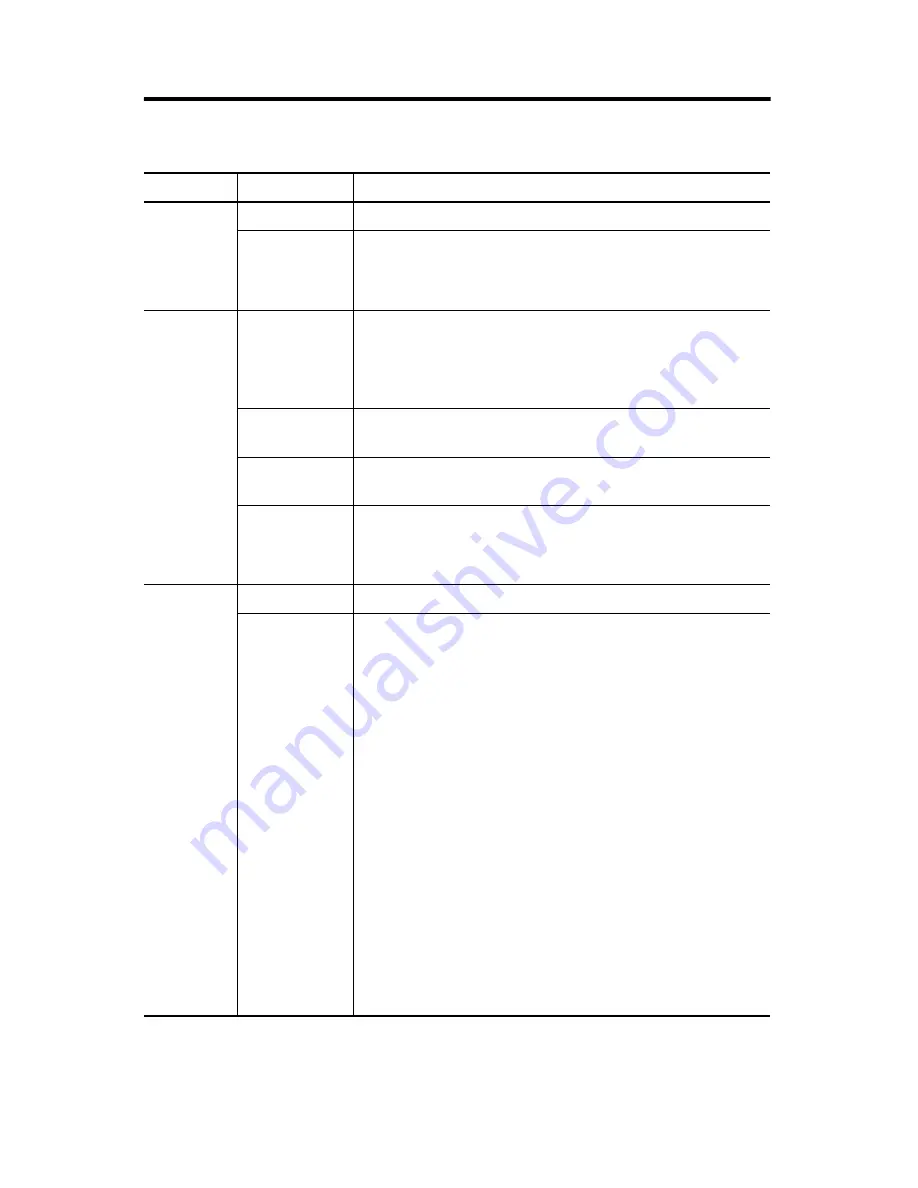
38
CompactLogix Packaged Controllers
Publication 1769-IN082A-EN-P - July 2008
BATT
Off
The battery supports memory.
Steady red
The battery is either:
•
not installed.
•
95% discharged and should be replaced.
I/O
Off
Either:
•
There are no devices in the I/O configuration of the packaged
controller.
•
The packaged controller does not contain a project.
Steady green
The packaged controller is communicating with all the devices in its I/O
configuration.
Flashing green
One or more devices in the I/O configuration of the packaged controller
are not responding.
Flashing red
Either:
•
The packaged controller is not communicating with any devices.
•
The packaged controller is faulted.
OK
Off
No power is applied.
Flashing red
One of the following conditions exists:
•
The packaged controller requires a firmware update.
•
A major recoverable fault occurred on the packaged controller.
To clear the fault, perform this procedure.
•
Turn the packaged controller keyswitch from PROG to RUN to
PROG.
•
Go online with RSLogix 5000 software.
•
A nonrecoverable major fault occurred on the packaged
controller. In this case, the packaged controller:
a. OK indicator initially displays steady red.
b. Resets, clearing the project from memory.
c. Sets the OK indicator to flashing red.
d. Produces a major recoverable fault.
e. Generates a fault code in the RSLogix 5000 project.
The fault code displayed in RSLogix 5000 software and the subsequent
fault recovery method depends upon your system.
Controller Status Indicators
Indicator
Status
Description