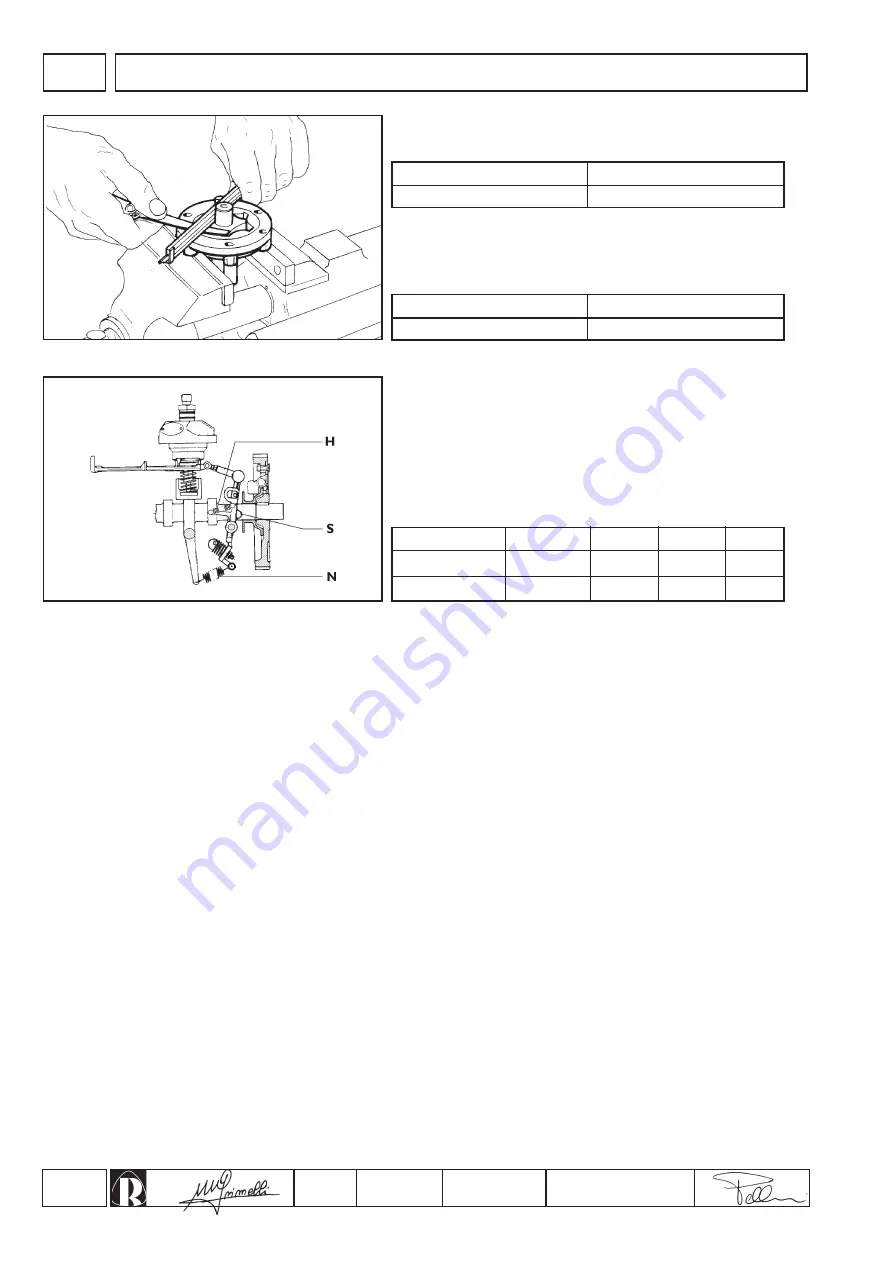
26
COMPILER TECO/ATI
ENDORSED
DATE
14.07.2003
REG. CODE
1-5302-612
MODEL N°
50894
DATE OF ISSUE
07-03
REVISION
00
X
37
38
0,27
÷
0,47
0,60
0,01
÷
0,06
0,10
10
25,5
1,9
0,6
52
÷
54
38,7
32
÷
34
25,75
÷
26,2
Load
kg
Nr of
windings
Lenght under
load mm
Lenght
mm
Governor (N)
Supplement (H)
Spring
Fitting mm
Max. wear mm
Fitting mm
Max. wear mm
CHECKS AND OVERHAUL
The clearance between the external rotor of the oil pump and the
cover facing surface must be:
End float of rotors (fig.37):
Governor lever and spring
Check that the shoes (
S
, fig.38) are level and that the springs have
not lost their elasticity. Renew any excessively worn parts after
consulting the spare parts catalogue.
Supplement and governor spring dimensions (fig.38):