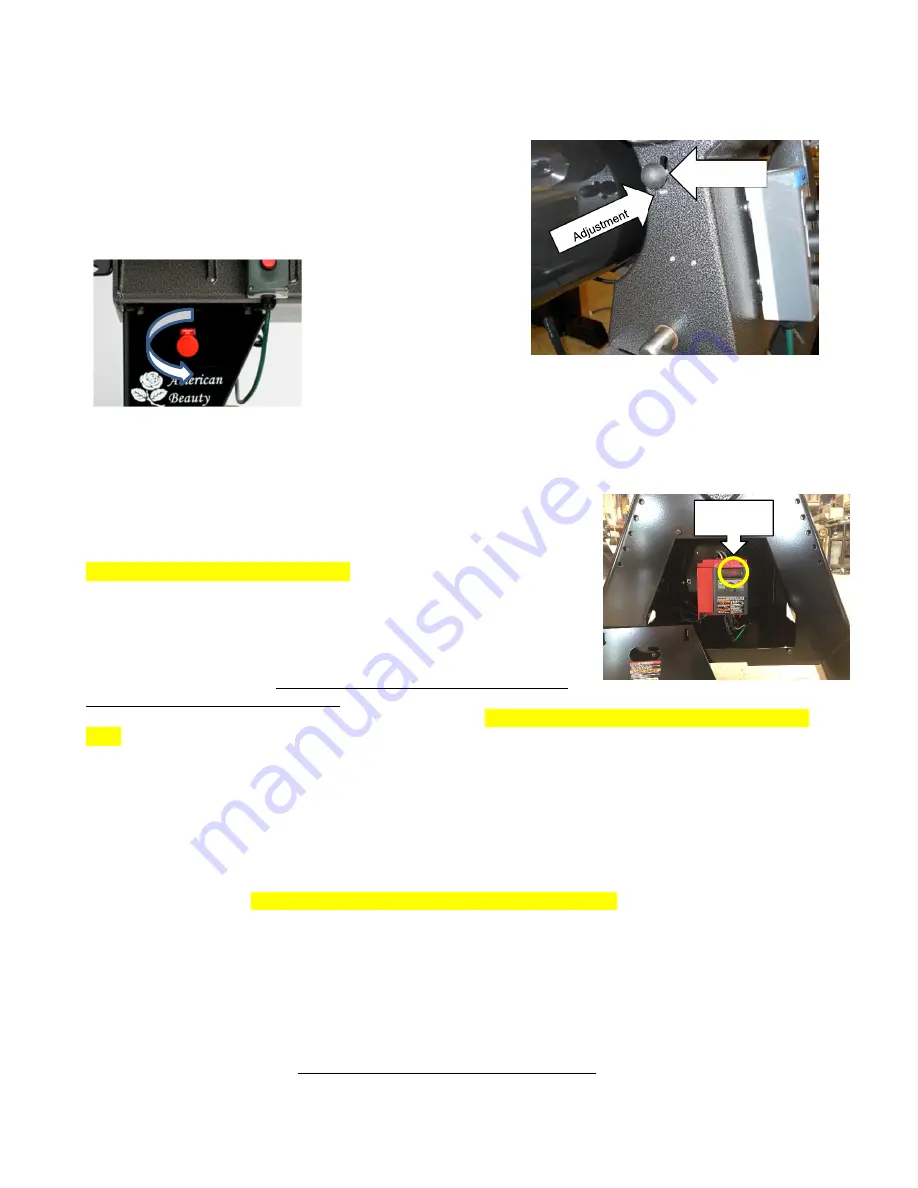
15
TROUBLE SHOOTING
Failure to Start, try these six steps in order:
1) Push down on the spindle lock: it may have moved upward just
enough to open the internal safety switch but not enough to lock the
spindle. If the problem happens frequently, try tightening up the
adjustment screw that puts tension on the spindle lock. You’ll find it
in the threaded hole directly below the spindle lock knob.
2) Check the emergency off
switch. If you’ve bumped it,
you’ll need to give it a little twist
to re‐establish power.
3) Check that the lathe is plugged
in to a working outlet of the correct voltage.
4) Check that the circuit breaker has not tripped.
5) Look for dust or debris that might interfere with movement of the switches on the pendant controller. Disconnect the
power, open the controller and clean the switches with compressed air. Check that all wire connections are tight.
6) Remove the cover plate over the inverter and check the inverter for error
codes. A blank screen means there is no power to the inverter, so check out 2‐4
above. If there is power, the display should read “0.0.”
ANYTHING ELSE WILL BE AN ERROR CODE. If the error code is “ПOFF” you do not
have correct power to the unit. You’ll typically only see this the first time you
start the lathe from new. This error code indicates there is only 110v going to the
machine, not 220. Time to call an electrician.
If any other error code is present, clear it by unplugging the machine until the
display goes completely blank (
a quick power down will not be sufficient – the
lathe must be unplugged for 2‐3 minutes
). After the code has cleared, plug the lathe back in and let it reboot. If you are
consistently getting error codes, call Robust with the error code. If it still will not run,
DO NOT
attempt to program the
drive.
INTERMITTENT STOPPING
: If your lathe shuts down for no apparent reason while you are making cuts or turning out of
balance work, but you can start it right back up, see #1 above.
LOSS OF POWER‐Lathe bogging down:
Make sure are using the large pulley on the spindle for heavy cuts and coring.
Coring takes a lot of horsepower. The cutter blade rubbing or loading up with shavings acts like a disc brake. Go slow and
sharpen often. If the belt is slipping, thumb pressure on the motor or motor mount is normally more than enough to
ensure power transmission. Also look for dirt or oil on the belt by loosening it, turning it inside out and cleaning it and the
pulleys using a fine brush. Do not apply belt dressing as belt dressing just collects dust. Remember: horsepower is not a
substitute for sharp tools and good technique. Overloading the machine will result in an error code of “OP3” on your
inverter. Reset is described above. Remember: horsepower is not a substitute for sharp tools and good technique.
SPINDLE LOCK IS HARD TO MOVE
: Squirt a little light oil into the slot and work it up and down. You can also loosen the
screw that puts tension on the spindle lock, see #1 above. Too much tension and you won’t be able to move the spindle
lock, too little and you may get some intermittent stopping (see above).
PROBLEM WITH CENTER ALIGNMENT:
For optimum alignment push the headstock and tailstock away from you, against
the back way. Also look for debris stuck to the bottom of the headstock or tailstock. A very small amount can make a big
difference. If cleaning does not re‐establish alignment, settle the lathe as described elsewhere. If you have bolted your
lathe down, it is especially important to settle the lathe afterwards. Clean your Morse Tapers and check for burrs.
Spindle Lock
Should
read “0.0.”