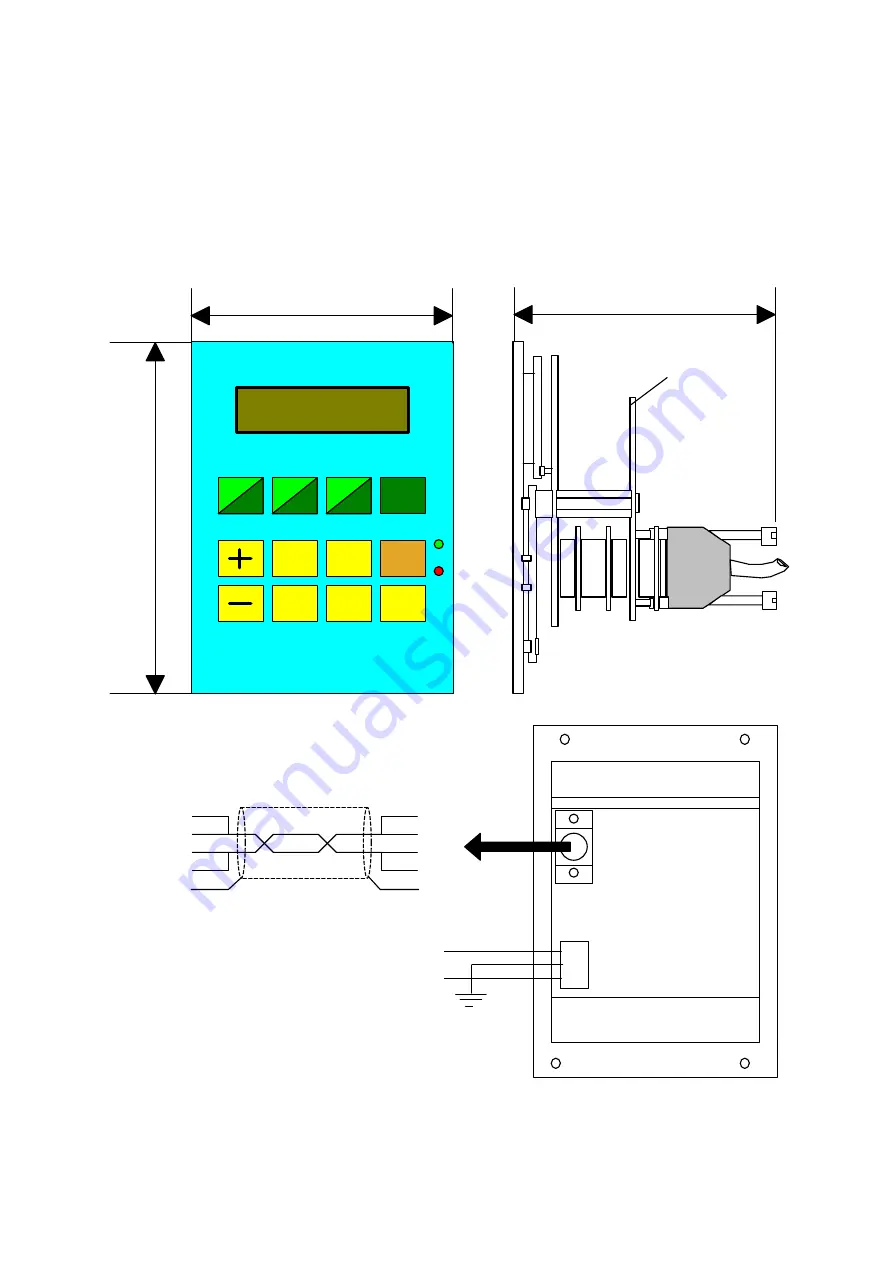
S.B.C. Elettronica S.p.A. - Engineering Division
HPDxxN – High Power User’s Manual
87
Appendix I: remote communications interface
If the application calls for a simple operator interface, use console 048+049+064. The console is
connected to the drive by means of the serial line; it does not provide I/O capabilities and it does not
have buffered memory. The connection cable is not part of the standard supply and the software
must be generated by S.B.C. to client specifications.
F1
F2
F3
F4
SHIFT
F5
F6
A
P
C
S
ESC
START
STOP
128.5
90
90 max
Power supply type 064
1
2
3
power
M1
P2
L1
L2
PE
Rear panel view
4
5
2
3
4
3
1
2
8
8
X5
HPD
connector P2 pins
for burden resistors refer to
Serial line connection