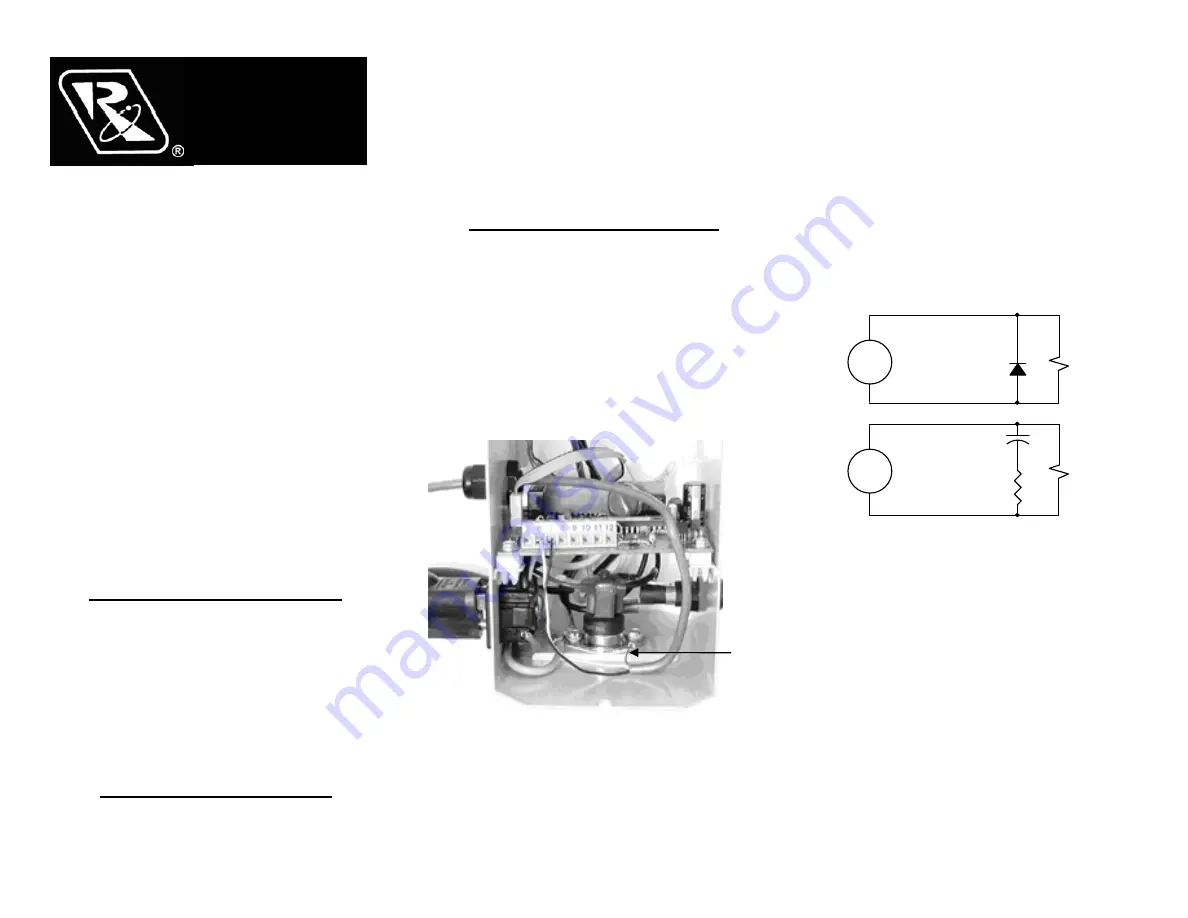
RODIX SOLUTION
Good wiring practices for
avoiding electrical noise
problems.
Rodix controls have been designed with a
high degree of immunity to electrical
noise; however, depending on the control
installation, electrical noise can cause
problems. These problems occur in less
than 1% of the product installations. Most
electrical noise problems can be avoided
by following some simple guidelines.
Good wiring practices need to be used to
prevent electrical noise from interfering
with your control’s operation. Another
name for electrical noise is Electro-
Magnetic Interference (EMI).
Symptoms of Electrical Noise
The symptoms of electrical noise would
appear as follows: a brief pause or a brief
“bump” in the vibratory feeder’s output
that the control automatically recovers
from. In rare cases the control will either
stop operating or run continuously at full
power in 120 pulse mode until the power
switch is slowly cycled OFF and ON.
Sources of Electrical Noise
Electrical noise is generated by devices
like relay coils, solenoid valves,
contactors, servo motors, and variable
frequency inverter drives. The electrical
noise is then transferred to another device
by one of three ways. The noise could be
conducted through the power wires, or
capacitively coupled from wire to adjacent
wire, or it is transmitted from the wires of
a nearby noise source.
Solutions for Electrical Noise
1. Use shielded wires for all I/O (Input /
Output) signals. The I/O signals may
include: 4-20mA input, Run input, Sensor
input, 0-5VDC input, Interlock input or
AUX output. The shield “drain” wire
should be tied to the chassis in the Rodix
control. The drain wire should be kept
shorter than 2”. Please see the enclosed
picture.
Example of a “drain” wire termination
2. Never run I/O signal wires in the same
conduit or raceway as AC power lines
such as wires to motors, solenoids,
heaters, welders and Rodix controls, etc.
3. I/O wires within an enclosure should
be routed as far away as possible from
relays, solenoids, transformers, power
wiring and other noisy equipment. Keep
the I/O signal wires separate from the
control’s input and output power wiring.
Secure the wires in place.
4. Whenever relays or solenoid valves
are used, install a Snubber on them to
reduce electrical noise. Use a diode on a
DC coil. Use a RC Snubber on an AC
coil.
5. In extremely high EMI environments,
Power Line Filters and ferrite beads can
be effective. Install ferrite beads on I/O
signal wires as close as possible to the
circuit board terminal strip. Loop the wire
through the bead several times or use
several beads on each wire for additional
protection.
RODIX, INC.
Toll Free (800) 562-1868
E-mail [email protected]
www.rodix.com
2000,2014 RODIX INC. Good Wiring 1/31/2014
RODIX INC.
FEEDER CUBE
RODIX SOLUTION .408
Drain
Wire
RELAY
COIL
SNUBBER
VAC
104M06QC47
QUENCH-ARC
RECTIFIER
DIODE
RELAY
COIL
1N4006
VDC
+
-