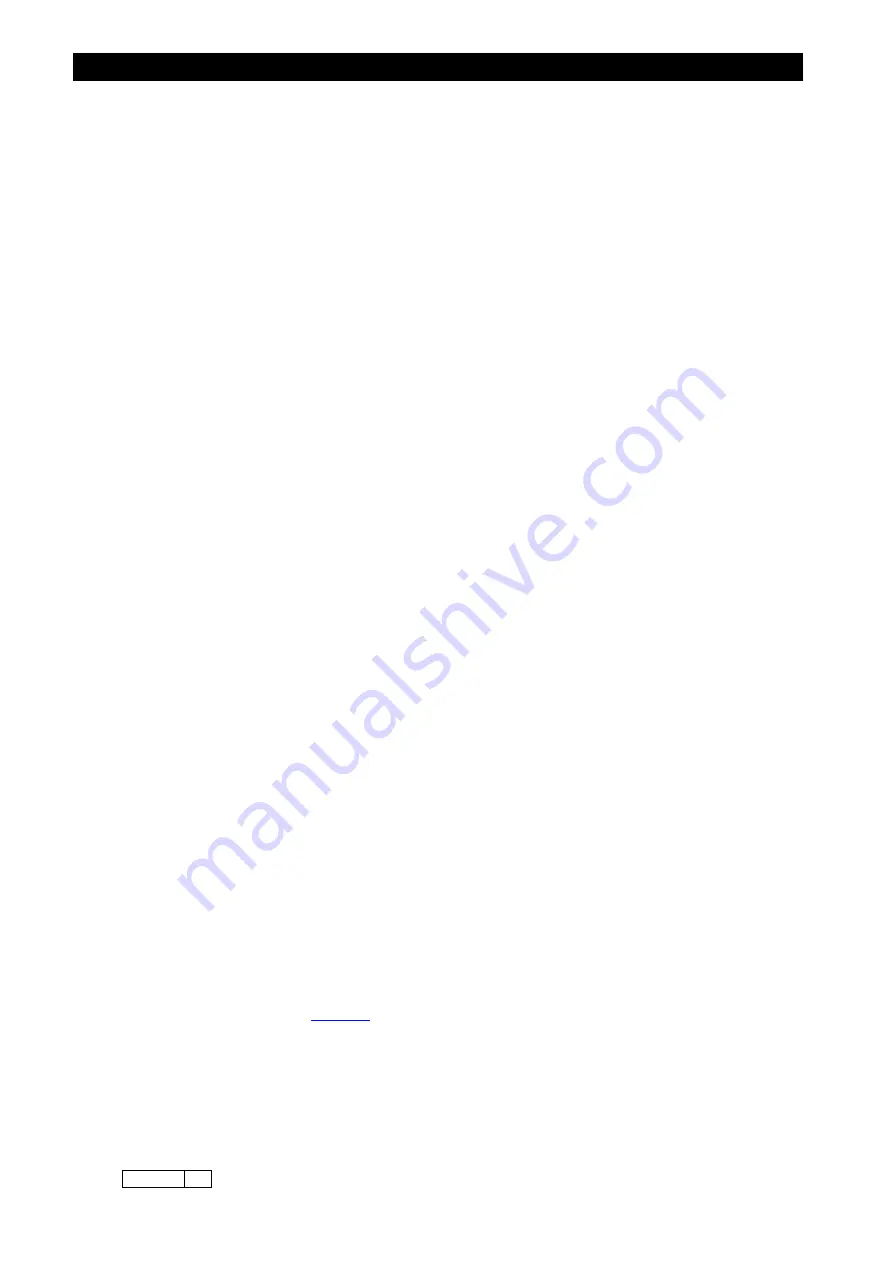
Testing the DFC Console:
If there are two or more DFC Consoles at the facility, try unplugging the Pigtails and swapping
the Consoles, this will show if the problem is with the Console or with the Wiring/Impulse
Meter/Solenoid(s).
To check that the DFC Console is counting properly, remove the pigtail plug at the back of the
console and plug in a spare pigtail. Authorize a ONE UNIT (1.0) (Quart/Liter/Pint/Gallon) dispense
and then touch the to Impulse Meter wires (Solid Red and Red/White Tracer) together ten times.
