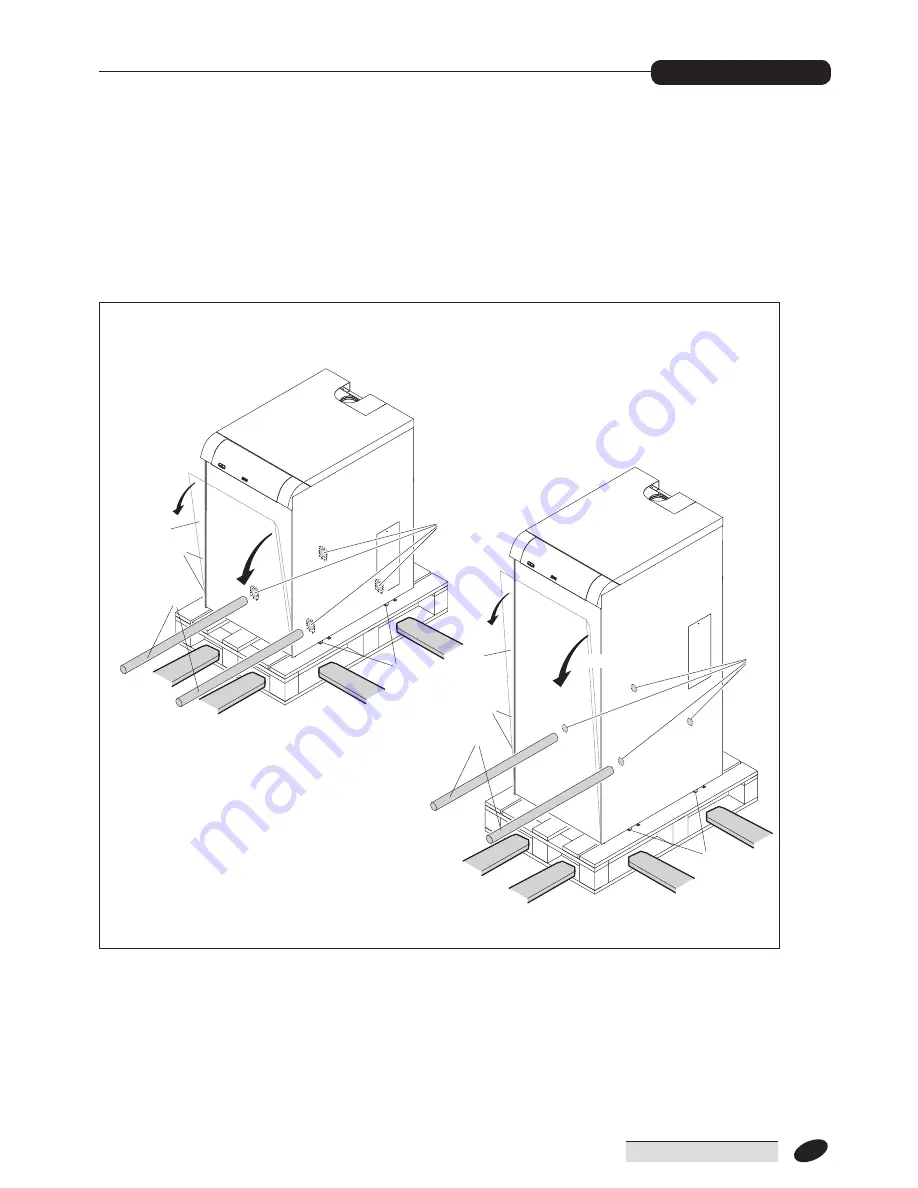
INSTALLER
19
2
1
4
2
2
1
2
4
3
3
INSIEME CONDENS
26 BK - 35 BK
INSIEME CONDENS
26 B - 35 B
HANDlING
Once you have removed the packaging, proceed as follows to handle the boiler.
- Remove the front panel (1) by pulling it forwards.
- Remove the screws (2) securing the boiler to the wooden pallet.
- Make sure that the equipment used to move the boiler is adequate for the weight involved.
- Insert two 3/4" pipes (3) through the lifting points (4) inside the boiler and lift the boiler carefully off the pallet.
b
Wear suitable personal protective equipment and use suitable safety devices.
a
Do not leave packaging material within the reach of children, since it can become a potential hazard. Dispose of
packaging material in compliance with applicable legislation.
ROTATE
ROTATE
Содержание 20039590
Страница 1: ...1 INSTALLATION AND MAINTENANCE MANUAL CONDENSING BOILERS 26 B 26 BK 35 B 35 BK 26 BK 35 BK 26 B 35 B ...
Страница 54: ...54 ...
Страница 55: ...55 ...