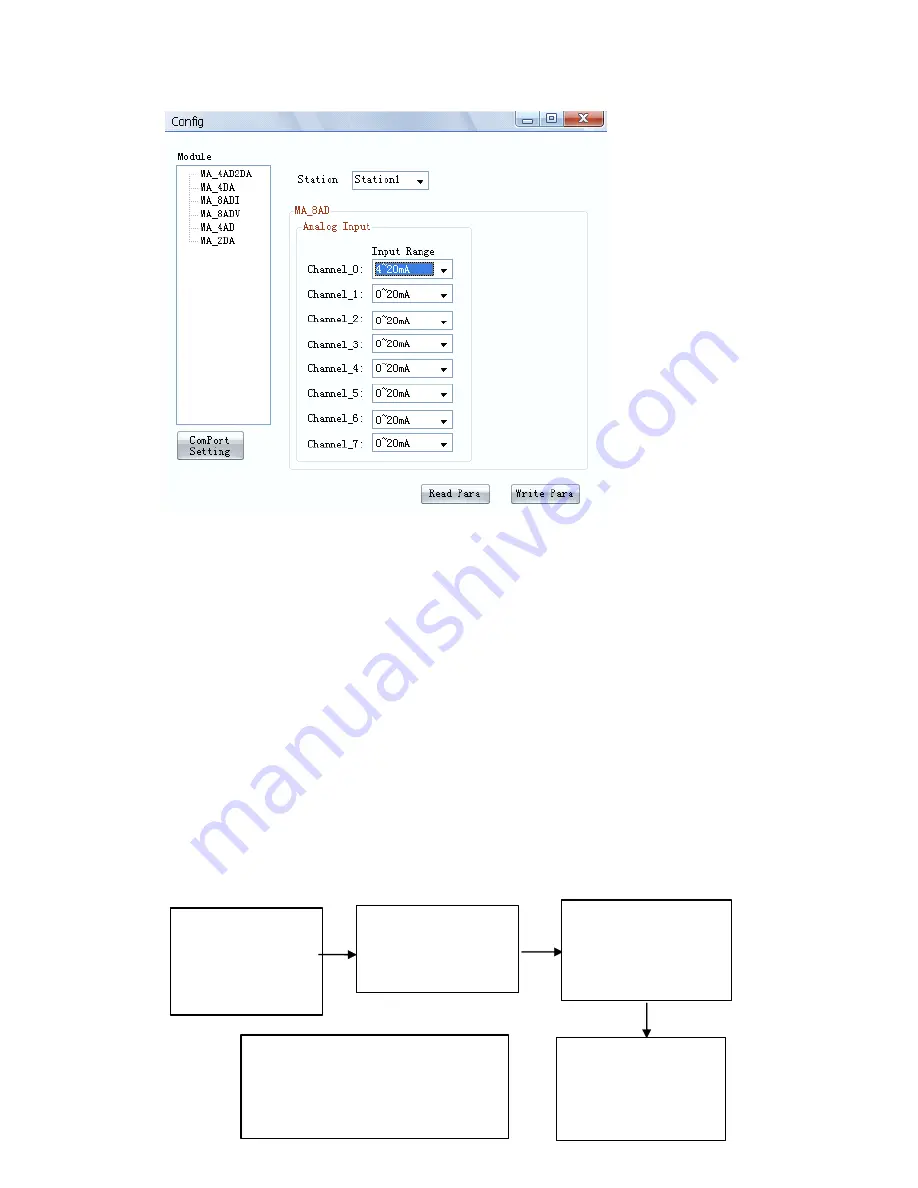
Set the current range of channel 0 to be 4~20mA, click "Write Para" to make them effective.
At the beginning of the program, write the PID parameters, set value, control period into the
register. It needs to configure the related parameters of the control object including PID enable bit,
self-study enable bit in order to do Modbus communication. When the local trigger condition is
satisfied, PLC send the set value, channel control period, PID parameters to the corresponding
address of the module via write instruction. At this time, all the preparations for PID self-study
have been done. When PID enable bit is on, the module starts to do PID control with the defaulted
state of negative action and reads the current value with the period of 100ms. When self-study
enable bit is on, the module starts to do self-study. Among up two processes, read the PID output
value to the local register to realize object control.
The whole process are as below:
Data evaluation:
PID parameters, set
value, control period...
Local related coil is set
on: PID enable bit,
self-study enable bit
To do data transfer via
communication:
PID
parameters,
set
value,
control period
Write the PID control bit
to the modules, realize
the
control
of
the
module
read the PID output value to the local
register in order to control the object,
read the PID parameters and current
value in order to do real time monitor.