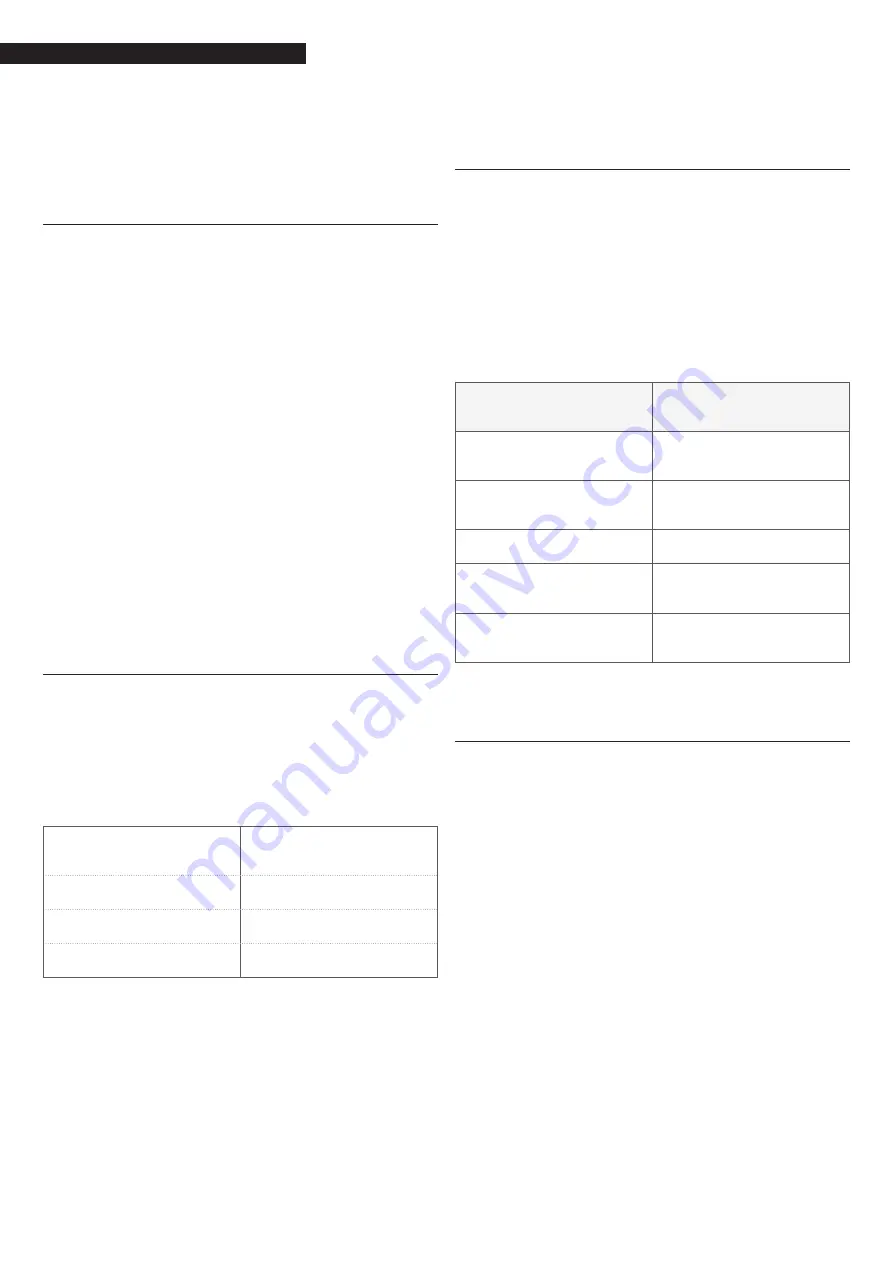
14
When faced with any fault (contactor, temperature swings,
interruption of current, other faults), or when the pumps are
stopped (protection pumps, etc.), the burner should switch off.
The system should do this automatically.
Carry out the electrical wiring taking into account all the
above-mentioned information.
