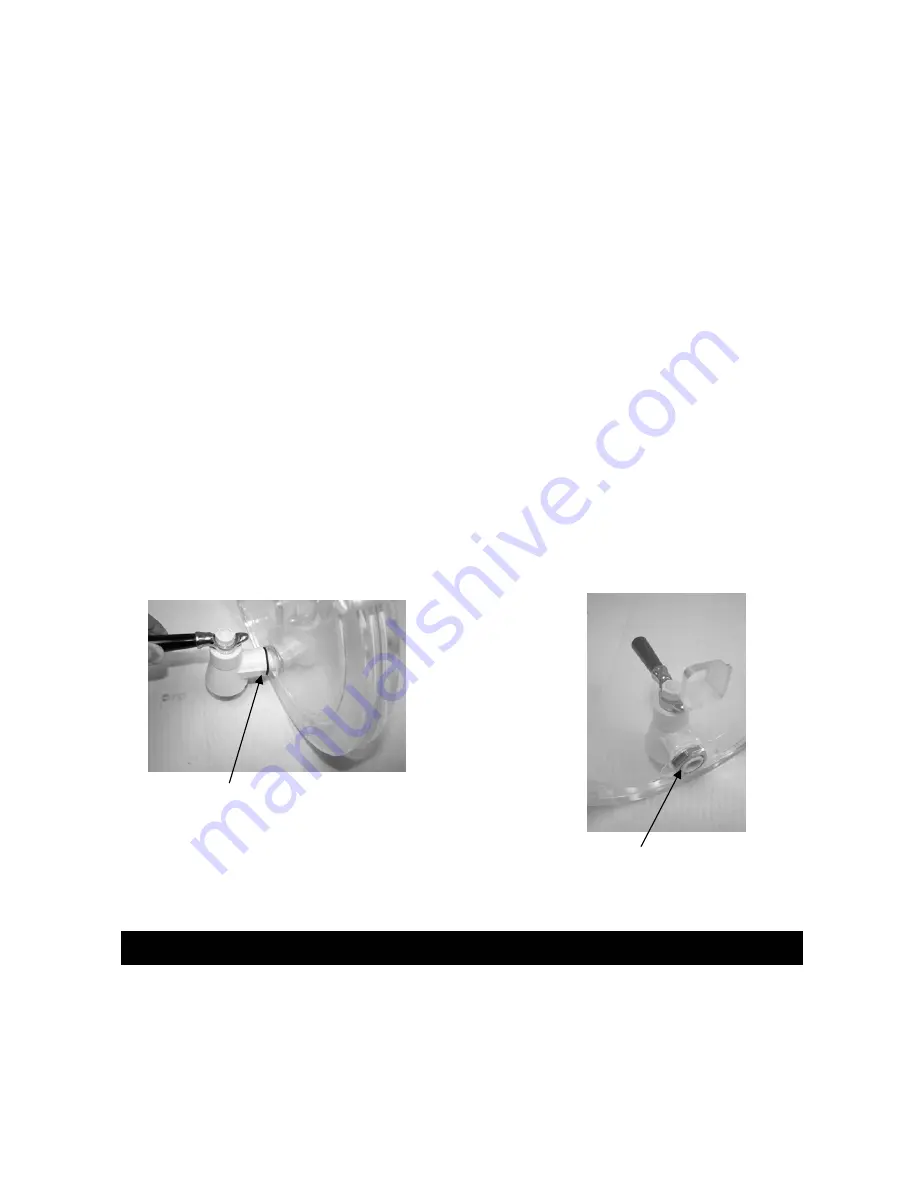
Autofill
System Installation
1. Connect
the
premix
line from the remote fill sys-
tem to the 3/8" barbed fitting located at the rear
of the remote dispensing head.
Oetiker®
clamps are required to contain the working
pressures of the system. Pressurize the line.
2. Activate
the
autofill
system by pressing the fill
switch located on the front panel of the dispens-
ing head
3. Purge the line by allowing the mix pan to fill until
the
system
probes close the fill switch solenoid
valve.
4
Assemble gasket on spigot side.
Warning: Machine damage possible if nut installed incorrectly!
Lubricate flat side of nut with Sani-Gel.
Install flat side of nut toward spigot.
Spigot Assembly