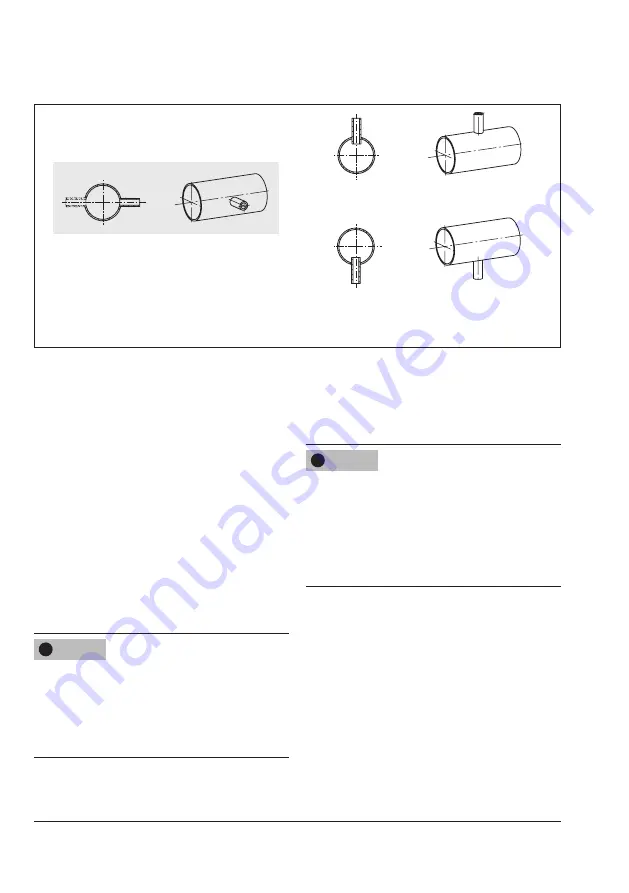
26
EB 3131 EN
Mounting and start-up
Correct
Incorrect
Connection at the top – incorrect position
Incorrect
Connection at the side – optimal
Connection at the bottom – incorrect position
Fig. 6:
Control line connection, depending on how the pipeline is routed
5.3
Putting the regulator into
operation
Î
First start up the regulator after mounting
all parts.
Î
Make sure the control lines are open and
correctly connected.
Î
Make sure that the restriction (1.2) is
open while filling the plant. Turn the set
point screw (17) counterclockwise (
) as
far as it will go.
Î
Open the shut-off valves slowly over a
time period of several minutes, prefera-
bly starting from the return flow pipe.
Risk of valve damage due to a sudden pres-
sure increase and resulting high flow veloci-
ties.
Slowly open the shut-off valve in the pipeline
during start-up.
NOTICE
!
Pressure testing the plant
All plant components must be designed for
the test pressure. Remove the regulator from
the pipeline, if necessary.
Risk of damage to the diaphragm actuator
due to impermissible excess pressure.
The test pressure must not exceed the nomi-
nal pressure at the actuator by 1.5 times on
testing the pressure of the plant when the
regulator is already installed.
Rinsing the plant
1.
After filling the plant, first completely
open the consumer
2.
Adjust the maximum flow rate at the reg
-
ulator (see section 6.1.1).
3. Adjust the maximum differential pressure
at the regulator (see section 6.1.2).
4.
Rinse out the pipeline at full flow rate for
several minutes.
NOTICE
!