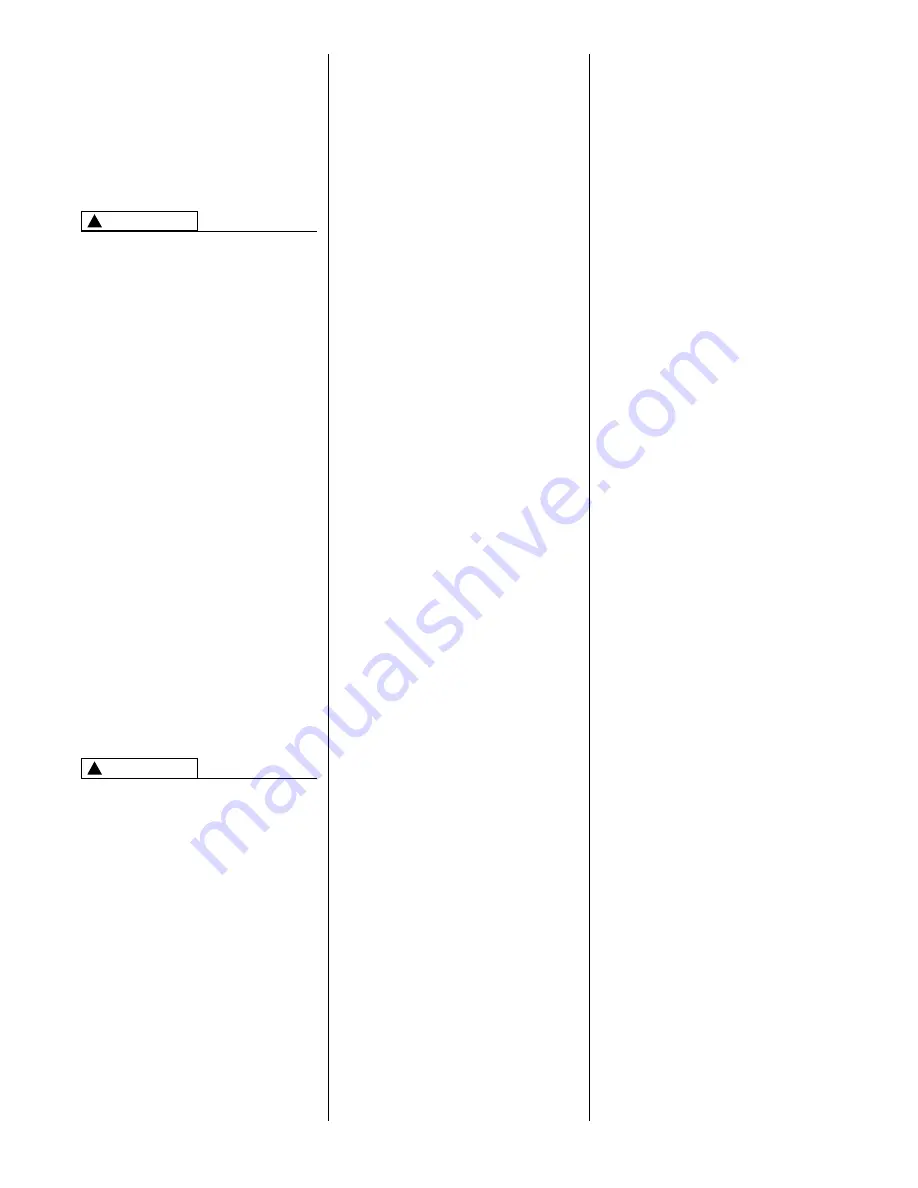
23
DIRECT SPARK IGNITION
LIGHTING INSTRUCTIONS
This appliance is equipped with a direct
spark ignition device. This device lights
the main burners each time the room
thermostat (closes) calls for heat. See
lighting instructions on the furnace.
TO START FURNACE
1.
BE SURE THAT THE MANUAL
GAS CONTROL HAS BEEN IN THE
“OFF” POSITION FOR AT LEAST
FIVE MINUTES. DO NOT
ATTEMPT TO MANUALLY LIGHT
THE MAIN BURNERS. FAILURE
TO FOLLOW THIS WARNING CAN
CAUSE A FIRE OR AN
EXPLOSION RESULTING IN
PROPERTY DAMAGE, PERSONAL
INJURY OR DEATH.
2. Set the room thermostat to the
lowest setting.
3. Turn the gas control knob to the
“On” position, or move the gas
control lever to the “On” position.
4. Replace the control access door.
5. Turn on the electrical power.
6. Set the room thermostat to a point
above room temperature to light the
main burners. After the burners are
lit, set room thermostat to a desired
temperature.
TO SHUT DOWN FURNACE
1. Set the room thermostat to its lowest
setting.
2. Shut off the gas to main burners by
turning the gas control knob to the
“Off” position, or by depressing the
gas control lever and moving it to
the “Off” position.
