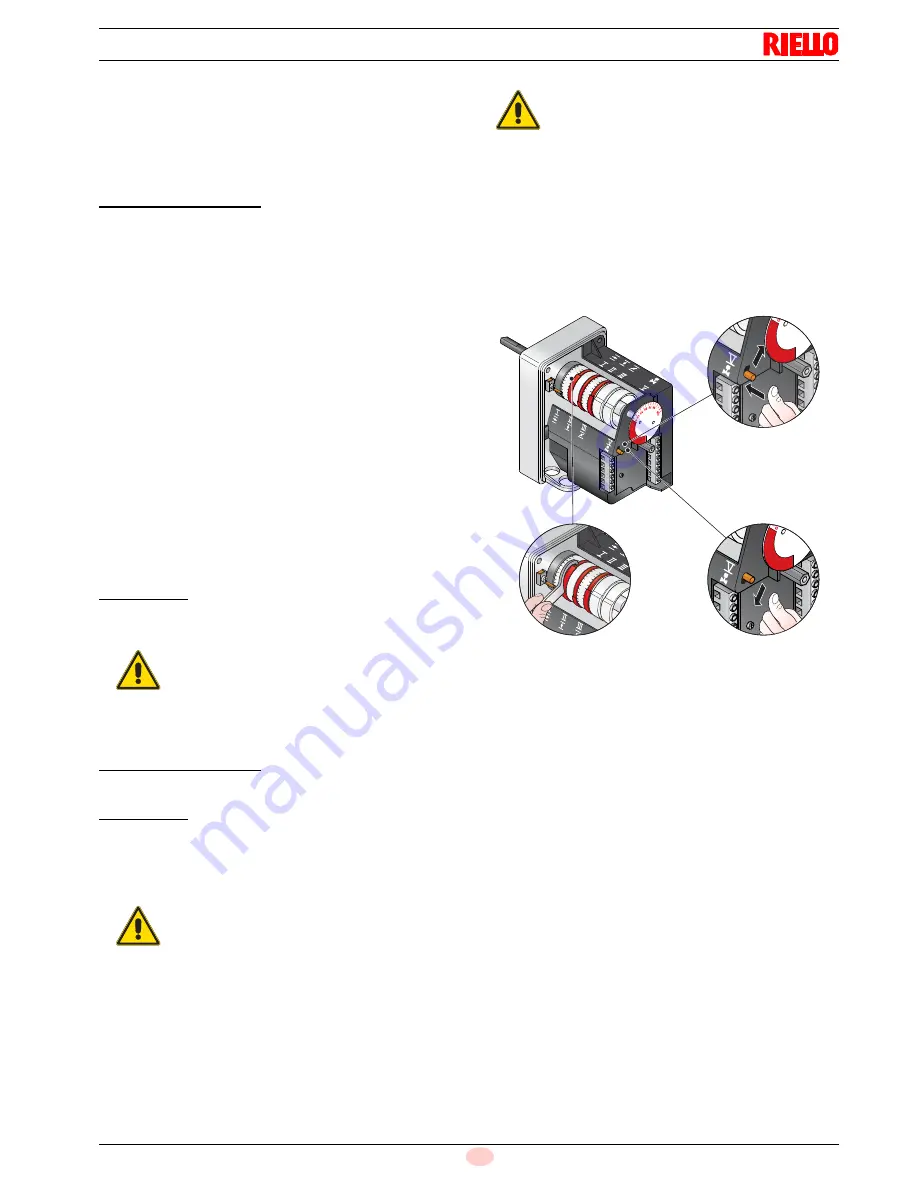
27
20054085
GB
Start-up, calibration and operation of the burner
6.6.3
Minimum output
Min output must be selected within the firing rate range shown on
page 9.
Press the “reduce output” button 2)(Fig. 28), and keep it pressed
until the servomotor has closed the air damper and the gas but-
terfly valve at 50° (adjustment made in the factory).
Adjustment of gas delivery
Measure the gas delivery on the gas meter.
–
If it is necessary to reduce it, slightly reduce the angle of cam
III (Fig. 32) with small, regular movements (i.e. bring it from
an angle of 65° to 63° - 61°....).
–
If it is necessary to increase it, lightly press the “increase out-
put” button 2)(Fig. 28) (open the gas butterfly valve by 10-
15°) and increase the angle of cam III (Fig. 32) with small,
regular movements (i.e. bring it from an angle of 65° to 67° -
69°....).
Now press the “reduce output” button until the servomotor is
in the minimum opening position, and measure the gas out-
put.
NOTE
The servomotor only follows the adjustment of cam III when the
angle of the cam is reduced.
If you need to increase the angle of the cam, you must first in-
crease the angle of the servomotor with the aid of the “increase
output” button.
Now increase the angle of cam III, then bring the servomotor
back to the MIN output position using the “reduce output” button.
For any necessary adjustment of cam III, especially for small
movements, use the specific key 10)(Fig. 32).
Air adjustment
Progressively adjust the initial profile of the cam 4) (Fig. 31) by
turning the screws 5).
6.6.4
Intermediate outputs
Adjustment of gas delivery
No adjustment of gas delivery is required.
Air adjustment
Lightly press the “increase output” button 2)(Fig. 28) so the ser-
vomotor rotates by about 15°.
Adjust the screws until optimal combustion is obtained. Proceed
in the same way with the other screws.
Switch off the burner via the switch 1)(Fig. 28) (“OFF” posi-
tion).
Release the cam 4 from the servomotor by pressing the but-
ton 3) and moving it to the right.
Manually rotate the cam 4) backwards and forwards several
times to make sure it moves smoothly.
Now engage cam 4) again to the servomotor by shifting but-
ton 2) to the left.
Once optimum adjustment has been reached, fix it with the
screws 6).
NOTE
Once you have finished adjusting the MAX - MIN - INTERMEDI-
ATE outputs, check ignition once again: noise emission at this
stage must be identical to the following stage of operation.
If you notice any sign of pulsations, reduce the ignition output.
Key (Fig. 32)
1
Servomotor
2
Servomotor 1) - cam 4): constrained
3
Servomotor 1) - cam 4): released
10 Spanner for adjusting cam III
CAUTION
It is preferable not to turn the first screw, as this
one is used to bring the air damper to its fully
closed position.
WARNING
Take care that the cam profile variation is progres-
sive.
WARNING
As far as is possible, try not to move those screws
at the ends of the cam that were previously adjust-
ed for the opening of the air damper to MAX and
MIN output.
D3922
10
2
3
Fig. 32
Содержание RS 150/M
Страница 2: ...Translation of the original instructions ...
Страница 41: ...39 20054085 GB Appendix Electrical panel layout ...
Страница 42: ...20054085 40 GB Appendix Electrical panel layout ...
Страница 43: ...41 20054085 GB Appendix Electrical panel layout ...
Страница 44: ...20054085 42 GB Appendix Electrical panel layout ...
Страница 45: ...43 20054085 GB Appendix Electrical panel layout ...
Страница 46: ...20054085 44 GB Appendix Electrical panel layout ...