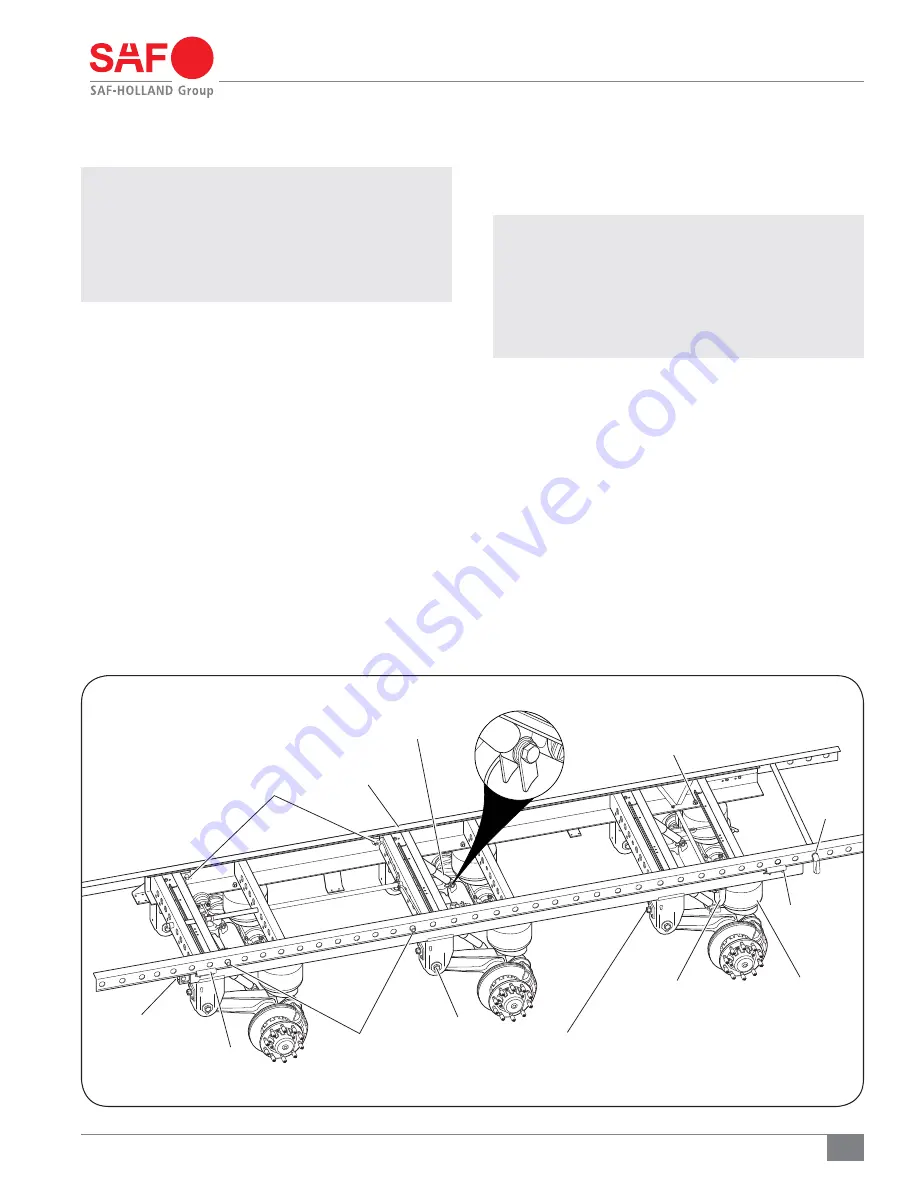
13
XL-AS20012BM-en-US Rev B · 2014-05-28 · Amendments and Errors Reserved · © SAF-HOLLAND, Inc., SAF-HOLLAND, HOLLAND,
SAF, and logos are trademarks of SAF-HOLLAND S.A., SAF-HOLLAND GmbH, and SAF-HOLLAND, Inc.
Pre-Operation Information
11. Pre-Operation
NOTE:
In the United States, workshop safety requirements
are defined by federal and/or state Occupational
Safety and Health Act. Equivalent laws may exist
in other countries. This manual is written based
on the assumption that OSHA or other applicable
employee safety regulations are followed by the
location where work is performed.
1. With the vehicle on a level surface, bring air system to
operating pressure, above 85 psig/5.9 bars.
2. Shut off the vehicle and inspect all air control system
fittings for air leaks by applying a soapy water solution
and checking for bubbles at all connections and fittings.
Examine the air springs
(Figure 18)
for equal firmness.
3. Check the shock absorbers for proper installation and make
sure that the upper and lower 3/4" shock absorber nuts
BSFUPSRVFEUPGUMCT /tN
(Figure 18)
.
4. Verify that the 1/2" air spring mounting nuts are torqued to
GUMCT /tNBOEUIFBJSTQSJOHNPVOUJOH
OVUTBSFUPSRVFEUPGUMCT /tN
(Figure 18)
.
5. With the suspension at full capacity, check that there is a
1" (25 mm) minimum clearance around the air springs.
6. The suspension’s ride height should be within ±1/4" (6 mm)
of the recommended design height. For proper height,
refer to Slider Assembly Section 8.
7. Verify that the 1-1/8" pivot nut are torqued to 550-600 ft.-lbs.
/tN
(Figure 18)
.
IMPORTANT:
The
SwingAlign
™
design maintains proper
alignment under correct torque without
welding; DO NOT weld
(Figure 18)
.
NOTE:
SwingAlign
™
pivot connections are on roadside
and fixed alignment pivot connections are on
curb-side. For SwingAlign
™
Connection Axle
Alignment procedure, refer to Section 9.
8. If your vehicle is equipped with a PosiLok
™
feature, make
sure there is a 1" (25 mm) minimum clearance between
the bottom of the flipper plate and the top of the beam
pad when at ride height
(Figure 18)
; Refer to PosiLok
™
Installation and Operation Manual XL-AR408 for more
information. Available at www.safholland.us or contact
SAF-HOLLAND
®
Customer Service at 888-396-6501.
9. Check that the slider locking pins, slider pull-bar mechanism,
and slider wear pads
(Figure 18)
are operating properly.
For slider repositioning instructions, see procedures
described in Section 12 of this manual.
10. Inspect the front and rear hold down clips
(Figure 18)
to make sure that they are correctly secured around the
slider body rails. Torque all 1/2" hold down clip nuts
UPGUMCT /tN
Figure 18
AIR SPRING
MOUNTING NUT
SHOCK ABSORBER NUT
REAR HOLD
DOWN CLIP
MANUAL
STOP BAR
OPTIONAL
AIR RELEASE
SHOCK ABSORBER
SLIDER
BODY RAILS
SLIDER LOCK PINS
AIR SPRING
OPTIONAL
POSILOK
™
FLIPPER PLATE
SWINGALIGN
™
ADJUSTMENT NUT
1- 1/8"
PIVOT NUT
FRONT HOLD
DOWN CLIP
SLIDER LOCK PINS