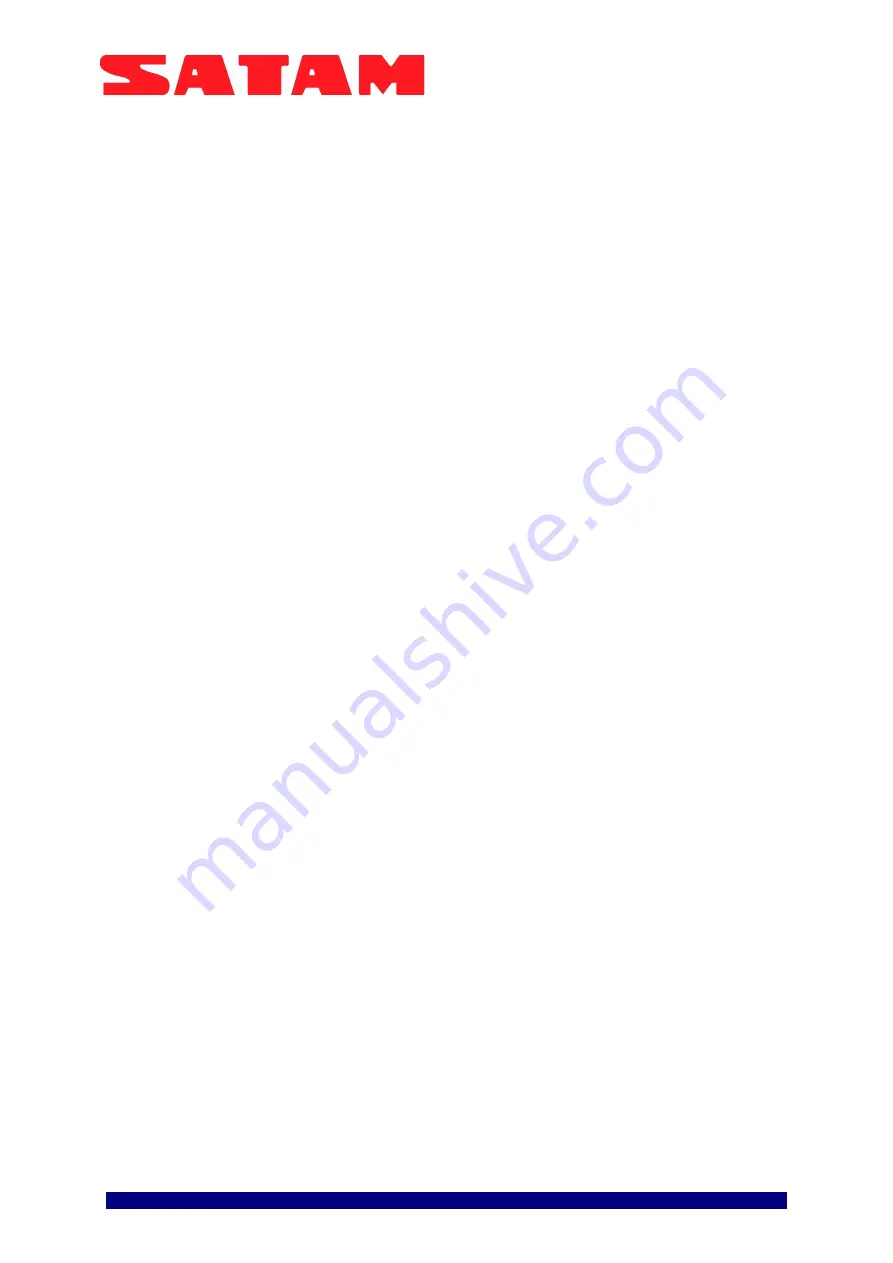
Edition du 24/02/09
/ 17
U508218-e Revision : 2
6
3. PERIODIC INSPECTION
3.1. GENERAL.
The Meter Register is fully lubricated and properly
adjusted
at
manufacture.
However,
periodic
cleaning a}\d lubrication are required.
