw on the base of the rolls.
The saw bands must not jam!
m
Working information
The following recommendations are examples of the safe
use of band saws.
The following safe working methods should be seen as an
aid to safety. They cannot be applied suitably completely
or comprehensively to every use. They cannot treat every
possible dangerous condition and must be interpreted
carefully.
• Connect the machine to a suction unit when working
in closed rooms. A suction device which conforms with
commercial regulations must be used for suction in
commercial areas.
• Loosen the sawband when the machine is not in opera
-
tion (e.g. after finishing work). Attach a notice on the
tension of the saw band to the machine for the next
user.
• Collect unused sawbands and store them safely in a dry
place. Check for faults (teeth, cracks) before use. Do not
use faulty sawbands!
• Wear suitable gloves when handling sawbands.
• All protective and safety devices must be securely
mounted on the machine before beginning work.
• Never clean the sawband or the sawband guide with a
hand-held brush or scraper while the sawband is run-
ning. Resin-covered sawbands impair working safety and
must be cleaned regularly.
• For your own protection, wear protective glasses and
hearing protection. Wear a hairnet if you have long hair.
Roll up loose sleeves over the elbows.
• Always position the sawband guide as near the work
-
piece as possible when working.
• Insure sufficient lighting in the work area and around the
machine.
• Always use the fence for straight cuts to keep the work
-
piece from tipping or slipping away.
• When working on narrow workpieces with manual feed,
use the push stick.
• For diagonal cuts, place the saw bench in the appropri
-
ate position and guide the workpiece on the fence.
• Insure safe workpiece guidance.
• For arced and irregular cuts, push the workpiece evenly
using both hands with the fingers together. Hold the
workpiece with your hands on a safe area.
• Use a pattern for repeated arced or irregular cuts.
• Insure that the workpiece does not roll when cutting
round pieces.
• Use the traverse cutting gauge special accessory for
safety when making traverse cuts.
m
Electrical Connection
The installed electric motor is connected and is ready to
work.
The connection complies with the relevant VDE and DIN
regulations.
The customer-side mains supply and the used extension
line must meet these regulations.
Installations, repair, and maintenance work relating to the
electric installation may only be performed by specialists.
Important Notes
The electric motor has been designed for the S 1 operating
mode.
In case of an overload of the motor, it turns off automati-
cally. After a cooling period (duration varies), you can turn
on the motor again.
Defective Electric Connection Lines
Often, insulation damages occur on electrical connection
lines.
Causes are:
• Drag marks if connection lines are led through window or
door clearances.
• Kinks due to improper attachment or routing of the con
-
nection line.
• Cuts caused by running over the connection line.
• Insulation damages caused by pulling the connection
line out of the wall socket.
• Fissures caused by the ageing of the insulation.
Such defective electric connection lines must not be used
and are
hazardous
due to the insulation damages.
Содержание 7323 0901
Страница 102: ...international 103 ...
Страница 103: ...104 international Basato 4 ET Zeichnung ...
Страница 104: ...international 105 ...
Страница 105: ...106 international ...
Страница 106: ...international 107 ...
Страница 108: ...Fig 1 Fig 2 Fig 3 A Fig 4 Fig 5 1 Fig 5 2 Fig 5 3 A Fig 6 ...