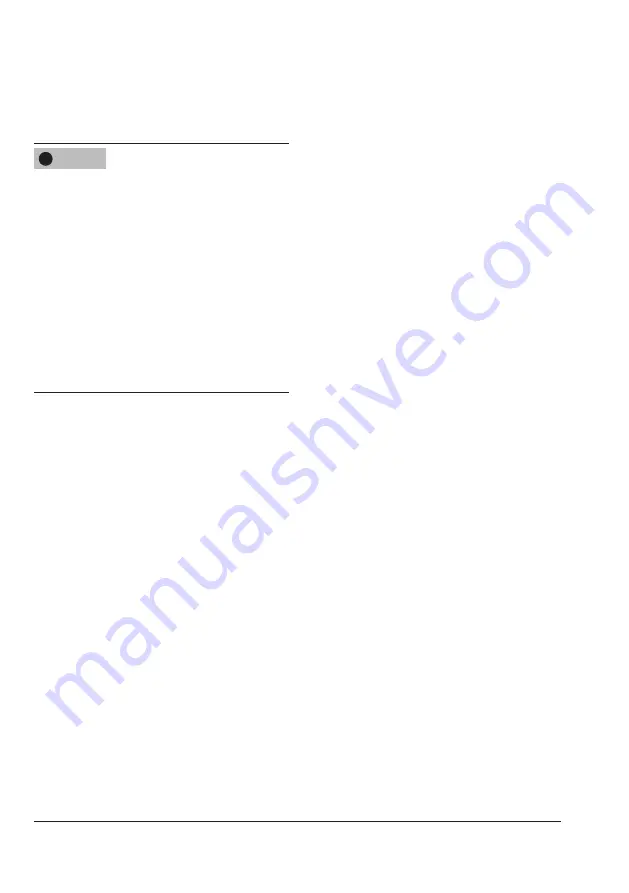
9-10
EB 8072 EN
Servicing
9.4.3 Replacing the packing
Risk of control valve damage due to incor-
rect servicing.
Î
The packing can only be replaced when
all the following conditions are met:
− The valve does not have a balanced
plug.
− The valve does not have a bellows
seal.
− The standard, form HT or ADSEAL
packing is installed in the valve.
Î
To replace the packing in other valve
versions, contact our after-sales service.
a) Standard packing (PTFE)
1.
Unscrew the castellated nut (92) and take
the yoke (60) off the bonnet (2).
2. Undo the body nuts (14) gradually in a
crisscross pattern.
3.
Lift the bonnet (2) and plug with plug
stem (5) off the body (1).
4.
Replace the gaskets (see section 9.4.2).
5. Unscrew the stem connector nut (9) and
lock nut (10) from the plug stem.
6. Unscrew the threaded bushing (8).
7. Pull the plug with plug stem (5) out of the
bonnet (2).
8. Pull the entire packing out of the packing
chamber using a suitable tool.
9. Renew damaged parts. Carefully clean
the facing (DF 10) in the packing cham-
ber.
10.
Apply a suitable lubricant to all the pack-
ing parts and to the plug stem (5).
11.
Slide the plug with plug stem (5) into the
bonnet (2).
12. Make sure that the seat (4) and seat re
-
tainer (124) are still clamped correctly
on the body.
13. Place the bonnet (2) together with the
plug stem and plug (5) onto the body.
Make sure that an opening of the seat re
-
tainer (124) faces toward the valve out
-
let.
Version with V-port plug:
place the bon
-
net onto the valve body, making sure
that the largest V-shaped port of the
V-port plug faces towards the valve out-
let.
Version with perforated plug:
place the
bonnet onto the valve body, making sure
that the hole of the plug that releases the
flow first faces toward the valve outlet.
See relevant information under 'Mount
-
ing the actuator onto the valve' in the 'In
-
stallation' section.
14.
Carefully slide the packing parts over the
plug stem into the packing chamber us
-
ing a suitable tool. Observe the proper
sequence (see Fig. 9-6).
15. Firmly press the plug (5) into the seat (4).
Fasten down the bonnet (2) with the
body nuts (14). See section 9.4.6.
16. Screw in the threaded bushing (8) and
tighten it. Observe tightening torques.
17. Place yoke (60) on the bonnet (2) and
fasten using the castellated nut (92).
NOTICE
!
Содержание 3291
Страница 14: ...1 10 EB 8072 EN...
Страница 30: ...4 6 EB 8072 EN Shipment and on site transport...
Страница 56: ...8 4 EB 8072 EN...
Страница 82: ...12 2 EB 8072 EN...
Страница 84: ...13 2 EB 8072 EN...
Страница 86: ...14 2 EB 8072 EN...
Страница 87: ...EB 8072 EN 14 3...
Страница 88: ...14 4 EB 8072 EN...
Страница 91: ...EB 8072 EN 15 3 Annex...
Страница 95: ......