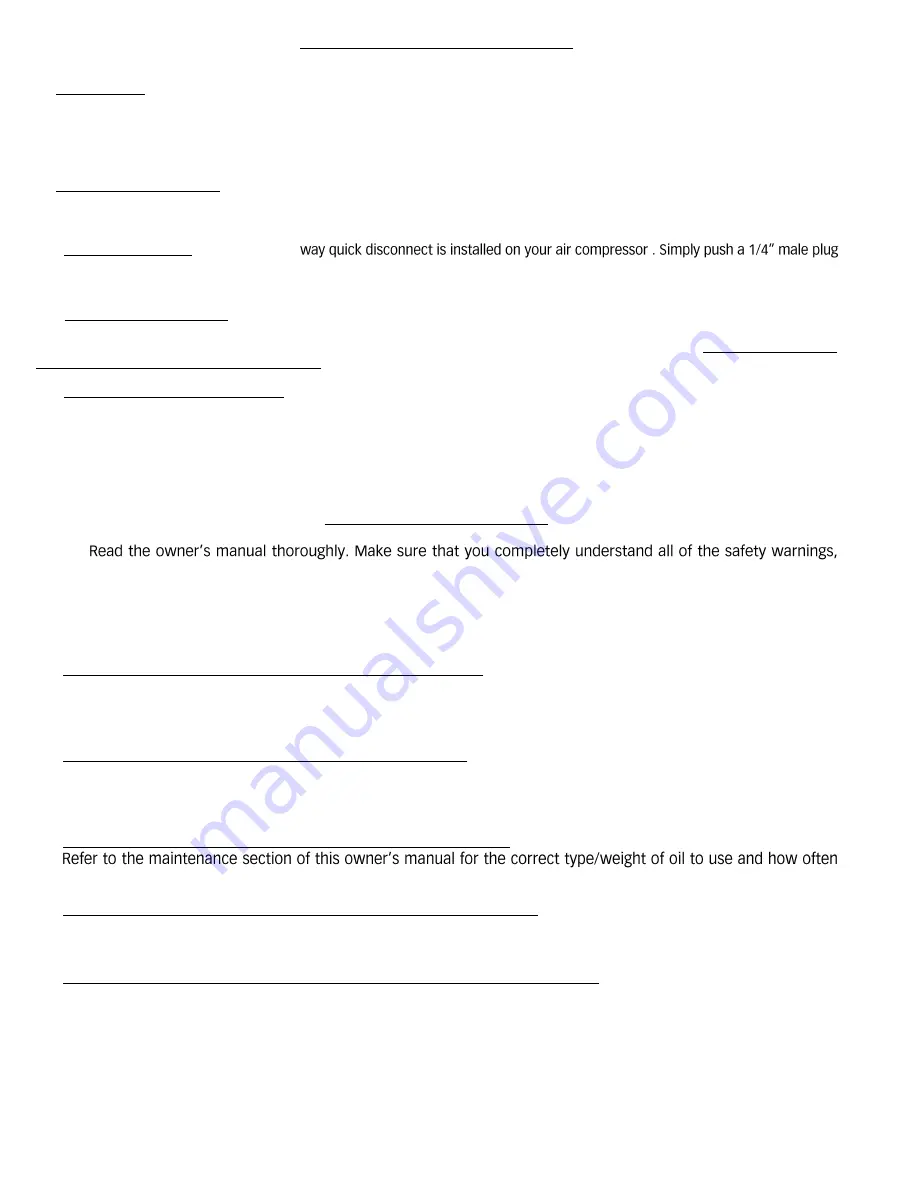
- 6 -
SYSTEM CONTROLS
(continued)
(8) CHECK VALVE Every ROLAIR
air compressor is built with a check valve to seal off and maintain tank pressure after the top end
pressure setting of pilot valve or pressure switch is reached. The check valve works in conjunction with the pressure switch relief
valve to provide a loadless start for the compressor system. A quick burst of air escaping from the pressure switch relief valve
after an electric unit reaches top end indicates the check valve is working properly. If the compressor has a mysterious leak after
stopping that cannot be traced elsewhere, the check valve may require servicing/replacing.
(9) VIBRATION DAMPENER(S)
The rubber pads installed beneath every portable ROLAIR tank assembly are very important to the
proper operation of the air compressor. They provide protection from vibration that left unchecked could cause damage to many
system components.
(10) QUICK DISCONNECT A universal or 3-
into coupler to snap hose fitting into coupler. Always relieve pressure from coupler before installing or removing hose. See
instructions for regulator (#4 above). Pull back on collar to remove air hose after pressure is relieved
(11) BREATHER/OIL FILL PLUG All reciprocating air compressor pumps are built with a crankcase vent to relieve the pressure
that is created by the downward movement of the piston in the pump cylinder. Our direct-drive air compressors vent the
crankcase pressure through special ports in the dipstick. Our belt-drive units vent through the oil-fill plug. Never operate the air
compressor without the dipstick or oil-fill plug.
(12) PRESSURE SWITCH RELIEF VALVE Most electric air compressors set up to operate start/stop are equipped with a pressure
switch relief valve. This valve works in conjunction with the tank check valve to bleed off the compressed air trapped between the
pump and check valve after each cycle, allowing for easier restarts. A brief, audible hiss of air at the end of each cycle signifies the
valve is working properly. A continuous leak at the relief valve at the end of a cycle would indicate a problem with the check valve.
An improperly functioning relief valve/check valve could lead to premature gasket and/or motor failures.
PRE-START CHECKLIST
system controls and instructions provided before attempting to operate this air compressor. Every effort has been
made to provide you with the information needed to obtain many years of reliable and trouble-free service out of
your new air compressor. It is your responsibility to operate the air compressor properly. To obtain the longest
possible service life from your air compressor you must always keep the following instructions in mind.
1.
ALWAYS OPERATE THE COMPRESSOR IN A LEVEL POSITION
All splash-lubricated pumps have a dipper on the bottom of the connecting rod that must remain submerged in
the oil bath. Operation at more than a 10 degree angle will cause the pump to seize and void the product
warranty
2.
OPERATE IN A CLEAN, DRY AND WELL VENTILATED AREA
Do not operate in the rain or in areas of standing water. Never operate in an area where other gases, fumes or
vapors are present which may become explosive when compressed. Do not operate compressor in an enclosed
area.
3.
CHECK OIL LEVEL DAILY AND CHANGE AT REGULAR INTERVALS
the oil should be changed. Check oil levels daily.
4.
INSPECT/CLEAN/CHANGE INTAKE ELEMENTS ON A REGULAR BASIS
The ingestion of dirt into the pump and engine is the primary cause of premature wear. Pay special attention to
the intake filters. Check intake filters daily.
5.
USE LONGER, PROPERLY SIZED AIR HOSE RATHER THAN EXTENSION CORDS
If an extension cord must be used, please refer to the chart below for the proper gauge and maximum length that
can be used. The use of inadequately sized air hose will also lead to frictional pressure drops that could affect the
proper performance of your air tools.