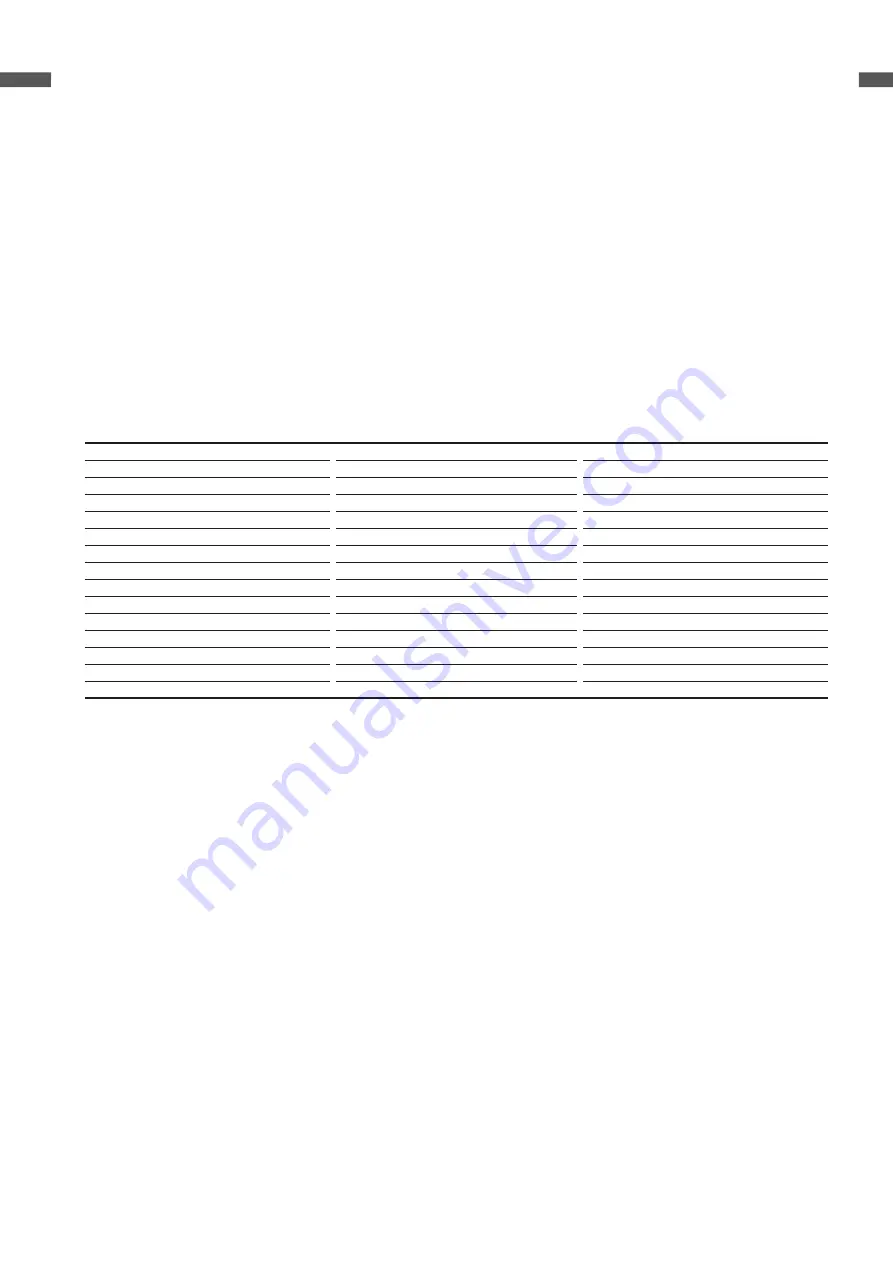
10
CONDENSING GENERATORS
Wall-hung gas condensing modules
WATER IN THE PLANT
Before connecting the thermal module, it is necessary to clean the system. This step is absolutely required when the appliance
replaces another one on pre-existing systems.In order to carry out this cleaning activity, if the old generator is still installed
on the system, it is advisable to:
• Add a de-scaling additive.
• Operate the system with the generator on for around 7 days.
• Discharge dirty system water and flush the system one or more times with clean water.
If the system is very dirty, repeat the last procedure one more time.In case of new installation or if the old generator is not
present or available, use a pump to circulate the additive water in the system for about 10 days and carry out the final washing
as described in the previous paragraph.
Once the cleaning has been completed, it is recommended to add a suitable protective fluid to the system's water before
installing the thermal module.
Do not use incompatible liquid detergents, including acids (eg chloridric acid and similar) in any concentration.
Do not subject the exchanger to cyclical pressure variations because the fatigue stress is very dangerous for the integrity of the
system components.
Sludge, limestone and contaminants present in the water can lead to irreversible damage to the heat generator, even in short
times and regardless of the quality level of the materials used.
The quality of the water used in the heating system must comply with the following parameters:
Parameters
Value
Unit
General characteristic
Colorless, without sediment
PH value
Min 6.5; Max 8
PH
Dissolved oxygen
<0.05
mg / l
Total iron (Fe)
<0.3
mg / l
Total Copper (Cu)
<0.1
mg / l
Na2SO3
<10
mg / l
N2H4
<3
mg / l
PO4
<15
mg / l
CaCO3
Min 50; Max 150
ppm
Trisodium phosphate
None
ppm
Chlorine
<100
ppm
Electrical conducibility
<200
microsiemens / cm
Pressure
Min 0.6; Max 6
bar
Glycol
Max 40% (only propylene glycol)
%
All the data in the table refer to the water contained in the system after 8 weeks' operation.
Do not use excessively softened water. Excessive water softening (total hardness < 5° f) results in corrosion due to contact with
metal elements (pipes or thermal module components).
Immediately repair any leaks or drips that could result in air entering the system.
Excessive pressure fluctuations can cause stress and fatigue to the heat exchanger.
Maintain a constant operating pressure.
Water used to fill a system for the first time and water used to top it up must always be filtered (using synthetic or metal mesh
filters with a filtration rating of no less than 50 microns) to prevent sludge from forming and triggering deposit corrosion. If
oxygen enters a circuit continuously or even intermittently (e.g. in under-floor heating systems whose pipes are not protected
by impermeable synthetic sheaths, in circuits with open expansion vessels, or in circuits that require frequent top-ups) always
separate the boiler’s water circuit from the central heating circuit.
It is prohibited to top up the heating system constantly or frequently, since this can damage the thermal module's heat
exchanger. The use of automatic topping up systems should be avoided for this reason.
To sum up, in order to eliminate contact between air and water (and to prevent the latter from becoming oxidized), it is
necessary:
• that the expansion system be a closed vessel, correctly sized and with the correct pre-loading pressure (to be regularly
checked);
• that the system be always at a pressure higher than the atmospheric one at any point (including the pump suction side)
and under any operating conditions (all seals and hydraulic couplings in a system are designed to withstand pressure
towards the outside, but not underpressure);
• the installation be not made with gas-permeable materials (e.g. plastic pipes without oxygen barrier for underfloor
heating systems).
Damages suffered by the thermal module, caused by encrustations and corrosion, are not covered by warranty.