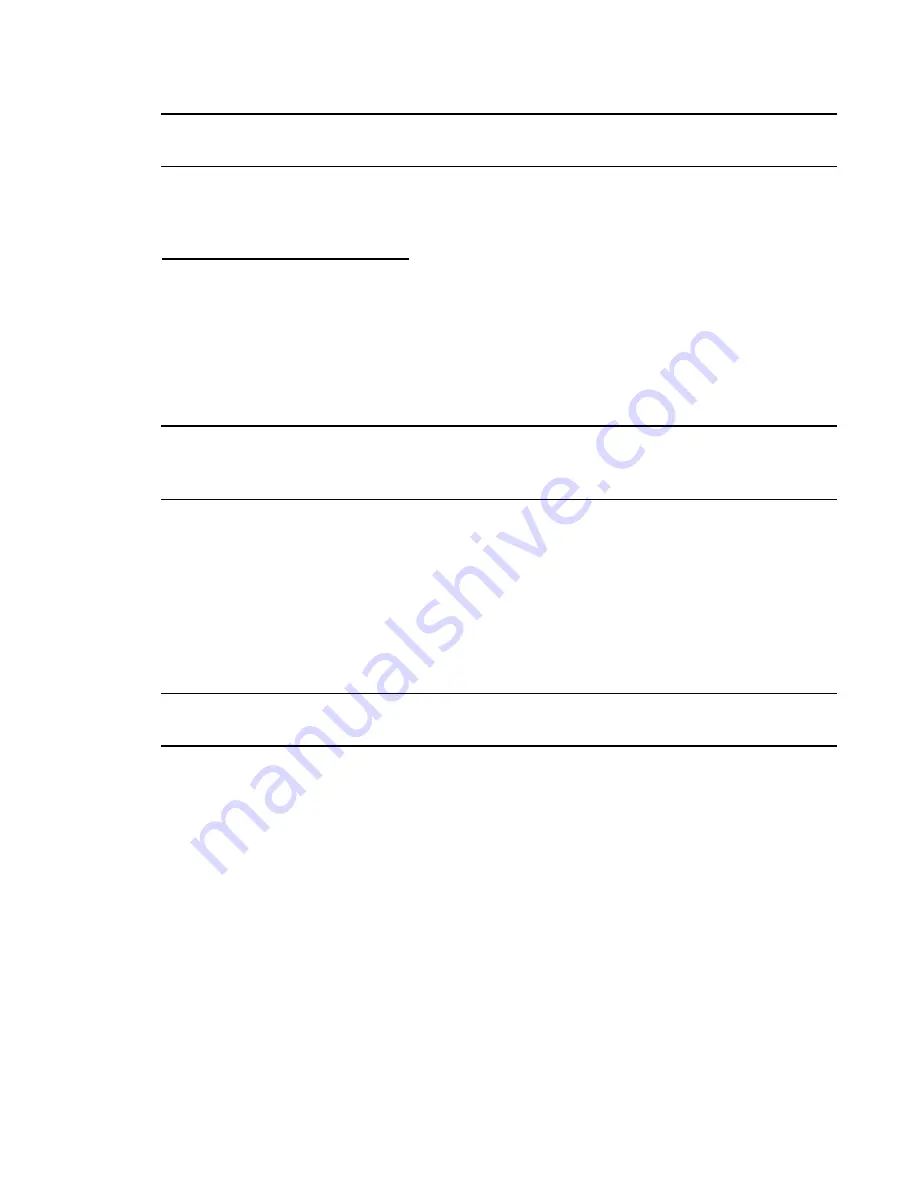
35-3001A-01-XX1 Sample-Draw Detector Operator’s Manual • 15
CAUTION:
Avoid loops or slumps in the incoming sample line. To reduce response time,
keep the incoming sample line as short as possible.
5. If desired, install the particle filter onto the end of the inlet line. Be sure the arrow on the
particle filter is pointed toward the inlet line.
Installing the Exhaust Line
1. Loosen the nut on the exhaust fitting until 3 threads are visible.
2. Push 1/4” O.D. rigid polypropylene or rigid Teflon sample tubing into the fitting until it
stops. Flexible polyurethane tubing may be used with an appropriate insert. RKI
Instruments, Inc. recommends using either 1/4” O.D. x 1/8” I.D. or 1/4” O.D. x 0.170”
I.D. tubing based on your length requirements. See “Specifications” on page 5 for
maximum tubing lengths based on tubing size.
CAUTION:
If you use
flexible
sample tubing (polyurethane is acceptable), use an
appropriate insert to seal the connection between the tubing and the inlet
fitting.
3. Hand tighten the nut on the exhaust fitting so the ferrules clamp on the tubing. If the tube
nut is removed, see Figure 6 for the arrangement of the fitting components.
4. Route the opposite end of the tubing to an open area where the sample can safely disperse
or to an exhaust duct. See “Specifications” on page 5 for maximum tubing lengths based
on tubing size.
Wiring the Sample-Draw Detector to a Controller
WARNING: Always verify that the controller is off and that power to the controller is off
before you make wiring connections.
1. Turn off the controller.
2. Turn off power to the controller.
3. Unlatch and open the housing door of the sample-draw detector.
4. Guide a three-conductor, shielded cable or three wires in conduit through the conduit hub
at the bottom of the sample-draw housing. A minimum of 18 AWG wire is recommended.
5. Connect the cable to the sample-draw detector’s interconnect terminal strip as shown in
6. Close and latch the housing door of the sample-draw detector.