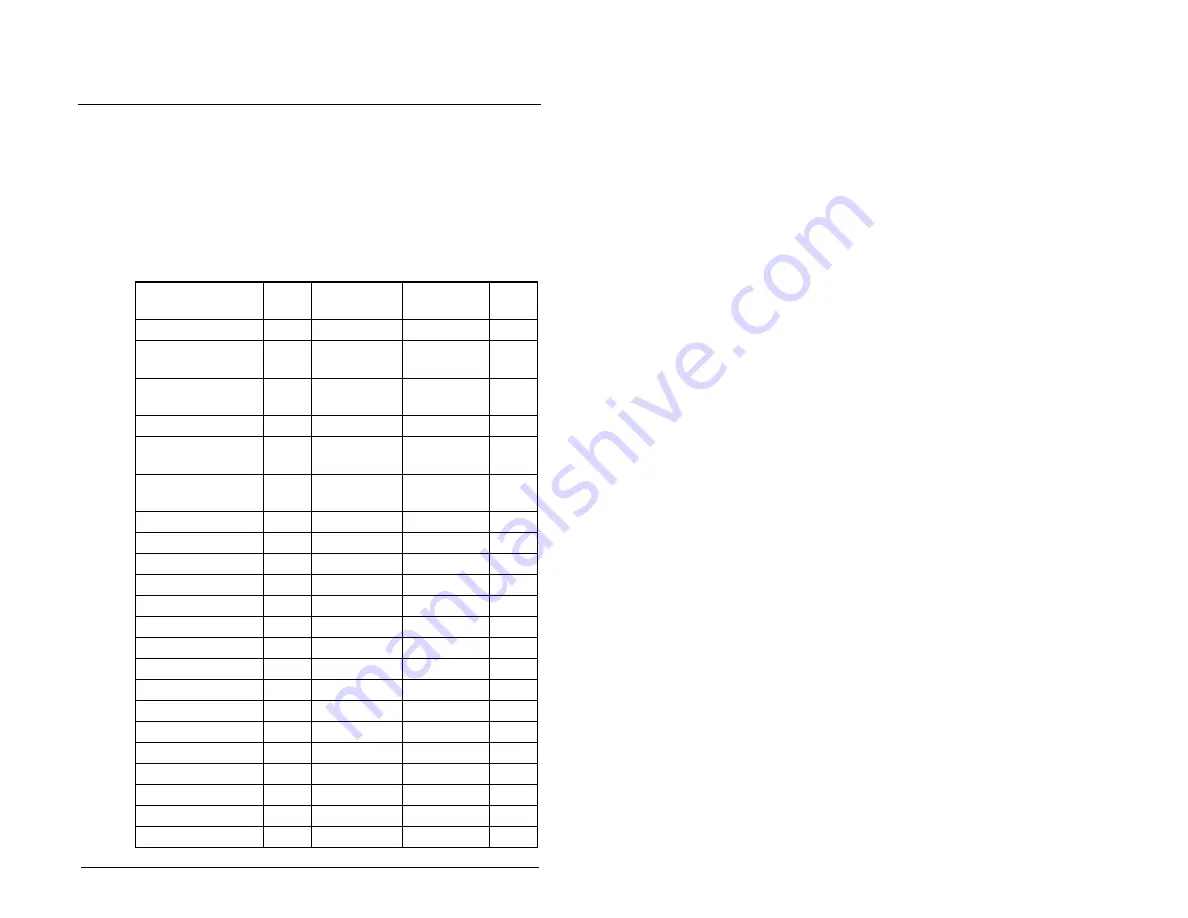
Parameters Cross-Referenced by Name
C-1
A
PPENDIX
C
Parameters
Cross-Referenced
by Name
Parameter Name
No.
Parameter
Group
Default
Value
Page
No.
0 - 10 V Analog Input
d020
Display
Read Only
9-32
0 - 10 V Analog Input
High
A111
Advanced
100.0%
9-24
0 - 10 V Analog Input
Low
A110
Advanced
0.0%
9-24
4 - 20 mA Analog Input
d021
Display
Read Only
9-32
4 - 20 mA Analog Input
High
A113
Advanced
100.0%
9-25
4 - 20 mA Analog Input
Low
A112
Advanced
0.0%
9-25
Accel Time 1
P039
Basic
5.0 sec
9-7
Accel Time 2
A067
Advanced
10.0 sec
9-11
Auto Restart Delay
A093
Advanced
1.0 sec
9-19
Auto Restart Tries
A092
Advanced
0
9-18
Comm Data Rate
A103
Advanced
4 = 19.2 K
9-22
Comm Format
A107
Advanced
0 = RTU 8-N-1
9-23
Comm Loss Action
A105
Advanced
0 = Fault
9-22
Comm Loss Time
A106
Advanced
5.0
9-23
Comm Node Address
A104
Advanced
1
9-22
Comm Status
d015
Display
Read Only
9-31
Commanded Frequency
d002
Display
Read Only
9-27
Compensation
A097
Advanced
1 = Electrical
9-20
Control Input Status
d013
Display
Read Only
9-30
Control Source
d012
Display
Read Only
9-29
Control SW Version
d016
Display
Read Only
9-31
Current Limit
A089
Advanced
Amps x 1.8
9-17
Содержание MD60
Страница 1: ...Instruction Manual MD60 AC Drive User Manual Version 3 0 D2 3499 3 ...
Страница 6: ...IV MD60 AC Drive User Manual ...
Страница 8: ...VI MD60 AC Drive User Manual ...
Страница 10: ...VIII MD60 AC Drive User Manual ...
Страница 12: ...1 2 MD60 AC Drive User Manual ...
Страница 42: ...6 10 MD60 AC Drive User Manual ...
Страница 92: ...10 10 MD60 AC Drive User Manual ...
Страница 96: ...A 4 MD60 AC Drive User Manual ...
Страница 100: ...B 4 MD60 AC Drive User Manual ...
Страница 104: ...C 4 MD60 AC Drive User Manual ...
Страница 108: ...D 4 MD60 AC Drive User Manual ...
Страница 134: ......
Страница 135: ......
Страница 136: ...Publication D2 3499 3 September 2003 2003 Rockwell International Corporation All rights reserved ...