1.18
Supply and discharge of the boiler water
Discharge of the boiler water
9
Switch off the boiler before emptying the boiler and let it
cool.
To empty the boiler, open all the valves of the circuit and the
radiators. All the system water should be discharged by drain-
ing the boiler, when the latter is in the lower part of the system
itself. If a part of the heating system is below the boiler room,
the process for draining the water can be carried out at a point
situated in the lower part of the system.
Supplying water to the boiler
To fill the boiler with water use the tap upstream of the boiler,
during the charging operations all the valves of the hydraulic
piping and radiators should be open. To prevent air infiltration,
carry out this operation slowly, opening the plug at the top.
When water comes out of this plug it means the process has
finished. Bleed the air from all the radiators.
9
Do not fill the boiler with water when it is hot. This could
damage the elements
9
The quality of the water should correspond to that indicated
in "1.9 Hydraulic system" a pagina 10
1.19
Instructions for disposing of the product
Cast iron boilers have a long life due to the particular character-
istics of the construction materials used. The service life of these
appliances, which is stated in the accompanying legal docu-
ments, is 15 years. Therefore, the replacement of these appli-
ances generally takes place for reasons of plant modernisation.
Cast iron boilers, produced with harmless materials, can be dis-
posed of as follows:
Cast iron body (Grey cast Iron)
Using disposal companies
specialised in iron and cast
iron foundries
Casing piping and panels
Using disposal companies
specialised in iron
Other Metal Parts
Using disposal companies
specialised in iron
Thermal ceramic and other
insulating materials
Using normal refuse dis-
posal services
NOTA:
For more information please contact au
NOTA:
thorised dealers
1.20
Fire prevention regulations for the boiler
room
The RTT 163-355 boilers should be positioned and installed par-
ticularly carefully and in conformity with fire safety regulations.
When installing and using the boiler, a safety distance of 200
mm must be observed from class B, C1 and C2 flammable ma-
terials.
For class C3 materials that easily catch fire, namely materials that
burn quickly and that keep combusting even after removal from
the source of the ignition, the safety distance is 400 mm.
The safety distance should be doubled also when the flamma-
bility class of the material has not been ascertained.
Flammability classes of the
materials and the construc-
tion products
materials and construction
products
A - Non-combustible
Granite, sandstone, bricks,
ceramic tiles, mortar, fire-
proof plasters etc.
B - Almost non-combustible
Acumin, izumin, heraklit,
lignos, basalt panels and
fibre, fiberglass panels etc.
C1- Difficult to ignite
Beech or oak, hobrex panels,
plywood, werzalit etc.
C2 - Normal combustibility
Pine, larch, white wood,
panels of wood shavings and
cork, rubber floors etc.
C3 - Easily ignited
Tar-coated sheets, polyure-
thane, polystyrene, polyethyl-
ene, PVC etc.
NOTA:
For more information, contact an authorised service
company.
1.21
Boiler checks and start-up
Preliminary checks
− The following checks need to be carried out before start-
ing the boiler. In the event of problems or faults, the boil-
er should not be started. Adequately air the room.
− Check the level of water in the boiler. If the level is below
the minimum, add the necessary amount.
− If the hydraulic system is leaking water, contact the tech-
nical assistance service which will carry out repairs, and
in any event repairs should be carried out before the
boiler is started.
− Check the connection between the fuel tank and the
burner. In the event of leaks or faults restore the connec-
tion before starting the boiler. Clean the filters.
− If the boiler runs on gas, make sure that the tank is
charged and check that the gas valves are open.
− If the boiler runs on liquid fuel, check the level in the fuel
tank and make sure the fuel valve is open.
− Check the pumps are running and check their rotation
direction.
− Check the control panel electrical system.
− All the boiler's gas and water valves should be open.
9
Check all the other connections according to the system's
options.
Boiler start-up
− Switch on the electrical supply using the master switch in
the boiler room, and as a result the operating lamp will
come on.
− Start the circulation pump
− Warning, it is mistaken to wait until the water tempera-