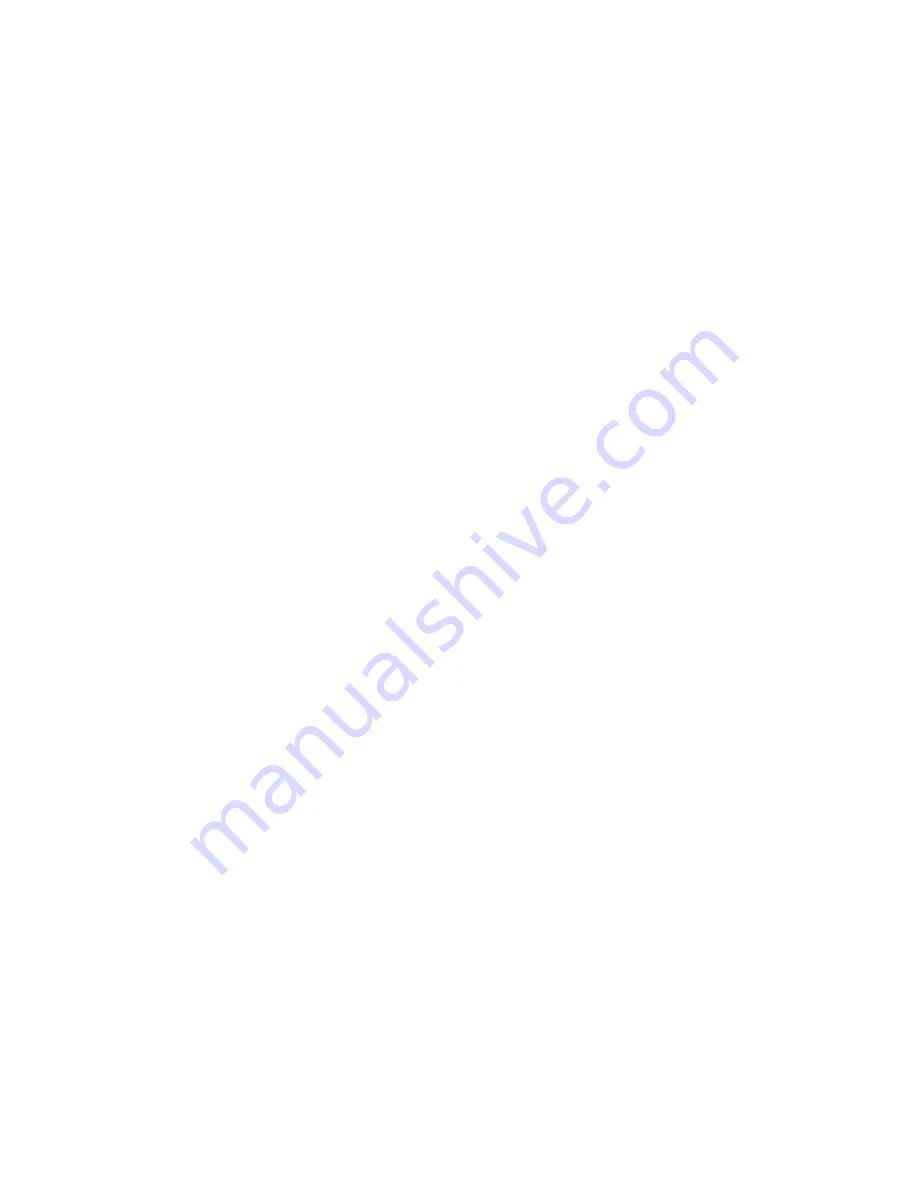
- 4 -
type solder removal device or with solder braid.
CAUTION:Work quickly to aviod overheating the
circuiboard printed foill.
6.Use the following soldering technique.
a.Allow the soldering iron tip to reach a normal temperature
(500k to 600k)
b.First,hold the soldering iron tip and solder the strand.
Against the component lead the solder melts.
C.Quickly move the soldering iron tip to the junction of the
compontent lead and the printed circuit foil and hold it
there oniy until the solder flows onto and around both
the component lead and the foil.
CAUTION:work quickly to avoid overheating the circuit
board printed foil.
d.Closely inspect the solder area and remove any excess
or splashed solder with a small wire-bristle brush.