If the DFC Console is functioning properly the Pre-Set counter will advance one digit each time
the wires are touched together and on the tenth contact the DFC ready light will extinguish and
the Pre-Set counter will read 1.0. If a spare pigtail is not available, disconnect the Solid Red and
the Red/White Tracer wires at the Junction Box adjacent to the DFC Console to perform the test
with the original pigtail plugged into the Console.
If the DFC Console continually blows fuses, the System is most likely mis-wired or less possibly a
Solenoid or Ready Light is defective.
To check the voltage output to the solenoids and the station selector knob, remove the pigtail
plug at the back of the console and plug in a spare pigtail. Authorize a dispense on the DFC
Console and using a multi-meter check the voltage from the color coded station wire to the
Solenoid ground wire (Black). Check each station in turn, the color codes on the list should match
the Station Selector knob position and the reading on the multi-meter should be 24 Volts AC at
each station indicated by the Station Selector knob, and zero at the others.
Testing the Impulse Meter:
Make a mark on the top of one of the lobes of the cam on the Impulse Meter and a
corresponding mark on the body of the Impulse Meter. Authorize a dispense of ONE UNIT (1.0)
at the DFC Console and then pump the product. The mark should have made one complete
revolution and returned very closely to the original position marks.
Disconnect the wire terminals at the Impulse Meter and attach a multi-meter to the two outside
spade terminals at the micro-switch. Authorize a dispense at the DFC Console, open the dispense
point and while the product is being pumped monitor the action of the micro-switch. There
should be clean contact shown on the multi-meter as each lobe of the cam passes the micro-
switch. The micro-switch is mounted on a plastic adjusting base; if the pulses are uneven adjust
it appropriately in or out until the Impulse Meter pulses perfectly. Reconnect the wires at the
Impulse Meter and then disconnect the Impulse Meter wires at the junction box adjacent to the
DFC Console. Perform the same test to see if there is a defect in the wires running from the DFC
Console to the Impulse Meter.
Testing the Solenoid(s):
Model 1065 does not test properly with a conventional multi-meter. It is internally rectified
and shows infinite resistance normally. A steady resistance reading in the range of 0
Ω
to
50
Ω
indicates a shorted coil. When the DFC console energizes the Fluid Solenoid assembly,
there is an audible ‘CLICK’.
Model 1064 shows a resistance reading of
≈
4.1
Ω
when disconnected from the System. When
the DFC console energizes the Solenoid assembly, there is an audible ‘CLICK’.
Monday Morning Syndrome:
Any Pump suction tube longer than two feet must be equipped with a foot valve for the DFC System to
function properly. If the System performs erratically sometimes, giving a one or a few dispenses that are
under the authorized amount and then mysteriously returns to normal, the cause can often be traced to
the Pump rather than the System. Even with a perfectly sealed suction tube, extended periods of idle time
can allow a gas pocket to form at the top of a long suction tube not equipped with a foot valve – the
negative pressure of the column of oil inside the suction tube allows the lighter fractions of the oil (and
any air dissolved in the oil) to ‘
’ out of the oil and create a gas pocket at the top of the suction
tube under the foot valve at the base of the stub pump. When this pocket of gas is pumped through the
Impulse Meter it ‘zings’ the meter, giving a false reading and an under-delivery of oil on that dispense; the
System then returns to normal. This condition worsens as the oil level in the tank drops, a full tank may
mask the condition for a period of time until the tank level drops again. Once the gas pocket enters the
system piping, it is not unusual for the gas to re-dissolve back into the oil (since the oil is under pressure
from the pump) and not show up as foaming or ‘spitting’ at the Dispense Point (Station), making this
condition very difficult to diagnose in the field. An improperly sealed suction tube causes this problem with
quite a bit of frequency, and generally shows up as ‘spitting’ or foaming at the Dispense Point (Station).
1060
8
Special Diagnostic Procedures Continued
Samson Corporation-Swannanoa, NC 28778-
800.311.1047 www.samsoncorporation.com