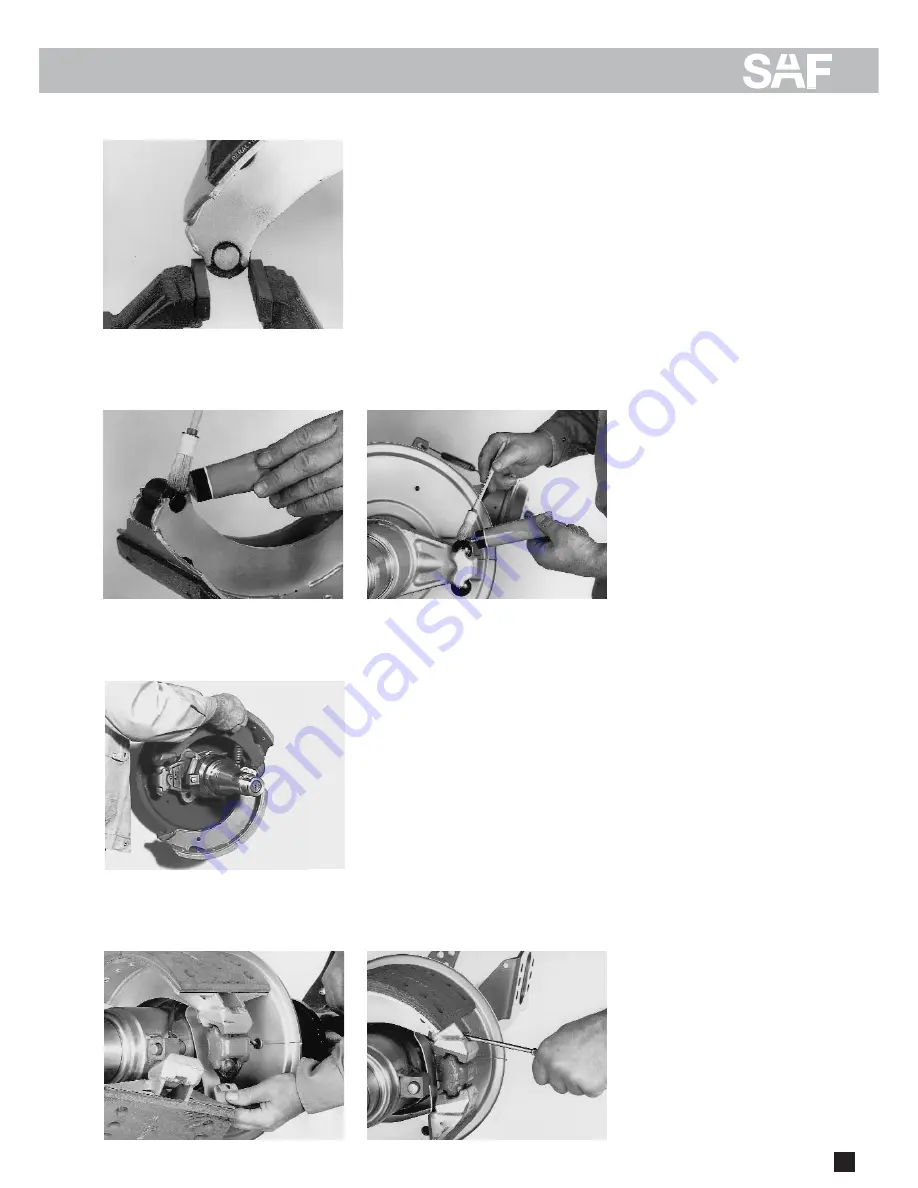
19
E) Installation instructions
Check the proper mounting of the cam roller on the brake shoes.
The cam roller must not jam in the mounting. It must turn easily, but
without radial clearance.
Replace the cam roller if the journal is severely worn.
When installing new cam rollers, a secure mounting in the brake shoe
can be achieved by pressing in the two side faces in a vice.
Apply copper paste to the brake shoes, to the ball surface and to the
two journals of the cam roller.
See chapter “Maintenance instructions” for recommended media.
Apply copper paste to the two
balls in the brake carrier.
See chapter
“Maintenance instructions”
for recommended media.
Hook a new return spring into the tabs of the brake shoes.
Position the upper brake shoe on the ball pivot point and the cam
roller surface.
Suspend the spring clip on the upper brake shoe.
Tilt the lower brake shoe towards the cover plate until the correct
seating on the cam and on the ball pivot point is achieved; if
necessary, turn the camshaft into the required position. Insert the
spring clip into the groove on the lower brake shoe and hook into
the retainer on the upper brake shoe using a screwdriver.
Ensure that the spring clip is
fitted securely.
Check the assembly and the
proper operational condition
of the installed brakes.
Turn the camshaft by actuating
the slack adjuster by hand and
check the correct positioning
and smooth return of the
brake shoes; readjust the
camshaft bearing, if necessary.