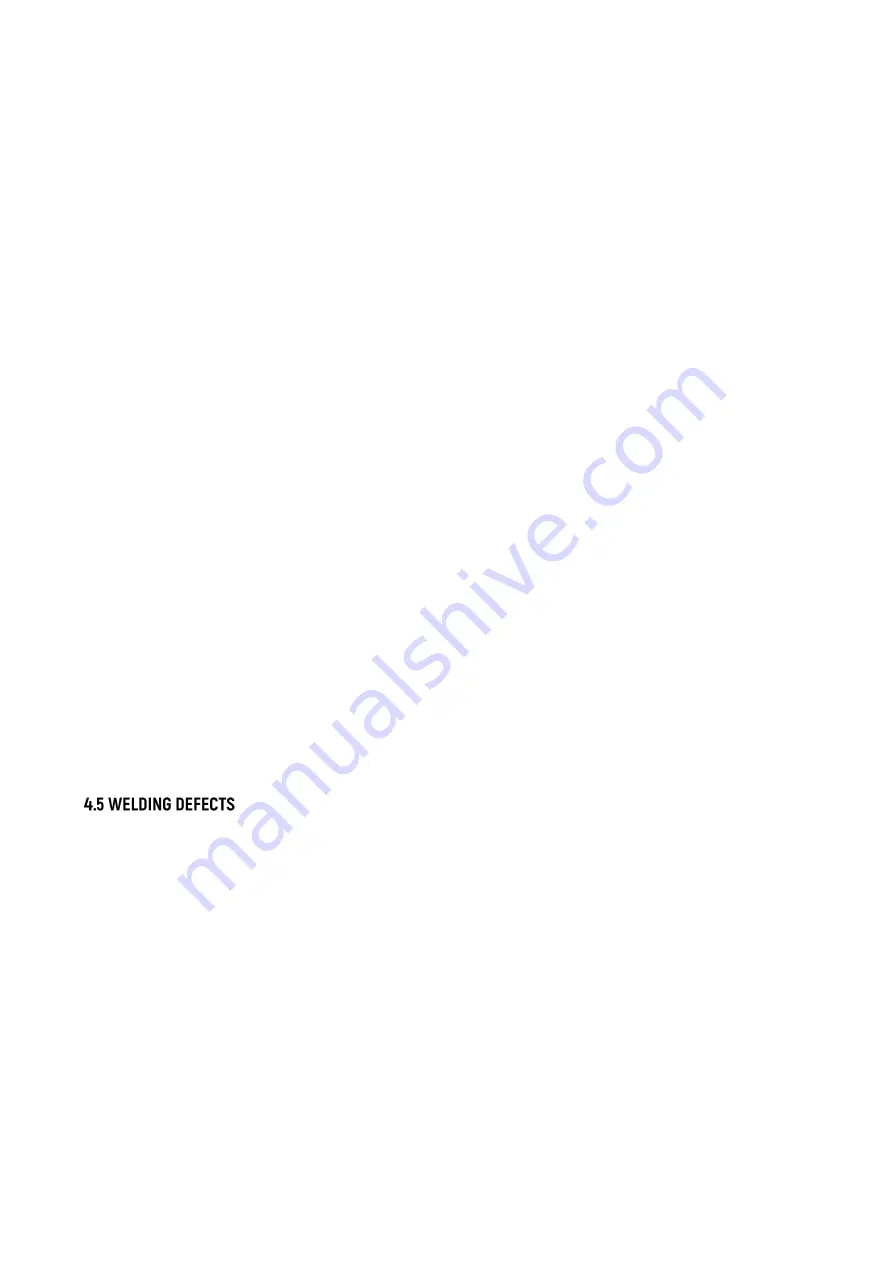
15
4.4.5 WELDING ALUMINIUM
The following is required for aluminium welding:
1) 100% Argon as welding protection gas.
2) A torch wire of composition suitable for the basic material to be welded.
For ALUMAN welding wire 3.5% silicon.
For ANTICORODAL welding wire 3.5% silicon.
For PERALUMAN welding wire 5% magnesium.
For ERGAL welding wire 5% magnesium.
3) A torch prepared for aluminium welding.
If you only have a torch for steel wires, the same shall be modified in the following way:
- Make sure that length of torch cable does not exceed 118 inches (it is advisable not to use longer torches).
- Remove the brass sheath-holding nut, the gas and the current nozzles, then slip the sheath off.
- Insert the teflon sheath for aluminium and ensure it protrudes from both ends.
- Screw the current nozzle so that the sheath adheres to it.
- Insert the sheath holding nipple, the O-Ring in the free end of the sheath and secure with the nut without
tightening too much.
- Slip the brass tube on the sheath and insert both into the adapter (after removing the iron tube which was
fitted inside the adaptor).
- Cut the sheath diagonally so that it stays as close as possible to the wire slide roller.
4) Use drive rolls that are suitable for aluminium wire. The drive rolls, when being installed, must be
tightened as tight as possible.
5) Use contact tips that are suitable for aluminium wire and make sure that the diameter of the contact tip
hole corresponds to the wire diameter that is going to be used.
6) Use abrasive grinders and tool brushes specifically designed for aluminium. Never use these tools on
other materials. REMEMBER that cleanliness equals quality.
The wire spools must be stored in plastic bags with a dehumidifier.
1- DEFECT- Porosity (in, or on the surface of the weld bead)
CAUSES Bad wire (rust on the surface).
Insufficient gas shielding due to:
- Inadequate gas flow due to a block in the gas line.
- Defective flowmeter.
- Gas regulator covered with frost because a gas heater was not used to heat the
CO2 shielding gas.
- Failure of gas valve solenoid.
- Gas nozzle plugged up with spatter.
- Gas flow holes plugged up.
- Air drafts in the welding area.
2- DEFECT- Shrinkage Cracks
CAUSES Welding wire or work to be welded dirty or rusty.
Содержание AE7022
Страница 1: ...V AR 7022 1903 01 AE7022 ...
Страница 2: ...2 ...
Страница 3: ...3 ...
Страница 4: ...4 ...
Страница 5: ...5 I J K L B A C D E F G H ...
Страница 6: ...6 A E F B C D G ...
Страница 7: ...7 ...
Страница 8: ...8 ...
Страница 10: ...10 ...
Страница 17: ...17 A E F B C D G ...
Страница 22: ...22 AE7022 V AR 7022 1903 01 988 5 12 201802 86 21 6061 1919 86 21 6061 1918 www satatools com ...