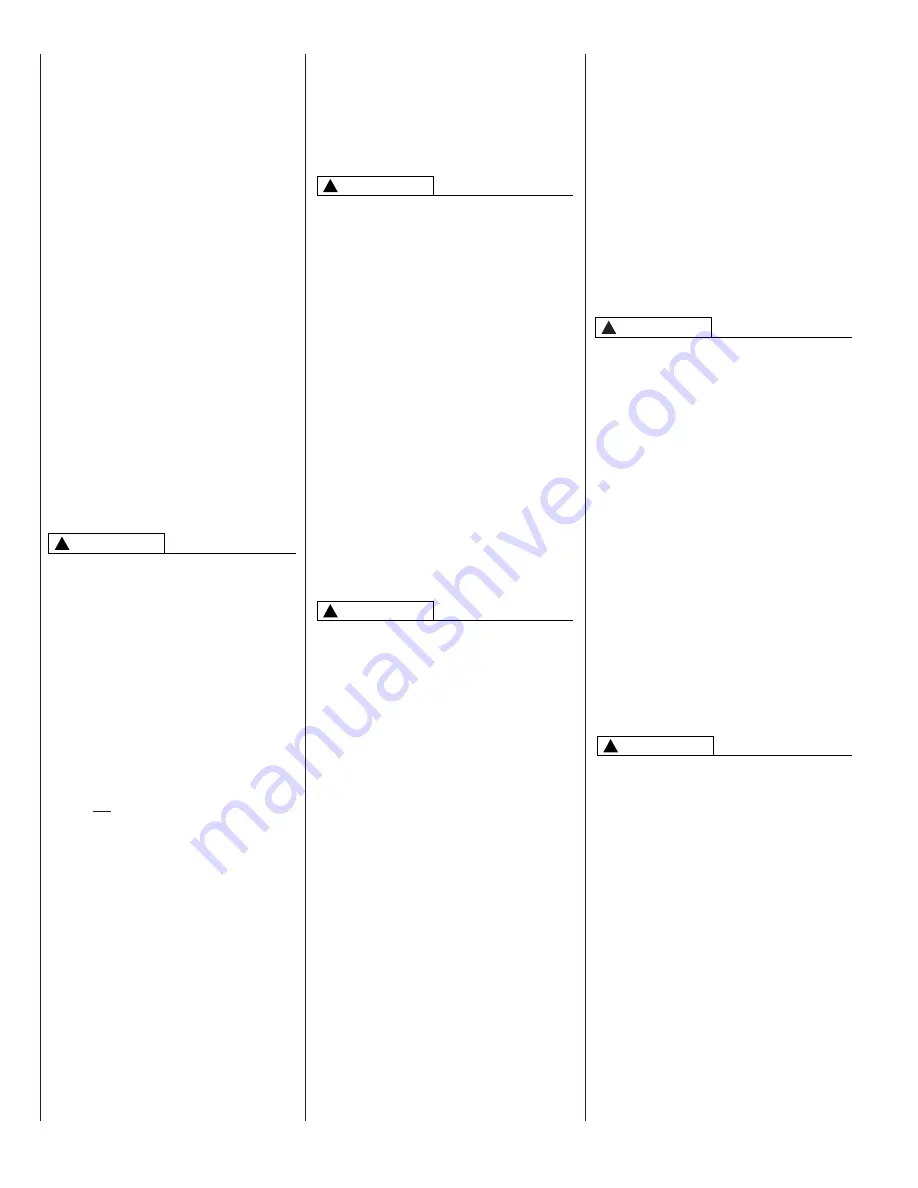
22
The integrated furnace control is
equipped with diagnostic LED. The LED
is lit continuously when there is power to
the control, with or without a call for heat.
If the LED is not lit, there is either no
power to the control or there is an internal
component failure within the control, and
the control should be replaced.
If the control detects the following failures,
the LED will flash on for approximately
1/4 second, then off for 3/4 second for
designated failure detections.
1 Flash: Failed to detect flame within the
three tries for ignition.
2 Flash: Pressure switch or induced draft
blower problem detected.
3 Flash: High limit or auxiliary limit open.
4 Flash: Flame sensed and gas valve not
energized or flame sensed with
no “W” signal.
5 Flash: Overtemperature switch open.
OPERATING INSTRUCTIONS
This appliance is equipped with
integrated furnace control. This device
lights the main burners each time the
room thermostat (closes) calls for heat.
See operating instructions on the back of
the furnace/controls access panel.
DO NOT ATTEMPT TO MANUALLY
LIGHT THIS FURNACE WITH A MATCH
OR ANY OPEN FLAME. ATTEMPTING
TO DO SO CAN CAUSE AN
EXPLOSION OR FIRE RESULTING IN
PROPERTY DAMAGE, PERSONAL
INJURY OR DEATH.