Judgement of the intervals at which the meter
register requires such service must necessarily be
left to the individual user due to varying conditions
of service. Under normal conditions, this will be at
least once a year, or after each 2-1/2 million units of
measure delivered, whichever comes first.
3.2. DISASSEMBLY PRIOR TO CLEANING.
Remove the meter register from its housing as
follows:
1. Remove the bolts securing the cover (if present)
to the top of the housing. These bolts are hex head
and are located at the four corners of the bottom of
the housing. Remove the cover.
2. Remove the three button-head bolts securing the
meter register to the housing. Remove the meter
register.
3. Remove the screws securing the gear plate to the
bottom of the housing. Remove the gear plate.
3.3. CLEANING.
CAUTION: DO NOT USE A WIRE BRUSH.
1. Wipe bezel crystal with a clean lint-free rag.
2. If the wheel faces are dirty, gently clean with a
clean lint-free rag dipped in mild soapy water.
3. Clean the gears on the base plate by flushing or
with a brush dipped in solvent. Blow dry with
compressed air.
4. Clean Housing by dipping, flushing or brushing
with solvent. Blow dry with compressed air.
3.4. INSPECTION.
A periodic inspection of the en tire meter register,
housing and gear plate is required to make sure that
they function properly, parts are in place, and no
binding or excessive side-to-side motion of shafts
occurs. A checklist on such procedures follows:
1. Check the following shafts for perceptible side-to-
side motion.
Note: Remove the meter register from the housing
before checking shaft freedom.
a. Wheel Shaft
b. Anti-Topping Finger Group Shaft
c. Reset Finger Group Shaft
d. Clutch Group Shaft
e. Pinion Shaft
2. Temporarily install the base plate and meter
register in the housing and check for proper
engagement and freedom of movement of:
a. AlI gears on gear plate.
b. Output bevel gear on gear plate with the bevel
drive gear on drive shaft.
c. 57 tooth gear on clutch assembly with gear on
right wheel assembly.
d. Gear drive shaft with gear train that operates the
totalizer, and gear connecting the drive train to the
totalizer.
3. Rotate drive shaft by hand to see that unit
operates freely and then reset, checking for proper
reset and shutter action. Adjust pointer alter reset as
required.
4. Check ail screws, retaining rings and groove pins
to see that they are tight and seated properly.
3.5. LUBRICATION.
1. Recommended Lubricants
Note: Chemlube and Vischem products are
manufactured by Ultrachem Inc.,
1400 N. Walnut St., P.O. Box 2053
Wilmington, DE 19899
Oil: Chemlube 201 or equivalent with a temperature
range of -65°F to +275°F (-54°C to + 135°C).
Grease: Vischem 352 or equivalent with a
temperature range of -65°F to +3000F (-MOC to +
149°C).
Note: All lubricants used in the register must be of a
type which remains fluid over the full temperature
range to which the register will be subjected. Also,
they should not oxidize or dry out leaving a gummy
or perceptible residue.
If the Chemlube 201 oil lubricant is not available, a
substitute with equivalent properties may be used.
To assist field personnel in obtaining suitable
lubricants for the meter register and ticket printers,
the following list showing equivalent lubricants has
been prepared:
OIL
AEROSHELL FLUID
NO. 3
REGENT SPINTEX OIL
60
GARGOYLE ARCTIC OIL
LIGHT
CASTROL HYSPIN
40
ANDEROL
40lD
GREASE
AEROSHELL
14
ESSO BEACON
325
ANDEROL
795
2. Points to Lubricate
Oil: Ali points indicated as "Oil" on Figure 6 should
be lubricated with oil as described above. This
includes ail shafts, studs, and bosses on which a
moving part bears.
Grease: Grease should be applied to ail points
indicated as "Grease" on Figure 6. This includes
gears and the no-back ratchet and pinion.
Note: The oil and grease should be applied with a
small brush to make certain that ail areas will be
properly lubricated. In this manner, the amount of
lubricant being used will be more easily controlled.