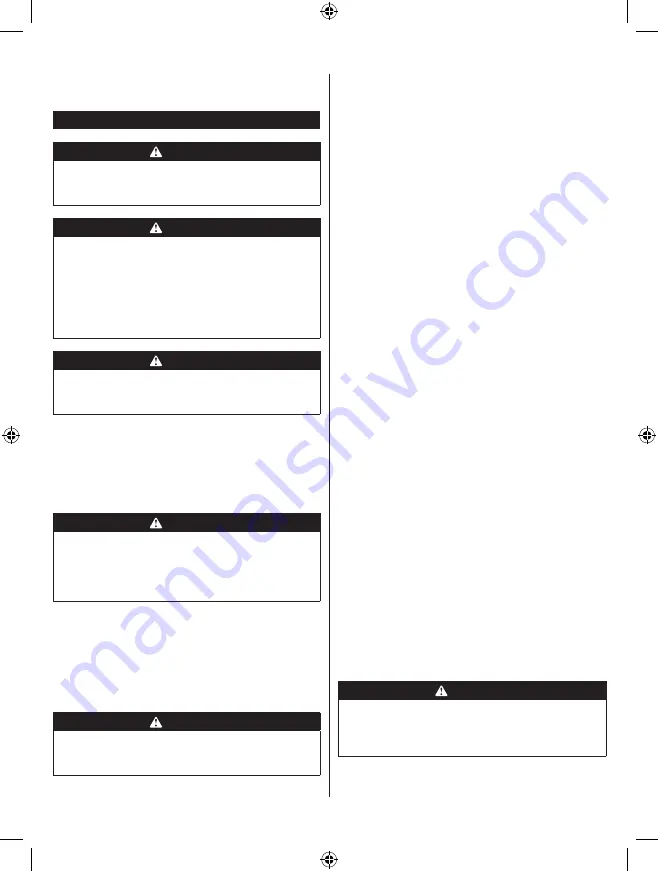
8
7. Reconnect the tool to the air supply.
8. Reinstall fasteners.
MAINteNANce
wARNINg
When servicing use only identical replacement parts.
Use of any other parts may create a hazard or cause
product damage.
wARNINg
Always wear eye protection with side shields marked to
comply with one of the following standards:
● Australian Standard – AS/NZS 1337
● European Standard – CE EN166
● American Standard – ANSI Z87.1
Failure to do so could result in objects being thrown into
your eyes resulting in possible serious injury.
wARNINg
Disconnect the tool from the air supply and empty the
magazine before performing maintenance. Failure to do
so could result in serious personal injury.
geNeRAl MAINteNANce
Avoid using solvents when cleaning plastic parts. Most
plastics are susceptible to damage from various types of
commercial solvents and may be damaged by their use.
Use clean cloths to remove dirt, dust, oil, grease, etc.
wARNINg
Do not at any time let brake fluids, gasoline, petroleum-
based products, penetrating oils, etc., come in contact
with plastic parts. Chemicals can damage, weaken or
destroy plastic which may result in serious personal
injury.
cOlD weAtheR OpeRAtION
For cold weather operation, near and below freezing,
the moisture in the air line may freeze and prevent tool
operation. We recommend the use of air tool lubricant or
permanent antifreeze (ethylene glycol) as a cold weather
lubricant.
wARNINg
Do not store tools in a cold weather environment to
prevent frost or ice formation on the tools’ operating
valves and mechanisms that could cause tool failure.
NOte:
Some commercial air line drying liquids are harmful
to “O” rings and seals. Do not use these low temperature
air dryers without checking compatibility.
AIR sUpply pRessURe AND vOlUMe
Air volume is as important as air pressure. The air volume
supplied to the tool may be inadequate because of
undersize fittings and hoses, or from the effects of dirt and
water in the system. Restricted air flow will prevent the tool
from receiving an adequate volume of air, even though
the pressure reading is high. The results will be a slow
operation or reduced driving power. Before evaluating tool
problems for these symptoms, trace the air supply from
the tool to the supply source for restrictive connectors,
low points containing water and anything else that would
prevent full volume flow of air to the tool.
ReqUIReD DAIly checKlIst
1. Disconnect the air supply from the tool and remove
all fasteners.
2. Check all screws, nuts, bolts, and pins on the tool. If
any of these are loose, they must be tightened with the
appropriate size wrench.
3. Press the safety yoke against a workpiece to ensure
that it moves smoothly.
4. With the safety yoke depressed, pull the trigger. The
trigger should move smoothly, without binding.
5. While the tool is not loaded, connect the appropriate
air supply at 5.5 bar (80 psi) to the tool.
● Without pulling the trigger, press the safety yoke
against a workpiece several times. The tool must
not operate.
● With the safety yoke not engaged on the workpiece,
point the tool down and away from you and other
persons, and pull the trigger several times. Hold
the trigger in this position for a minimum of 5
seconds. The tool must not operate.
● Press the safety yoke firmly against the workpiece,
and pull the trigger. The tool must operate.
● With the safety yoke still depressed, release the
trigger. The driver must return to its up position.
6. If the tool successfully meets all the requirements
in this checklist, it is ready for use. Load the proper
fasteners for the desired application.
7. Set the depth of drive according to the “drive depth
adjustment” section in this manual. Repeat this
checklist before using the tool each day, or if the tool is
dropped or damaged in any way.
wARNINg
Do not use any attachments or accessories not
recommended by the manufacturer of this tool. The use
of attachments or accessories not recommended can
result in serious personal injury.