TO START THE FURNACE
1. Set the thermostat to its lowest
setting.
2. Turn off all electric power to the
appliance.
3. This appliance does not have a pilot.
It is equipped with an ignition device
which automatically lights the burner.
Do not try to light the burner by hand.
4. Remove control door.
5. Move control knob to the “OFF”
position. Turn the knob by hand only,
do not use any kind of tool.
6. Wait five (5) minutes to clear out any
gas. Then smell for gas, including
near the floor. If you smell gas,
STOP! Follow B in the safety
information on the Operating
Instructions located on the back of the
controls/access panel. If you don’t
smell gas, go to the next step.
7. Move the gas control knob from
“OFF” position to “ON” position.
Operate this appliance with the gas
control knob in the “ON” position only.
Do not use the gas control knob as a
means for throttling the burner input
rate.
MANUAL RESET
OVERTEMPERATURE
CONTROL
Four manual reset overtemperature
controls are located on the burner shield.
These devices senses blockage in the heat
exchanger or insufficient combustion air.
This shuts off the main burners if excessive
temperatures occur in the burner
compartment.
Operation of this control indicates an
abnormal condition. Therefore, the unit
should be examined by a qualified installer,
service agency, or the gas supplier before
being placed back into operation.
DO NOT JUMPER THIS DEVICE! DO
NOT reset the overtemperature control
without taking corrective action to
assure that an adequate supply of
combustion air is maintained under all
conditions of operation. Failure to do so
can result in carbon monoxide
poisoning or death. Replace this control
only with the identical replacement part.
PRESSURE SWITCH
This furnace has four pressure switches for
sensing a blocked exhaust or a failed
induced draft blower. They are normally
open and close when the induced draft
blowers start, indicating air flow through the
combustion chamber.
LIMIT CONTROL
The supply air high temperature limit cut-off
is set at the factory and cannot be adjusted.
It is calibrated to prevent the air
temperature leaving the furnace from
exceeding the maximum outlet air
temperature.
DO NOT JUMPER THIS DEVICE! DOING
SO CAN CAUSE A FIRE OR EXPLOSION
RESULTING IN PROPERTY DAMAGE,
PERSONAL INJURY OR DEATH.
IMPORTANT:
Replace this control only
with the identical replacement part.
8. Replace the control door.
9. Turn on all electric power to the
appliance.
10. Set the thermostat to the desired
setting.
11. If the appliance will not operate, follow
the instructions below on how to shut
down the furnace.
THE SPARK IGNITOR AND IGNITION
LEAD FROM THE IGNITION CONTROL
ARE HIGH VOLTAGE. KEEP HANDS OR
TOOLS AWAY TO PREVENT
ELECTRICAL SHOCK. SHUT OFF
ELECTRICAL POWER BEFORE
SERVICING ANY OF THE CONTROLS.
FAILURE TO ADHERE TO THIS
WARNING CAN RESULT IN PERSONAL
INJURY OR DEATH.
The initial start-up on a new installation
may require the control system to be
energized for some time until air has bled
through the system and fuel gas is
available at the burners.
TO SHUT DOWN FURNACE
1. Set the thermostat to the lowest
setting.
2. Turn off all electric power to the
appliance if service is to be
performed.
3. Remove control door.
4. Move control knob to the “OFF”
position.
5. Replace control door.
SHOULD OVERHEATING OCCUR OR
THE GAS SUPPLY FAIL TO SHUT OFF,
SHUT OFF THE MANUAL GAS VALVE
TO THE APPLIANCE BEFORE
SHUTTING OFF THE ELECTRICAL
SUPPLY. FAILURE TO DO SO CAN
RESULT IN AN EXPLOSION OR FIRE
CAUSING PROPERTY DAMAGE,
SEVERE PERSONAL INJURY OR
DEATH!
BURNERS
Burners for these units have been
designed so that field adjustment is not
required. Burners are tray-mounted and
accessible for easy cleaning when
required.
!
WARNING
!
WARNING
!
WARNING
!
WARNING
!
WARNING
Содержание A180CL25E
Страница 30: ...30 FIGURE 26 ...
Страница 31: ...31 FIGURE 27 ...
Страница 32: ...32 FIGURE 28 ...
Страница 33: ...33 FIGURE 29 ...
Страница 34: ...34 SYSTEM CHARGE CHARTS FIGURE 30 ...
Страница 35: ...35 SYSTEM CHARGE CHARTS FIGURE 31 ...
Страница 36: ...36 SYSTEM CHARGE CHARTS FIGURE 32 ...