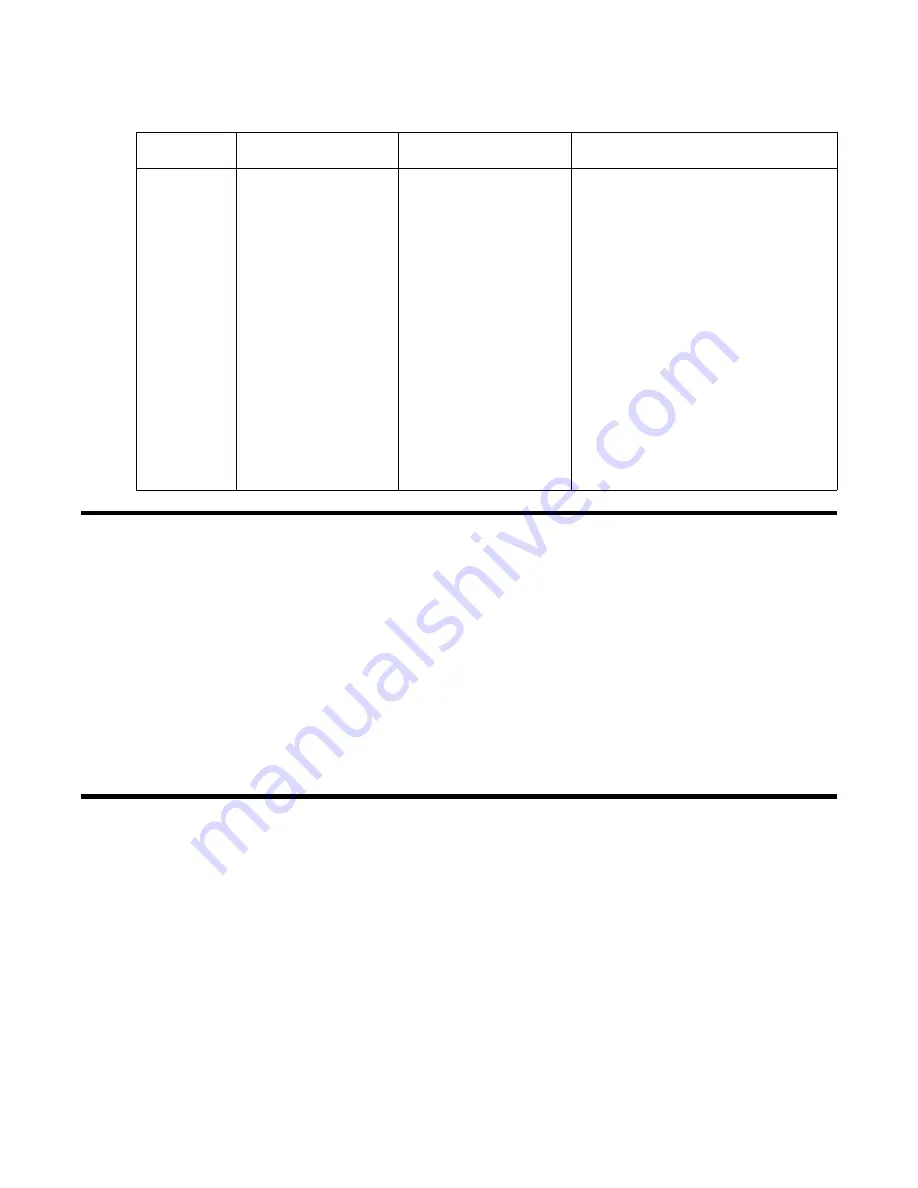
65-2640RKSS-04S M2A Transmitter Operator’s Manual
35
Calibration Frequency
Although there is no particular calibration frequency that is correct for all applications, a calibration frequency of
every 3 to 6 months is adequate for most combustible gas transmitter applications. Unless experience in a
particular application dictates otherwise, RKI Instruments, Inc. recommends a calibration frequency of every 3
months.
If an application is not very demanding, for example detection in a clean, temperature controlled environment
where combustible gas is not normally present and calibration adjustments are minimal at calibration, then a
calibration frequency of every 6 months is adequate.
If an application is very demanding, for example if combustible gas is present often and in significant
concentrations or the environment is not well controlled, then more frequent calibration than every 3 months may
be necessary. If potential catalyst poisons are known or likely to be present, more frequent calibration than every
3 months will be necessary.
Determining Response Time
Since the detector junction box is installed remotely from the M2A, the response time of the detector will depend
on the length of flexible tubing that is attached to the calibration adapter/splash guard. To determine the response
time based on the length of tubing connected:
1. Place the M2A into its calibration mode or disable external alarms.
2. Note the current gas reading displayed at the M2A.
3. Screw the regulator into the calibration cylinder. Do not use a zero air cylinder for this operation.
4. Use the flexible tubing coming from the calibration adapter/splash guard to connect the regulator to the
calibration adapter/splash guard.
5. Turn the regulator’s on/off knob counterclockwise to open the regulator. Gas will begin to flow. Take note of
the time or start a stopwatch.
Slow or No
Response/
Difficult or
Unable to
Calibrate
• Unable to
successfully set the
fresh air or span
reading during
calibration.
• M2A requires
frequent calibration.
Note:
See
for calibration
frequency guidelines.
• The calibration
cylinder is low, out-
dated, or defective.
• The calibration gas
flow rate is too low.
• The calibration gas is
not an appropriate
concentration.
• The detector is
malfunctioning.
• The terminal PCB is
malfunctioning.
• The flexible tubing to
the calibration
adapter/splash guard
has become kinked,
blocked, or
disconnected.
1. Verify that the calibration cylinder
contains an adequate supply of a
fresh test sample.
2. Verify that the regulator used for
calibration is a 0.5 LPM regulator.
3. Verify that the calibration gas
concentration is appropriate for the
transmitter. The concentration should
be in the detection range, preferably
about half of the detection range.
4. Verify that the flexible tubing to the
calibration adapter/splash guard is
clear and connected to the calibration
adapter/splash guard.
5. If the calibration/response difficulties
continue, replace the detector.
6. If the calibration/response difficulties
continue, contact RKI for further
instruction.
Table 7: Troubleshooting the Combustible Gas Detector (Continued)
Condition
Symptom(s)
Probable Causes
Recommended Action