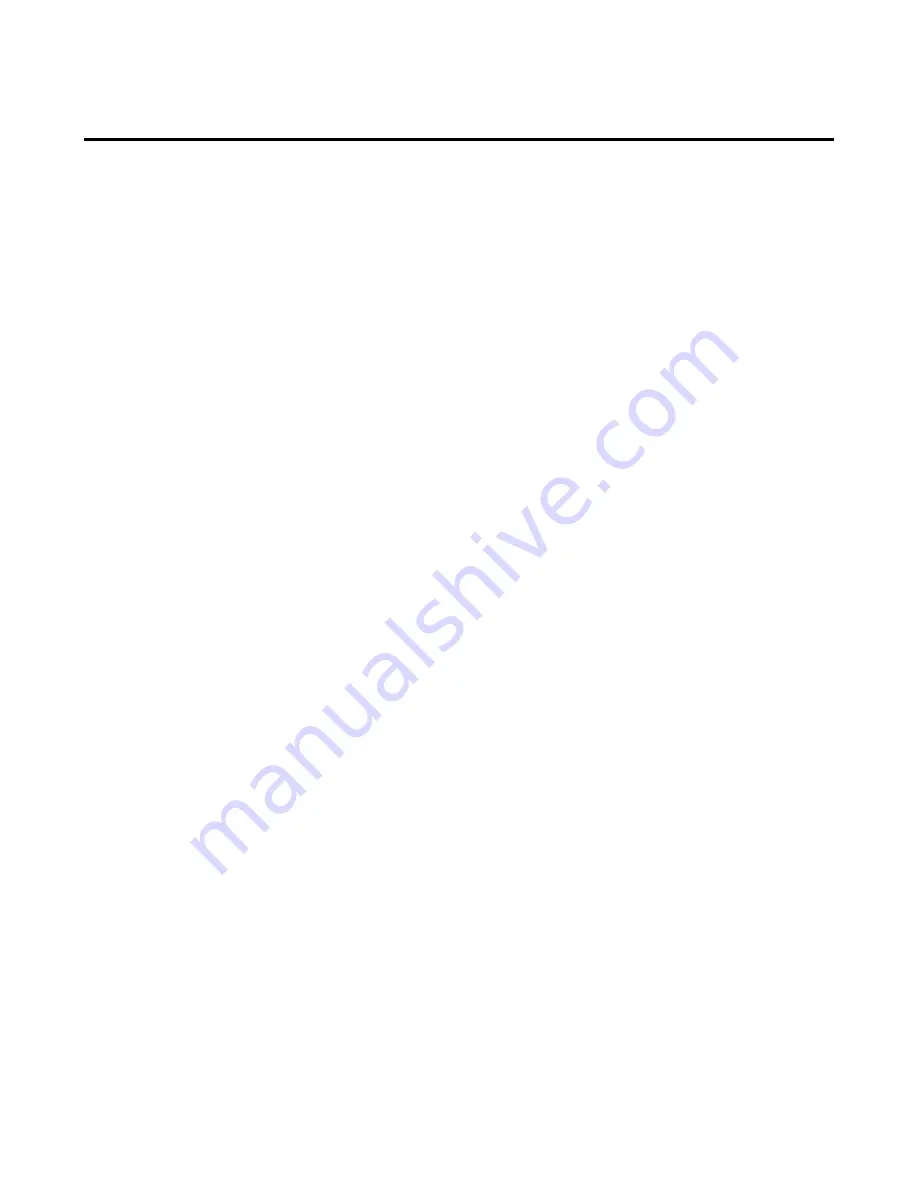
23
Section 4
SERVICE INFORMATION
4.
SERVICE INSTRUCTIONS
4.1.
Routine Maintenance
4.1.1.
Daily Maintenance
Daily maintenance consists of a simple series of functional checks that will alert
maintenance personnel to any signs of developing problems. The importance of
regularly checking the machine cannot be over stressed to prevent not only damage
to the machine, but also loss of productive time and product. Whenever the furnace
is started up the failure alarms should be checked for signs of trouble. An
intermittent exhaust failure indicates that something is wrong and that the alarm
mechanism, system exhaust fan, and possibly exhaust ductwork must be checked
and corrected as necessary. Other alarm functions should be monitored, such as the
lamp failure indicator, to see if corrective action is required. As the machine is
being started up, each control and switch should be briefly checked to insure that
all functions are working properly. Any controls that do not respond as expected,
or alarms that do not clear should be checked out and corrected before putting the
machine into operation.
4.1.2.
Monthly Maintenance
Monthly maintenance, in general, means four weeks of operation for one eight-hour
shift per day. This period of operation is not an absolute number, and it is possible
that some of the tasks are needed more often. Experience with the machine and
process being performed should dictate the need.
4.1.2.1.Run a temperature profile, no less often than monthly, on machines
that are used for sensitive processes, such as thick film firing.
On machines that are used for a variety of products, it is advisable to set
up a profiling schedule so that each process can be checked periodically.
The most sensitive profiles should be checked at least monthly, while
less sensitive profiles could be checked every 2-6 months.
Содержание 2115150301
Страница 23: ...22 Figure 3 8 1 1 Event Logging ...
Страница 44: ...43 Section 6 PRODUCT SPECIFICATION 6 PRODUCT SPECIFICATION ...
Страница 62: ...61 View Product Tracking ...
Страница 83: ...82 ...