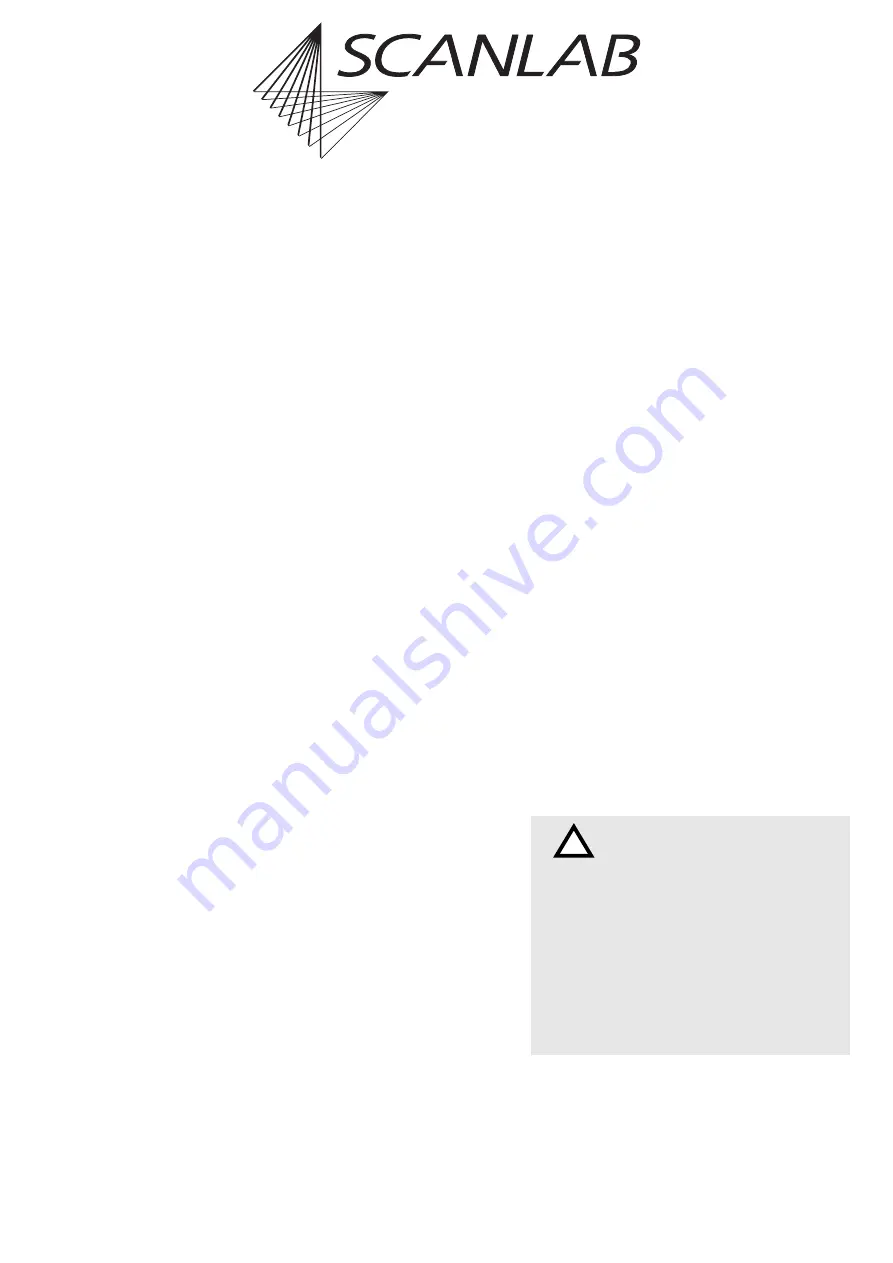
hurry
SCAN
®
10, digital, 1064 nm, f = 254 mm
Rev. 2.6 e
5 Start-up and Operation
27
innovators for industry
within this focus may be more than 1000 times larger
than in the original beam and the effective damage
threshold will be correspondingly reduced. In partic-
ular, the mirrors can be damaged by lasers with high
pulse energies, short pulse lengths and good beam
quality. Contamination on or damage to the optical
surfaces of the objective or protective window can
further increase residual reflectivity, which further
increases the danger of mirror damage from back
reflections.
Furthermore, the specified values only apply to clean
and new mirrors. Mirror contamination (dust, finger-
prints, cleaning residue, deposits from laser
processing etc.) as well as mechanical damage
(scratches, fractures, burn-in, damage by an
improper cleaning procedure) can considerably
reduce the damage threshold.
The specified damage threshold for pulsed operation
is the maximum energy density for which no mirror-
surface damage is expected for the specified wave-
length and for two hundred 10 ns pulses onto the
same mirror spot (see note below).
In general, the damage threshold considerably
decreases with an increasing number of laser pulses.
In continuous operation, SCANLAB therefore recom-
mends only applying suitably reduced energy densi-
ties (depending on the repetition rate and the laser
parameters, typically five times smaller than the spec-
ified pulse damage threshold, if necessary even
smaller).
The damage threshold for pulsed operation also
decreases with decreasing pulse length. In particular,
this effect must be considered for pico- or femto-
second lasers.
Note
: The specified damage threshold energy density corre-
sponds to 0% damage probability (see ISO 11254). Here,
damage means a permanent, laser induced surface modifi-
cation. Test parameters: angle of incidence: 45°; pulse
length (FWHM): 10 ns; beam profile: TEM00; 200 pulses per
test site; inspection method: Nomarski dark field micro-
scope (150x).
5.3 Adjustment and Alignment
To ensure optimum performance of the scanning
system, it is crucial that the laser beam and the scan
head are precisely aligned with respect to each other.
Incorrect alignment might lead to the following
effects:
• vignetting of the laser beam
• a large, irregular spot
• arbitrary translation of the image field
In most cases, vignetting will be the predominant
effect. Vignetting occurs if the laser beam is not able
to fully pass through or be reflected by the optical
components. Part of the beam’s diameter will be cut
off, resulting in power loss and possible system
damage due to excessive absorption of laser power.
To avoid significant vignetting, the system must be
aligned as precisely as possible, particularly in terms
of the beam position relative to the scan head’s
optical axis. If the laser beam profile is Gaussian, the
maximum tolerances appropriate for most applica-
tions are:
If you use a laser with "flat top" beam profile, it can
be necessary to align the system with even higher
precision. Avoid vignetting especially for a high
power laser. Align carefully and
–
if necessary
–
reduce the beam diameter to an appropriate value.
• tilt of the laser beam:
< 5 mrad
• displacement:
< 0.3 mm
Danger!
• Do not stare directly into the laser beam or at
any of its deflected radiation. Keep all parts of
the body away from direct contact with the laser
beam or any of its deflected radiation.
• Adjust the output beam path of the scan head
by means of a laser with a laser class not higher
than 2. If this is not possible, the laser should be
operated at the lowest power. Avoid dangerous
deflected radiation!
!