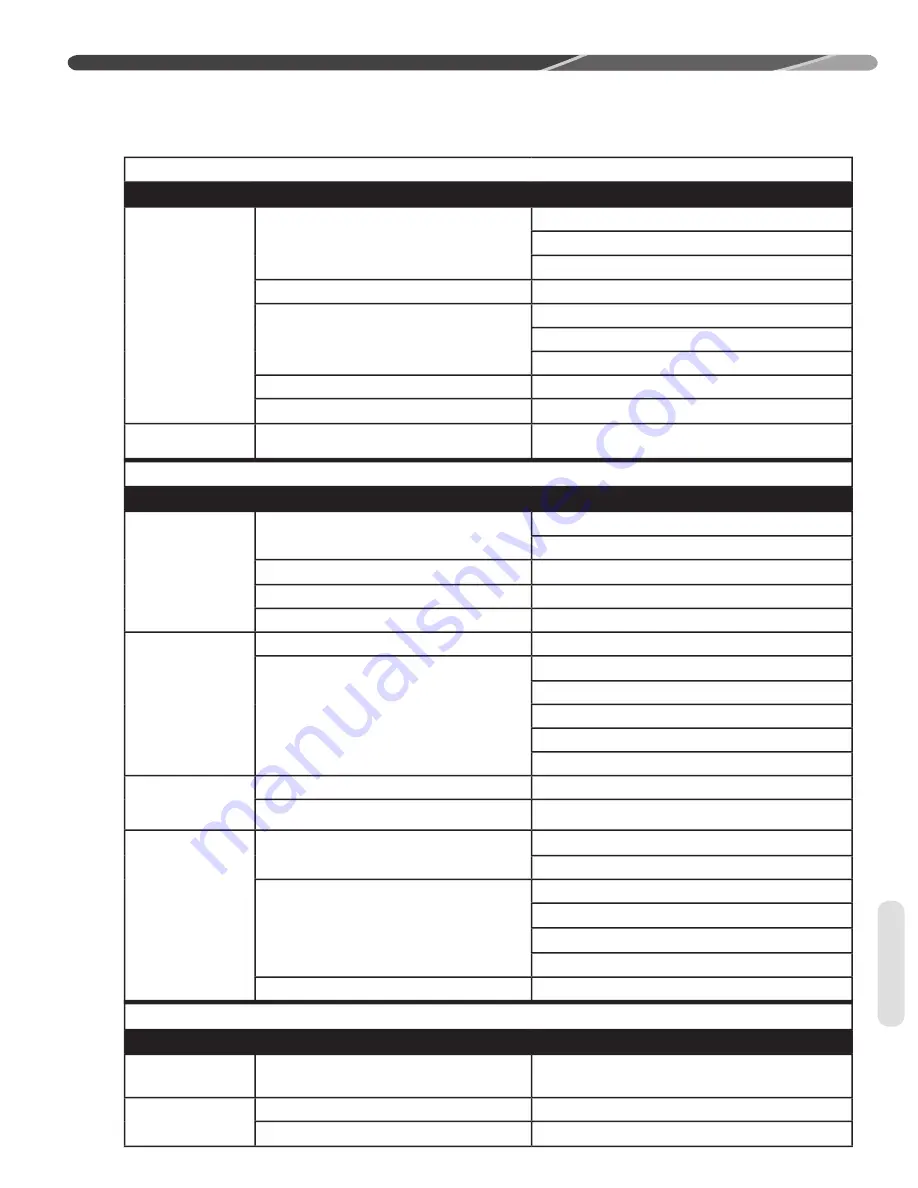
49
DIAGNOSTICS
Service Analyzer Charts
COMPRESSOR OVERHEATING (cont.)
SYMPTOM
POSSIBLE CAUSE
CHECK OR REMEDIES
Short cycling of
compressor (cont.)
Distributor tube
Restricted with foreign matter
Kinked
I.D. reduced from previous compressor failure
Low charge
Check system charge.
ow evaporator air ow
Dirty coil
Dirty lter
Duct too small or restricted
Faulty run capacitor
Replace.
Faulty internal overload
Replace compressor.
Faulty Compressor
Valves
ast equali ation ow pressure di erence
Replace compressor and examine system to
locate reason.
ELECTRICAL
SYMPTOM
POSSIBLE CAUSE
CHECK OR REMEDIES
Voltage present on
load side of com-
pressor contactor
and compressor
won't run
Compressor start components
Check start capacitor.
Check potential relay.
Run capacitor
Check with ohmmeter
Internal overload
Allow time to reset.
Compressor windings
Check for correct ohms.
Voltage present on
line side of com-
pressor contactor
only
Thermostat
Check for control voltage to contactor coil.
Compressor control circuit
High-pressure switch
Low-pressure switch
Ambient thermostat
Solid-state protection control or internal thermal sensors
ompressor timed o on control or interloc
No voltage on line
side of compressor
contactor
Blown fuses or tripped circuit breaker
Check for short in wiring or unit.
Improper wiring
Recheck wiring diagram.
Improper voltage
High voltage
Wrong unit
Power supply problem
Low voltage
Wrong unit
Power supply problem
Wiring undersized
Loose connections
Single Phasing (3 phase)
Check incoming power and fusing.
FLOODED STARTS
SYMPTOM
POSSIBLE CAUSE
CHECK OR REMEDIES
Liquid in the com-
pressor shell
Faulty or missing crankcase heater
Replace crankcase heater.
Too much liquid in
system
Incorrect piping
Check piping guidelines.
Overcharge
Check and adjust charge.
Diagnostics
Содержание RA17 Series
Страница 16: ...16 N R Application not recommended INSTALLATION Table 2 Tubing...
Страница 17: ...17 N R Application not recommended INSTALLATION Table 3 Tubing...
Страница 54: ...54 R C For Single Phase Models WIRING DIAGRAMS Wiring Diagrams...
Страница 55: ...55 WIRING DIAGRAMS Wiring Diagrams...
Страница 56: ...56 NOTES...