SHOULD OVERHEATING OCCUR
OR THE GAS SUPPLY FAIL TO
SHUT OFF, SHUT OFF THE MANUAL
GAS VALVE TO THE APPLIANCE
BEFORE SHUTTING OFF THE
ELECTRICAL SUPPLY. FAILURE TO
DO SO CAN CAUSE AN EXPLOSION
OR FIRE RESULTING IN PROPERTY
DAMAGE, PERSONAL INJURY OR
DEATH.
Sequence of operation with a single
stage thermostat
a. Connect the “W” terminal on the
thermostat to the W2 terminal on the
control board.
WARNING
!
b. When there is a call for heat, the “R”
and “W2” contacts close and the IFC
runs a self check routine to verify
that the pressure switch contacts
are open. The limit switch contacts
are constantly monitored.
c. The induced draft motor starts on
high for a few seconds to assure
that the low pressure switch
contacts close and then changes to
low speed. After a 30 second
prepurge the spark ignitor is
energized and the low stage of the
gas valve opens, lighting the
burners.
d. After the gas valve opens, the
remote flame sensor must prove
ignition for one second using the
process of flame rectification. If the
burners do not light, the system
goes through another ignition
sequence. It does this up to 4 times.
(2 tries on low fire and 2 tries on
high fire.)
e. The main blower starts on low
speed 30 seconds after the burners
light. The furnace will operate on low
fire for 12 minutes and then, if the
thermostat is not satisfied, shift to
high fire, causing the draft inducer to
go to high speed and the main
blower will go to heat speed. The
draft inducer will continue running
for a 5 second (low speed) or 10
second (high speed) post purge.
The main blower will run for 90
seconds on high speed or 120
seconds on low speed. (This timing
is field adjustable, for 60, 90, 120 or
150 seconds). See Figure 18 for
switch settings.
Sequence if the system doesn’t light
or doesn’t sense flame:
a. If flame is not sensed within 8
seconds after the gas valve opens,
the valve closes and the ignitor is
de-energized. The induced draft
motor will run for 60 seconds on low,
stop momentarily, and then restart.
The ignition process will go through
one more try on low fire. If this fails,
there will be two tries on high fire
with a 30 second interpurge
between trials. If there is no ignition
after the 2nd trial on high fire, the
furnace will go into soft lockout for
one hour.
b. The sequence will repeat after a one
hour delay and continue repeating
until ignition is successful or the call
for heat is terminated.
c. To reset the lockout, make and
break power either at the thermostat
or at the unit disconnect switch for 5
to 10 seconds. The furnace will then
go through another set of trials for
ignition.
Sequence of operation with two
stage thermostat
Connect W1 and W2 terminals on the
thermostat to W and W2 terminals on
the control board.
Call for 1st stage heat
a. R and W thermostat contacts close
and the control module runs a self-
check routine. After the control
module verifies that the 1st stage
pressure switch contacts are open
the induced draft motor runs on high
for a few seconds to assure that low
pressure switch contacts close. The
induced draft motor then switches to
low speed. After a 30 second
prepurge the spark ignitor is
energized and the low stage of the
gas opens, lighting the burners.
b. After the gas valve opens the
remote flame sensor must prove
ignition. If the burners do not light,
the system goes through another
ignition sequence. It does this up to
4 times (2 tries on low fire and 2
tries on high fire).
c. The main blower will start on low
speed 30 seconds after the gas
valve opens. The furnace will
continue to run on low until the call
for heat is satisfied and the 2nd
stage contacts close. If the 1st stage
call for heat is satisfied the gas
valve will close and the induced
draft motor will continue running for
a 10 second post purge time. The
main blower will run for 90 seconds.
(This is field adjustable for 90, 120,
150 or 180 seconds.)
Call for 2nd stage heat after 1st
stage
R and W2 thermostat contacts close,
calling for 2 stage heat. The induced
draft motor then switches to high
speed and the high pressure switch
contacts will close, allowing the gas
valve to switch to high fire and the
main blower to switch to heating
speed.
2nd stage heat satisfied, 1st stage
heat still required.
R and W2 thermostat contacts open.
The induced draft motor switches to
low fire and the main blower motor
switches to low speed. The furnace will
continue to run in this mode until the
1st stage heat call is satisfied. The
system will shut down as noted in “c,”
under 1st stage call for heat.
WARNING
!
Содержание RGLK
Страница 21: ...21 FIGURE 16 UTEC NO 1095 100 CONTROL BOARD TWINNING CONNECTION SINGLE STAGE OPERATION I685 ...
Страница 22: ...22 FIGURE 17 UTEC NO 1095 100 CONTROL BOARD TWINNING CONNECTION TWO STAGE OPERATION I684 ...
Страница 30: ...30 FIGURE 25 FILTER RETAINING RODS SIDE RETURN FIGURE 26 DOWNFLOW FILTER INSTALLATION ...
Страница 32: ...FIGURE 27 INTEGRATED FURNACE CONTROL IFC TROUBLESHOOTING GUIDE FOR UTEC 1095 100 32 ...
Страница 33: ...33 ...
Страница 34: ...FIGURE 28 UTEC 1095 100 INTEGRATED FURNACE CONTROL 34 ...
Страница 35: ...35 ...
Страница 36: ...36 CM 997 Rheem Manufacturing Company Air Conditioning Division Fort Smith Arkansas ...