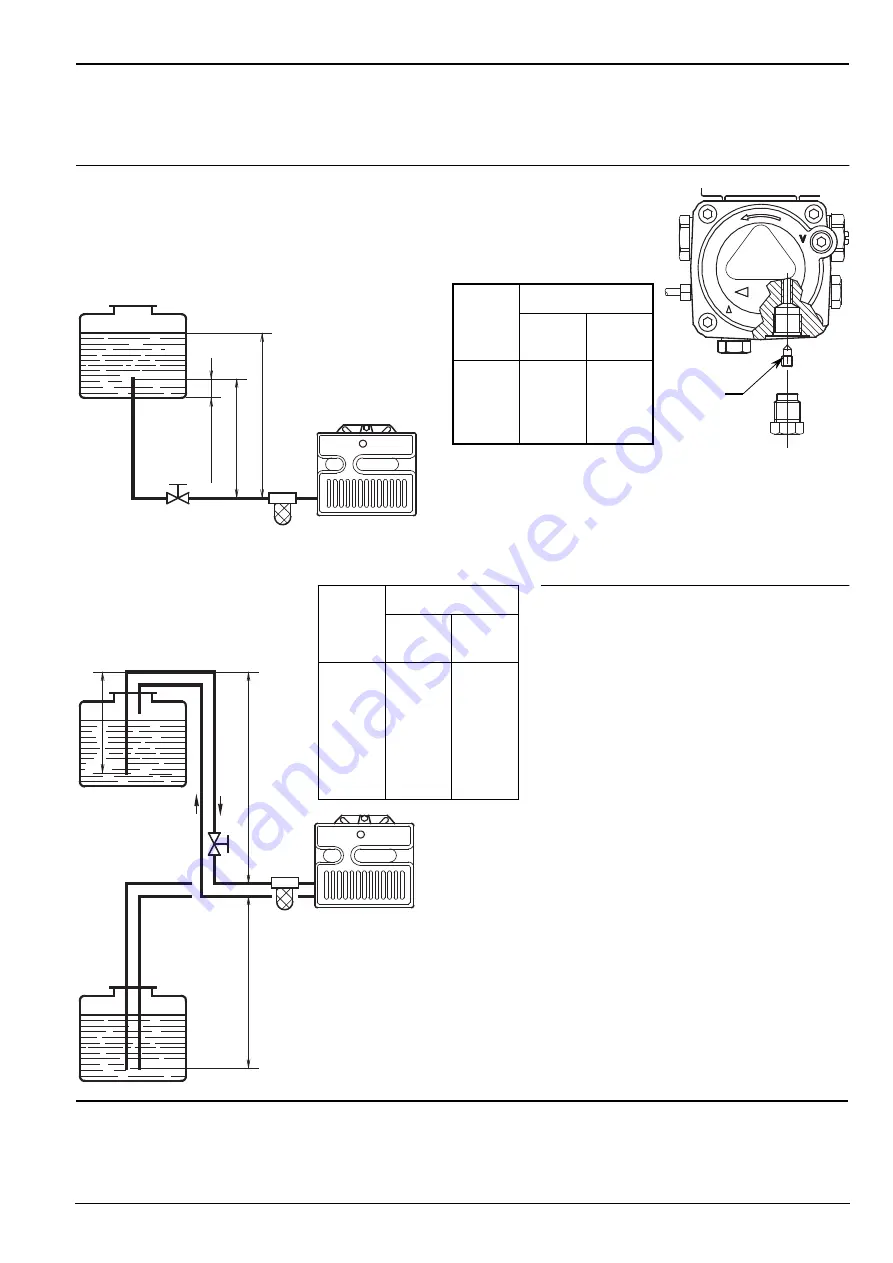
2508
3
OIL LINES
Warning:
before starting the burner make sure that the return pipe-line is not clogged: any obstruc-
tion would cause the pump seals to break.
The pump vacuum should not exceed a
maximum of 0.4 bar (30 cm Hg).
Beyond this limit gas is released from
the oil.
Oil lines must be completely airtight.
The return line should terminate in
the oil tank at the same level as the
suction line; in this case a non-return
valve is not required.
When the return line arrives over the
fuel level, a non-return valve must be
used.
This solution however is less safe than
previous one, due to the possibility of
leakage of the valve.
PRIMING THE PUMP
Start the burner and wait for the priming.
Should lock-out occur prior to the arrival
of the fuel, await at least 20 seconds
before repeating the operation.
◆
Check periodically the flexible pipes conditions. Using kerosene, they have to be replaced at
least every 2 years.
◆
A metal bowl filter with replaceable micronic filter must be fitted in the oil supply pipe.
H
meters
L meters
I. D.
8 mm
I.D.
10 mm
0.5
1
1.5
2
10
20
40
60
20
40
80
100
WARNING
The pump is supplied for use with a two pipe system.
For use on a one pipe system, it is necessary to remove the by-pass
screw (A), (see figure).
H
meters
L meters
I. D.
8 mm
I.D.
10 mm
0
0.5
1
1.5
2
3
3.5
35
30
25
20
15
8
6
100
100
100
90
70
30
20
H
max.
4 m
H
H
max.
4 m
min.
0.1 m
D5219
D5220
H =
Difference of level.
L
= Max.
length of the
suction line.
I.D. =
Internal diameter of the
oil pipes.
PRIMING THE PUMP
Loosen the plug of the vacuum gauge (5, fig. 1,
page 1) and wait until the fuel flows out.
A
D5809