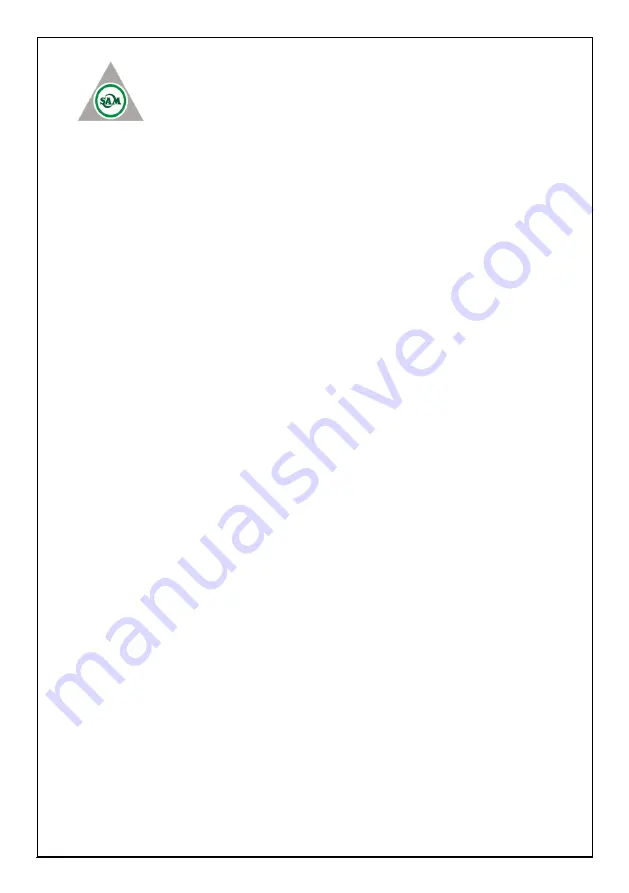
2
WARRANTY
We warranty that the pump supplied by us is free defective
material and faulty workmanship. This warranty holds good
for a period of 12 months from the date of commissioning of
the equipment or 18 months from the date of dispatch from
our factory, whichever is earlier.
Our liability in respect of any complaint is limited to replacing
part/parts free of charge ex-works or repairs of the defective
part/parts only to the extent that such replacement/repairs
are attributable to or arise solely from faulty workmanship or
defective material.
We warranty the materials for the chemical composition and
mechanical properties of the relevant standard only and not
for corrosion and erosion.
The warranty holds good only for the products manufactured
by us.