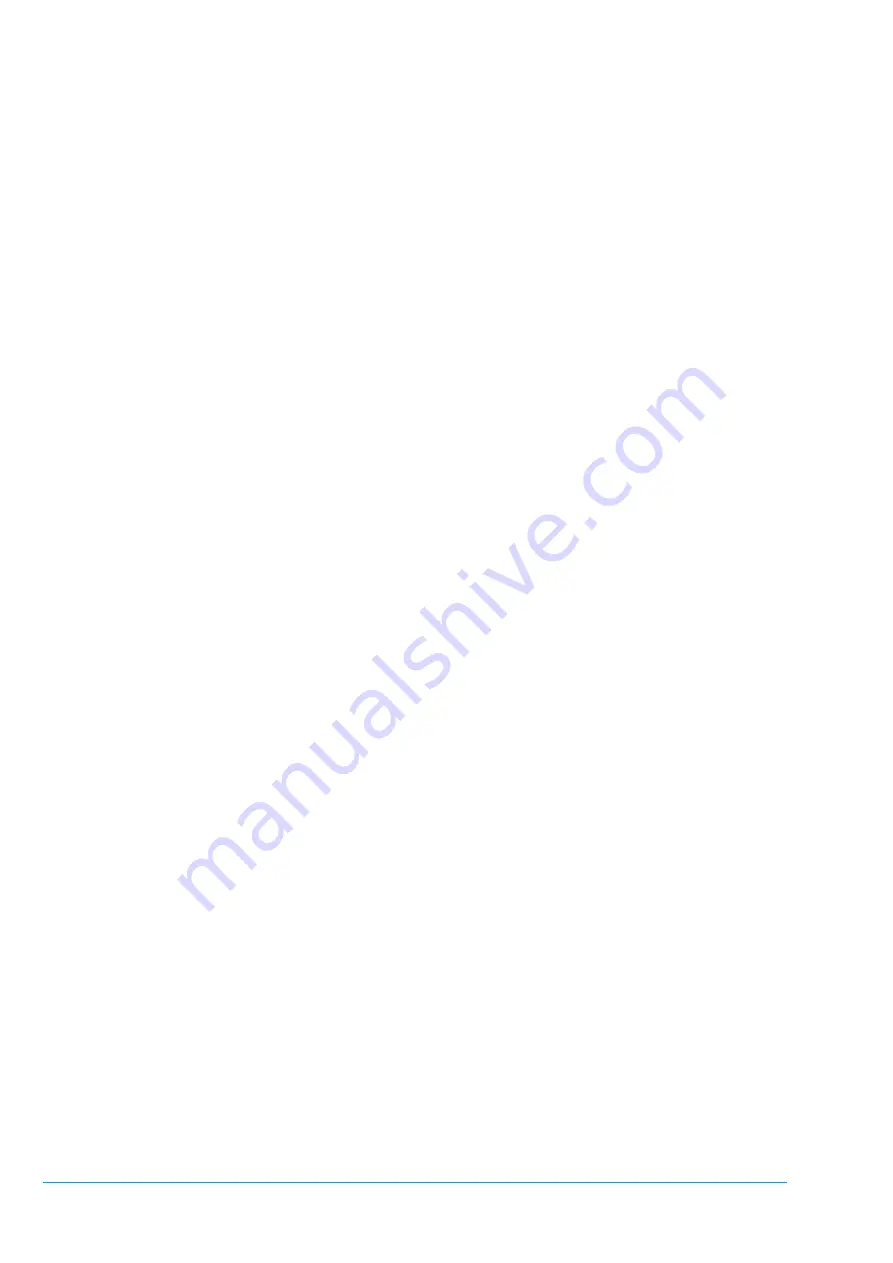
3.8
[en] 02/2014
Installation and operating manual - NK 31
ROTORCOMP VERDICHTER
3.8.2 Load condition
The rotor rotation produces vacuum in the suc-
tion port which opens the untake valve
2
.
The drawn in air flows via the intake filter
1
through the intake valve
2
directly into the com-
pression chamber of the screw compressor
3
.
There the intake air is compressed and oil is
injected for lubrication and cooling.
The oil-air mixture then enters the separator
tank
4
in which the majority of the oil is separated
from the air. The air then flows via the fine sepa
-
rator
5
and the minimum pressure valve
6
to the
compressed air outlet.
In the fine separator
5
the oil is filtered out down
to a residual content of < 3 mg/m
3
and then
routed back into the compressor housing via a
nozzle and a non-return valve
11
.
When the compressor is switched off, the mini
-
mum pressure valve
6
with a non-return function
prevents backflow of the compressed air out of
the system into the compression chamber in the
discharge phase.
During startup a faster pressure buildup is also
ensured, which is required for optimum lubrica
-
tion and oil separation.
The heat resulting during compression is dis-
sipated via the oil-air mixture. The oil circulation
also results from the pressure difference between
the outlet and inlet pressure. The optimum oper-
ating temperature for the oil is adjusted by the oil
thermostat
7
. Depending on the oil temperature,
the oil flow is routed directly via the oil cooler
9
or
directly to the oil filter
8
by the thermostat valve.
The oil then flows via the oil filter
8
to the various
injection points in the compressor block.
3.8.3 Switching off
When the system is switched off pressure builds
up over the rotors and closes the intake valve
2
makeing an oil tight seal.
The remaining pressure is released progressively
via a pressure line from the fine separator
5
to
a nozzle in the intake valve
2
. Through this the
system is completely depressurized.