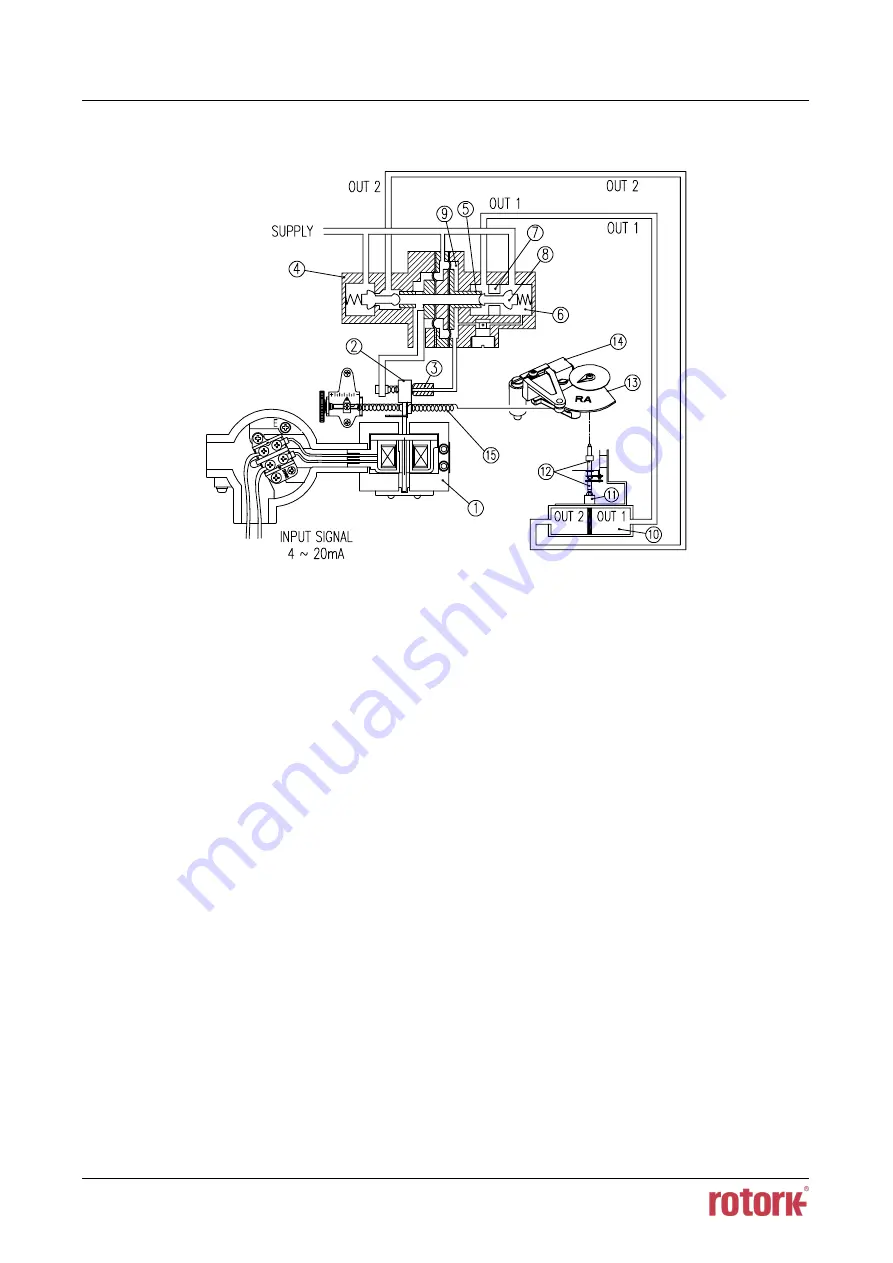
Electro-Pneumatic Positioner
YT-1000 / 1050 series
Product Manual
Ver. 1.30
42
3.2
Rotary Positioner
Fig. 3-2: Rotary positioner with an actuator
When INPUT SIGNAL is supplied to the positioner to open the valve, power is generated from
①
the
torque motor and pushes
②
the flapper to the opposite side of
③
the nozzle. The gap between
③
the
nozzle and
②
the flapper becomes wider and from inner part of
④
the pilot, air inside
⑨
the chamber
is exhausted through
③
nozzle. Due to this effect,
⑤
the spool moves to the right. Then the spool
pushes
⑧
the poppet away from
⑦
the seat which was blocked by the poppet and supplied pressure
(air) goes through
⑦
the seat and OUT1 Port and enters into
⑩
the chamber of the actuator through
OUT1. Then
⑩
chamber’s OUT1 pressure will increase and
⑪
the actuator’s stem will rotate and
through
⑫
the feedback shaft, actuator’s rotating motion will be transferred to
⑬
the cam. This motion
will then rotate
⑭
the span lever and pull
⑮
the span’s spring. Once it reaches to given input signal,
⑮
span spring’s pulling force and
①
torque motor’s power will be balanced and move
②
the flapper
back its original position to reduce the gap with
③
the nozzle. The amount of air being exhausted
through
③
the nozzle will reduce and
⑨
chamber pressure will increase again.
⑤
Spool will move
back to its original position on the left and
⑧
the poppet will also move in same direction blocking
⑦
the seat to stop the air coming into the
⑩
chamber through the SUPPLY. As a result, the actuator
will stop operating and the positioner will return to its normal condition.