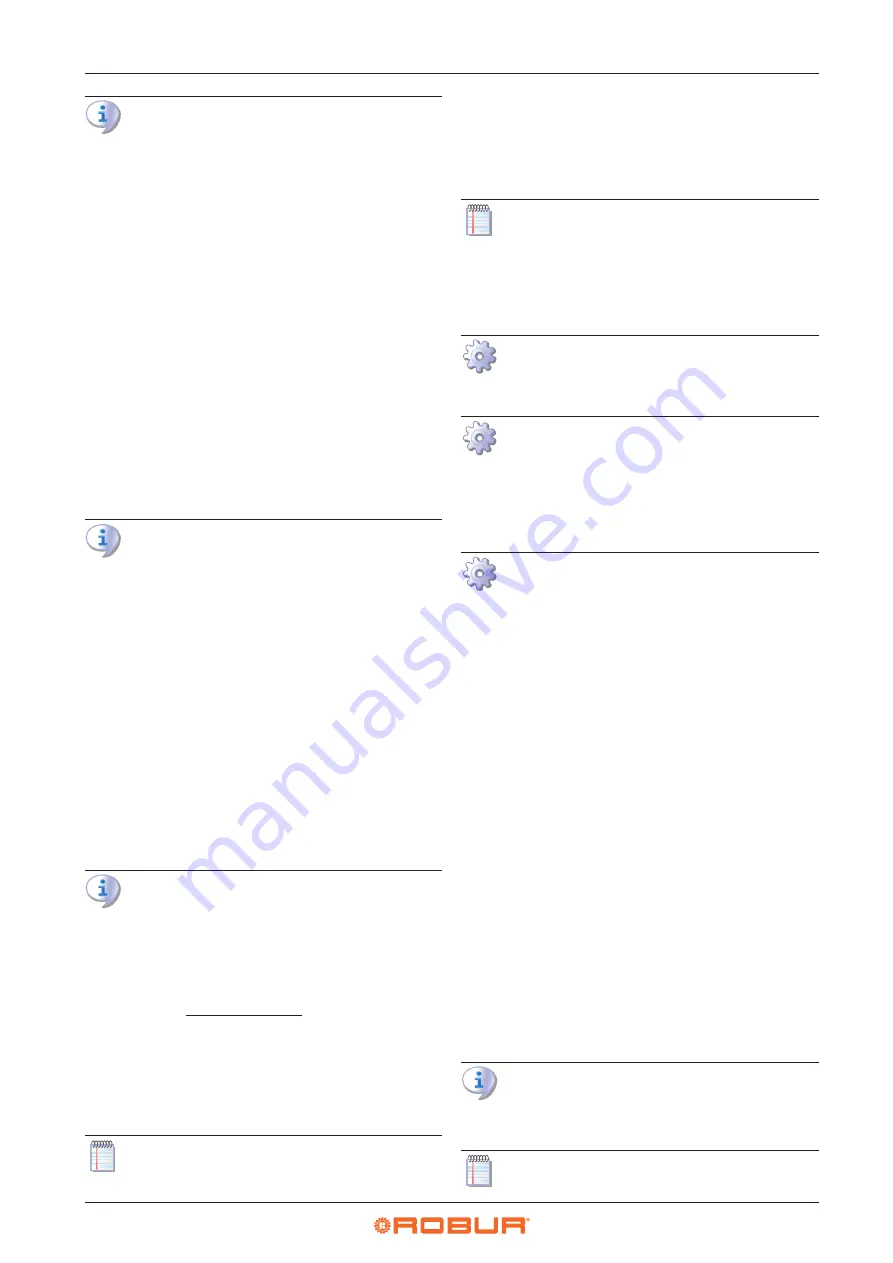
Heating engineer
18
3
Installation must also comply with the manufactur-
er's provisions.
3.2
HYDRAULIC CONNECTIONS
The hydraulic installer must make the hydraulic connec-
tion circuit to the heating system.
The installer must provide for the construction of a suita-
bly sized hydraulic connection circuit, taking into account:
A. of the following indications:
Use pipes for heating/cooling systems, protected
from weathering and freezing, insulated for ther-
mal dispersion.
Sizing of the pipes, according to the standard circu-
lator, must grant the nominal water flow required
for the correct operation of the heating system.
When using glycol water, take this into account
when selecting the pipe material and calculating
the additional pressure drop generated by the
presence of glycol (Table 3.1
B. of the residual head and pressure drop data reported
in Paragraph 1.6.3
Connect the outlet of the boiler safety valve
(Paragraph 1.2
p. 7) to a suitable drain. The
manufacturer is not liable for any damage caused
by the opening of the safety valve in the event of
system overpressure.
3.2.1
Hydraulic connections
on the right, at the bottom, connection plate (Paragraph
1.2
3.2.1.1
AY 35 and AY 50
OUT
Water outlet connection Ø 1 1/4" F
IN
Water inlet connection Ø 1 1/4" F
3.2.1.2
AY 100
OUT
Water outlet connection Ø 1 1/2" F
IN
Water inlet connection Ø 1 1/2" F
3.2.2
Pipe cleaning
Pipe cleaning
Before connecting the appliance,accurately wash
the water and gas piping and any other system
component, removing any residue.
3.2.3
Minimum components of water circuit
Always provide, near the appliance:
▶
on water piping, both outlet and inlet
2 antivibration joints on water fittings
2 pressure gauges
2 isolation ball valves
▶
on the inlet water piping
1 separator filter
The appliance is equipped with its own 10 l internal
expansion tank and with a safety valve. Depending
on the water content of the system, assess the
need for additional expansion tanks.
3.2.4
System filling
For the calculation of the total water content to
be loaded in the system it is necessary to add the
water content of the boiler (Table 1.1
of the distribution terminals to the water content
in the pipes and in other elements that make up
the system (tanks, hydraulic separators, etc.).
Proceed with the filling of the system as follows.
A filling tap on the system must be provided for fill-
ing the system.
At the first power supply and each time the power
supply is restored, an automatic system venting
cycle is activated. The display will show the code
F33 for the entire duration of the cycle (5 minutes
for the first power supply, 2 minutes for the fol-
lowing ones).
To access the display, remove the front panel of the
boiler, as shown in Figure 5.1
3.2.4.1
AY 35
1. Slightly loosen the cap of the jolly valve placed on the
top of the condensing block (Figure 3.1
p. 19) to re-
lease the air from the top of the boiler.
2. Open the system filling valve (to be provided on the
system) and let out all the air.
3. Check with pressure gauge that system pressure
reaches 1,5 bar.
4. Open the automatic air vent valves on the system, if
any, and check the air venting process.
5. Make sure that the unit is energized.
6. Send an operating request to the unit for a few sec-
onds. The circulating pump will be immediately
activated.
7. Remove the request before the burner is activated.
The circulating pump will continue to circulate the wa-
ter for the post-circulation time.
8. If, after the above operations, a decrease in system wa-
ter pressure is observed, open again the system filling
tap until the system pressure reaches 1,5 bar.
9. Repeat items 6, 7, 8 until the pressure has stabilised (at
least 1,5 bar).
10. After the operation, make sure that the system filling
tap is tightly closed.
Once the filling operation has been completed,
close the cap of the jolly valve on the condensing
block, to avoid water leaks.
To start the circulation pump only, with the boiler