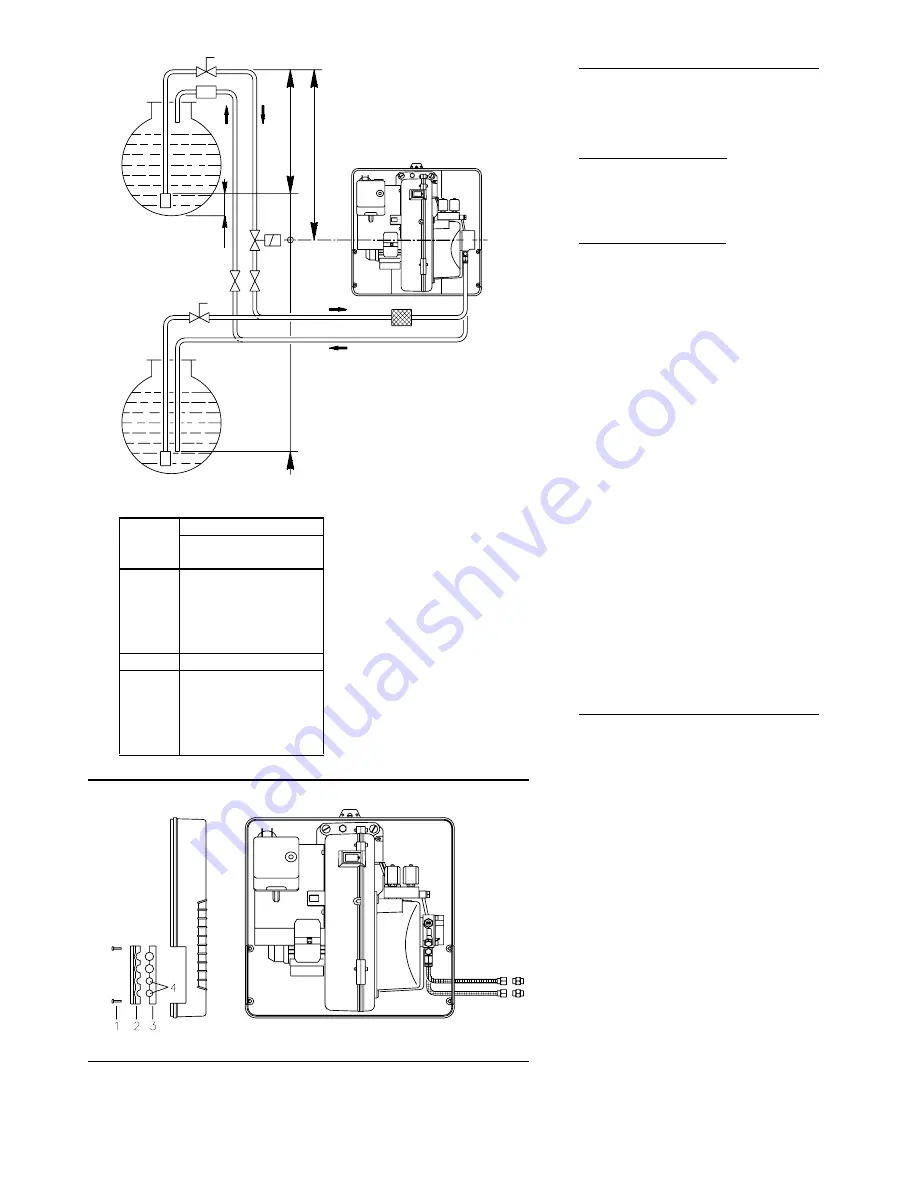
7
HYDRAULIC SYSTEM
FUEL SUPPLY
Double-pipe circuit (A)
The burner is equipped with a self-priming pump
which is capable of feeding itself within the limits
listed in the table at the side.
The tank higer than the burner
A
The distance "P" must not exceed 10 meters in
order to avoid subjecting the pump's seal to ex-
cessive strain; the distance "V" must not exceed
4 meters in order to permit pump self-priming
even when the tank is almost completely empty.
The tank lower than the burner
B
Pump depression values higher than 0.45 bar
(35 cm Hg) must not be exceeded because at
higher levels gas is released from the fuel, the
pump starts making noise and its working life-
span decreases.
It is good practice to ensure that the return and
suction lines enter the burner from the same
height; in this way it will be less probable that the
suction line fails to prime or stops priming.
The loop circuit
A loop circuit consists of a loop of piping departing
from and returning to the tank with an auxiliary
pump that circulates the fuel under pressure. A
branch connection from the loop goes to feed the
burner. This circuit is extremely useful whenever
the burner pump does not succeed in self-priming
because the tank distance and/or height differ-
ence are higher than the values listed in the table.
Key (A)
H =
Pump/Foot valve height difference
L =
Piping length
Æ =
Inside pipe diameter
1 =
Burner
2 =
Pump
3 =
Filter
4 =
Manual on/off valve
5 =
Suction line
6 =
Foot valve
7 = Rapid closing manual valve remote con-
trolled (only Italy)
8 = On/off solenoid valve (only Italy)
9 =
Return line
10 = Check valve (only Italy)
HYDRAULIC CONNECTIONS (B)
The pumps are equipped with a by-pass that
connects return line with suction line. The pumps
are installed on the burner with the by-pass
closed by screw 6)(B)p.11.
It is therefore necessary to connect both hoses
to the pump.
The pump will break down immediately if it is run
with the return line closed and the bj-pass screw
inserted.
Remove the plugs from the suction and return
connections of the pump.
Insert the hose connections with the supplied
seals into the connections and screw them
down.
Take care that the hoses are not stretched or
twisted during installation.
Route the hoses through the holes in the plate,
preferably using those on the rh side, fig. (B):
unscrew the screws 1), now divide the insert
piece into its two parts 2) and 3) and remove the
thin diaphragm blocking the two passages 4).
Install the hoses where they cannot be stepped
on or come into contact with hot surfaces of the
boiler.
Now connect the other end of the hoses to the
supplied nipples, using two wrenches, one to
hold the nipple steady while using the other one
to turn the rotary union on the hose.
(A)
(B)
9
10
7
5
8
4
7
9
5
3
2
1
6
6
10 cm
+ H
V
P
- H
B
A
+ H
- H
(m)
L (m)
Æ (mm)
8
10
12
+ 4,0
52
134
160
+ 3,0
46
119
160
+ 2,0
39
104
160
+ 1,0
33
89
160
+ 0,5
30
80
160
0
27
73
160
- 0,5
24
66
144
- 1,0
21
58
128
- 2,0
19
43
96
- 3,0
15
28
65
- 4,0
-
12
33
D3264
D3265