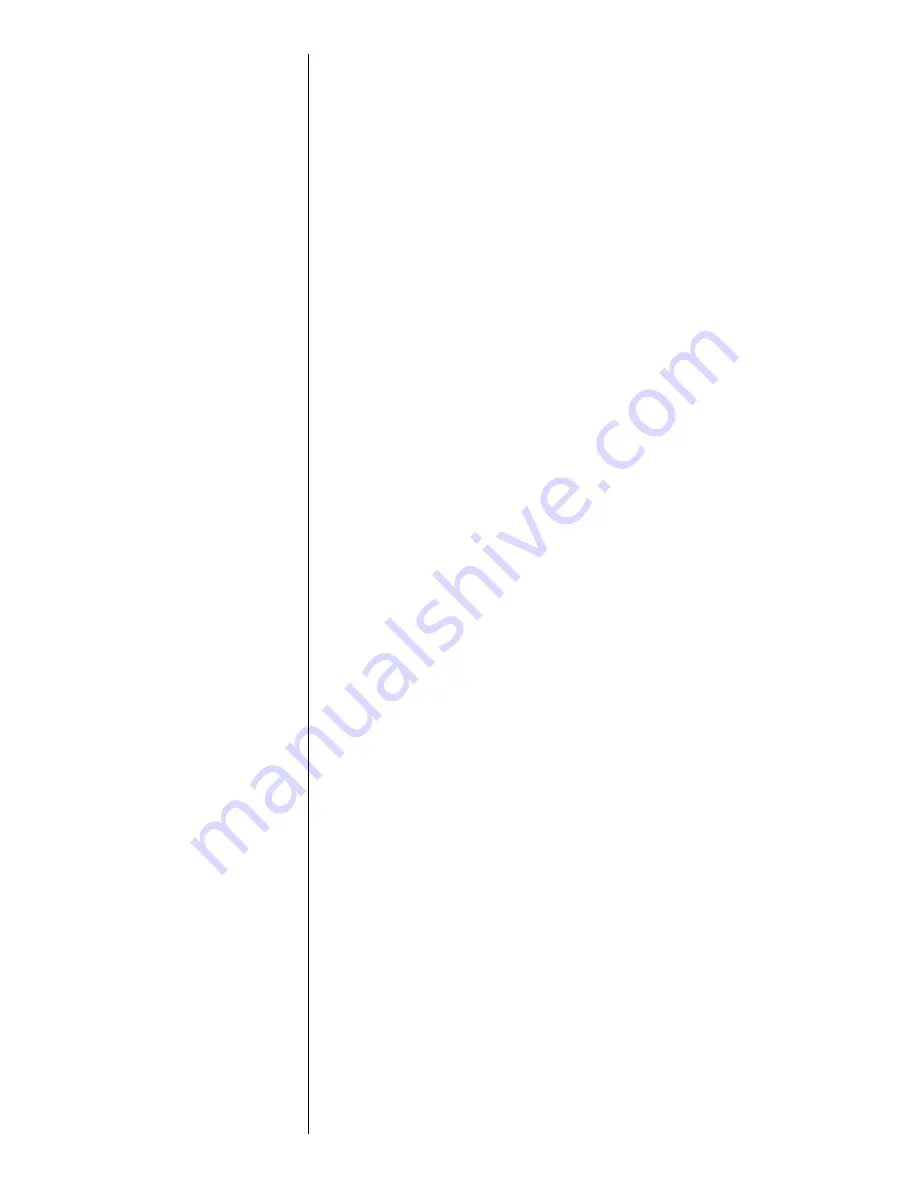
45
(-)H1T Blower Control
• There are two 24V outputs on the blower control for controlling the motor, one for con-
tinuous fan and one for cooling & heating operation.
• Motor speed changes are made at the motor speed terminal block instead of on the
blower control.
• The control has an on-board 3 amp automotive style fuse to protect the control circuit.
• A plug on the electric heater kit wiring harness plugs into a 4 pin plug receptacle on
the blower control to allow control of the electric heater by the blower control based
on thermostat input.
• There is a 6-pin connector for the thermostat pigtail harness to connect to. Wires
from the thermostat do not connect directly to the blower control, but rather to the pig-
tails that are routed to the exterior of the air-handler cabinet.
• There is no on-delay for blower operation when there is a call for blower operation.
• There is no blower off-delay provided by the blower control when a call for cooling or
heat pump heating ends since a 30 second off-delay is programmed into the constant
torque ECM motor.
• There is a blower off-delay programmed into the blower control when a call for electric
heating ends. The delay is 45 seconds for the White-Rodgers control and 30 seconds
for the UTEC control. This off-delay is added to the 30 second off delay programmed
into the motor for a total off-delay of 75 or 60 seconds. This allows time for the con-
tacts in the bi-metallic disc type heating sequencer to open which de-energizes the
heater elements.
5.4 BLOWER
The blower utilizes a forward curved centrifugal wheel. The blower housing is construct-
ed from galvanized sheet metal. The motor is attached with a 4-arm belly band type
mount that screws into the side of the blower housing. The control box attaches to the
front of the blower housing for assess through the blower access door. The blower
slides into place on a track and is secured by 4 sheet metal screws.
5.5 TRANSFORMER
A 40VA transformer is located inside the control box attached to the blower housing
which provides 24V control voltage for both the air-handler & the outdoor unit. The
transformer in 208/240V models is wired from the factory for 240V applications, but has
a separate 208V tap for 208V applications. The black wires connected to the 240V tap
must be moved to the 208V tap when installing the air-handler in 208V applications to
assure full 24V+ control voltage for reliable operation of the system controls.
5.6 INDOOR COIL ASSEMBLY
• The indoor coil slabs are a fin & tube design with enhanced aluminum fins & internally
grooved aluminum tubing.
• Most models have 3 coil slabs in an “N” configuration, but some models have 2 coil
slabs in an “A” configuration.
• All (-)H1P air-handlers have non-bleed thermal expansion valves (TXV) for refrigerant
control.
• (-)H1T air-handlers can have either a non-bleed TXV or a fixed orifice (piston). The
orifice may have to be changed when the air-handler is matched to certain outdoor
units. The correct orifice will be supplied with the outdoor unit in cases where the ori-
fice requires changing. (See Section 3.8)
• The 10th character in the model number indicates which type of metering device the
air-handler is equipped with, ”T” for TXV and “P” for piston. (See Section 2.3 for the
model number nomenclature).
• All models have a self-draining polypropylene condensate drain pan to eliminate
standing water & a painted & insulated sheet metal drip pan to catch any water drips
from the coil when the air-handler is oriented in the horizontal position.
• All models have built-in sheet metal channels in various locations designed to man-
age condensate when the air-handler is oriented in the horizontal position, thus pre-
venting water “blow-off”.
• Copper stubs are provided for field tubing connections.
• The coil assembly slides into the air-handler on sheet metal rails. The coil is installed in
the factory for upflow & horizontal left orientations. The coil must be removed and re-
installed into the air-handler cabinet 180° from its factory orientation. An additional set
of coil support rails must be installed before the coil can be re-installed. The additional
set of rails are included with the air-handler for field installation. (See Section 3.2.2)
• The TXV sensing bulb is shipped unattached & must be securely attached to the
vapor line with the supplied clamp and insulated with the supplied foam insulation.
(See Section 3.10)