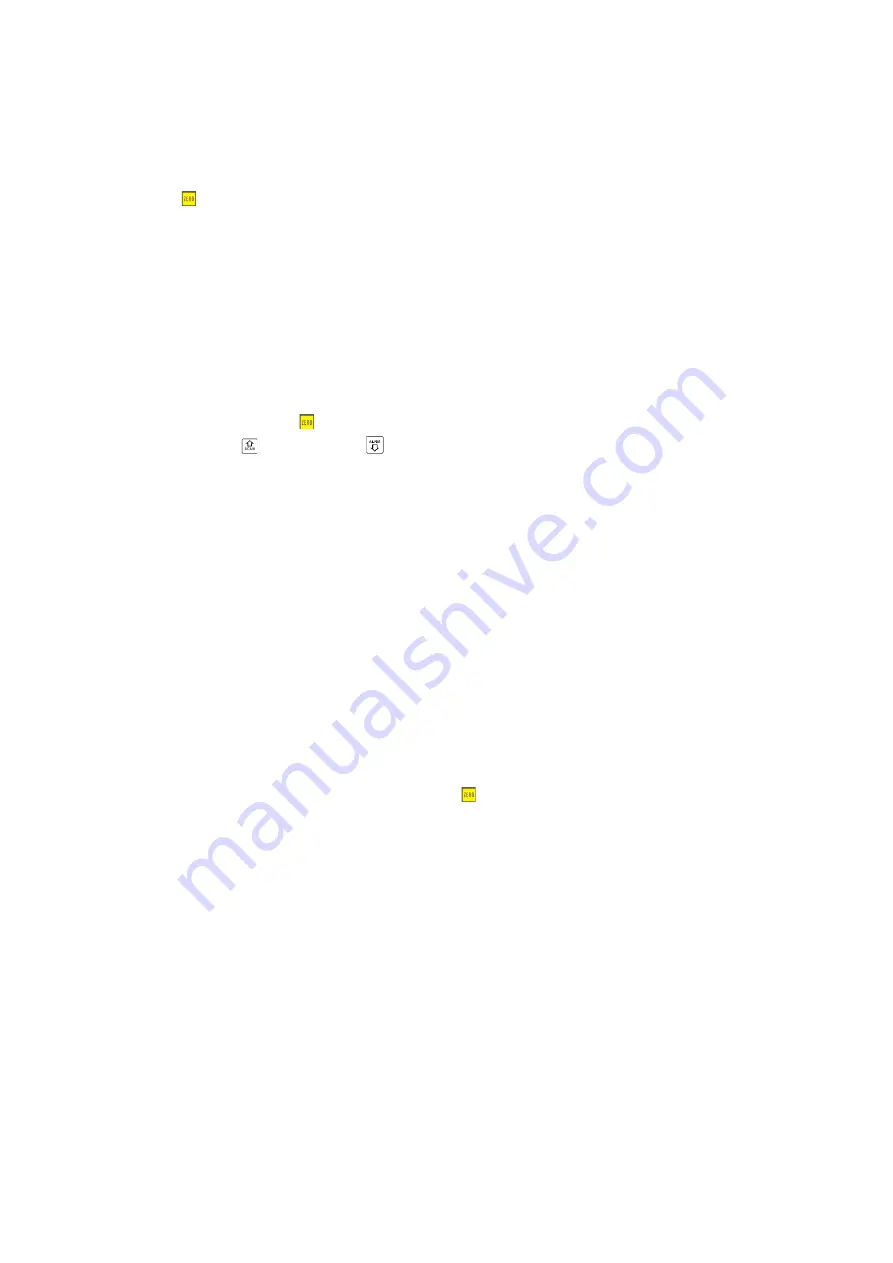
TN_US-BA-e-2020
11
In the device there is a special memory in which all measurements are stored, even
after switching off.
4.2 Sound generator setting (zero setting)
The key
is used to zero the device. This is done almost like with a mechanical
precision measuring instrument (micrometer).
If this is not done correctly, all measurements performed may be incorrect.
When the instrument is zeroed, the specified error value is measured and automatically
corrected for all subsequent measurements.
The procedure is as follows:
1. The sound generator (the ultrasonic probe) is plugged in and the connections
of the plugs are checked. The contact surface of the sound generator must be
clean.
2. Press the key to activate the zero setting mode.
3. The key
and the key
are pressed to display the currently used sound
generator model. Of course, no mistake should be made here, as this is crucial
for the measuring accuracy.
4. A drop of coupling agent is now applied to the metal zero plate.
5. The ultrasonic probe is carefully pressed onto the zero plate and should lie flat
on this surface. Now the value 4mm appears because the zero plate is 4mm
thick and the instrument is now calibrated to this value.
6. Now the ultrasonic probe is lifted off the zero plate.
The instrument has now recognized the initial error factor and will use it to adjust all
subsequent measurements. When zeroing, the instrument will always use the sound
velocity of the built-in zero plate, even if other values have been previously entered to
make current measurements.
Although the last zero setting is saved, it is recommended to do it again each time the
unit is switched on, even if a different sound generator is used. This will ensure that
the unit is always set correctly. Pressing the button cancels the current zero setting.
The instrument returns to the measuring mode.
4.3 Sound velocity
In order to be able to make exact measurements, this must be adjusted to the speed
of sound of the corresponding material. Different materials have different sound
velocities.
If this is not done, all measurements will be faulty by a certain percentage.
One-point calibration
is the most common way to optimize linearity over a long range.
Two-point calibration
allows higher accuracy at a shorter range by calculating the
zero setting and the speed of sound.
Note:
For
one-point and two-point calibrations,
paint or coating must be removed
in advance. If this is not done, the calibration result will consist of a kind of "multi-
material sound velocity" and will certainly not be the same as that of the actual material
to be measured.