IC Remove/Replacement
Some chassis circuit boards have slotted holes (oblong)
through wheic the IC leads are inserted’and then bent ftat
against the circuit foil. When holes are the slotted type the
following technique should be used to remove and replace
the IC. When working with boards using the familiar round
hole use the standard technique as outlined in parapraphs
5 and 6 above.
Removal
1. Desolder and straighten each IC lead in one operation
by gently prying up on the tead with soldering iron tip as
the solder melts.
2.Draw away the melted solder with an anti-static suction-
type solder removal device (or with solder braid) before
removing the IC.
Replacement
1.Carefully insert the replacement IC in the circuit board
2.Carefully bend each IC lead against the circuit foil pad
and solder it.
3.Clean the soldered areas with a small wire-bristle brudh.
(It is not necessary to reapply acrylic coating to the areas).
“Small-Signal” Discrete Transistor
Removal/Replacement
1.Remove the defective transistor by clipping its leads as
close as possible to the component body.
2.Bend into a “u” shape the end of each of three leads
renaining on the circuit board.
3.Bend into a “u” shape the replacement transistor leads.
4.Connect the replacement transistor leads to the corre
sponding leads extending from the circuit board and crimp
the “u”with long nose pliers to insure metal to metal to
metal contacttehn solder each connection.
Power Output, Transistor Device
Removal/Replacement
1.Heat and remove al solder from around the transistor
leads.
2.Remove the heatsink mounting screw (if so equipped).
3.Carefully remove the transistor from the heat sink of the
circuit board.
4.Insert new transistor in the circuit board.
5.Solder each transistor lead and clip off excess lead.
6.Replace heatsink.
Diode Removal/Replacement
1.remove defective diode by clipping its leads as close as
possible to diode body.
2.Bend the two remaining leads perpendiculay to the cir
cuit board.
3.Observing diode polarity wrap each lead of the new
diodearound the corresponding lead on the circuit board.
4.Secruely crimp each connection and solder it.
5.Inspect (on the circuit board copper side)the solder joints
of the two “original” leads. If they are not shiny reheat
them and if necessary apply additional solder.
Fuse and Conventional Resistor
Removal/Replacement
1.Clip each fuse or resistor lead at top of the circuit board
hollow stake.
2.Securely crimp the leads of replacement component
around notch at stak top.
3.Solder the commections.
CAUTION:Maintain original spacing between the replaced
component and adjacent component and the circuit board
to prevent excessive component temperaures.
Circuit Board Foil REPAIR
Excessive heat applied to the copper foil of any printed
circuit board will weaken the adhesive that bonds the foil
to the circuit board causing the foil to separte fron or “lift-
off” the board. The following guidelines and procedures
should be followed whenever this condition is encountered.
At IC Connections
To repair a defective copper pattem at IC connections use
the following procedure to install a jumper wire on the cop-
per pattem side lf the circuit board.9 (use this technique
ony on IC connections)
1.Carefully remove the damaged copper pattem with a
sharp knife.(Remove only as much copper as absolutely
necessary).
2.Carefully scratch away the solder resist and acrylic
coating(if used) from the end of the remaining copper
patten.
3. Bend a small “U” in one end of a small gauge jumper
wire and carefully crimp it around the IC pin.Solder the
IC connection.
4.Route the jumper wire along the path of the out-away
copper patten and let it overlap the previously scraped
end of the good copper pattem.Solder the overlapped
area and dip off any excess jumper wire.
At Other Connections
Use the following technique to repir the defective copper
pattem at connections other than IC pins.This technique
involoves the installation of a jumper wire on the compo-
nent side of the circuit board.
1.Remove the defective copper pattem with a sharp knife.
Remove at least 1/4 inch of copper,to ensure that a haz
ardous condition will not exist if the jumper wire opens.
2.Trace along the copper pattem from both sides of the
pattem break and locate the nearest component that is
directly connected to the affected copper pattem.
3. Connect insulated 20-gauge jumper wire from the lead
of nearest the nearest component on one side of the
pattem break to the lead of the nearest component.on
the other side,Carefully crimp and solder the connections.
CAUTION:
Be sure the insulated jumper wire is dressed
so the it does ot touch componets or sharp edges.
SERVICING PRECAUTIONS