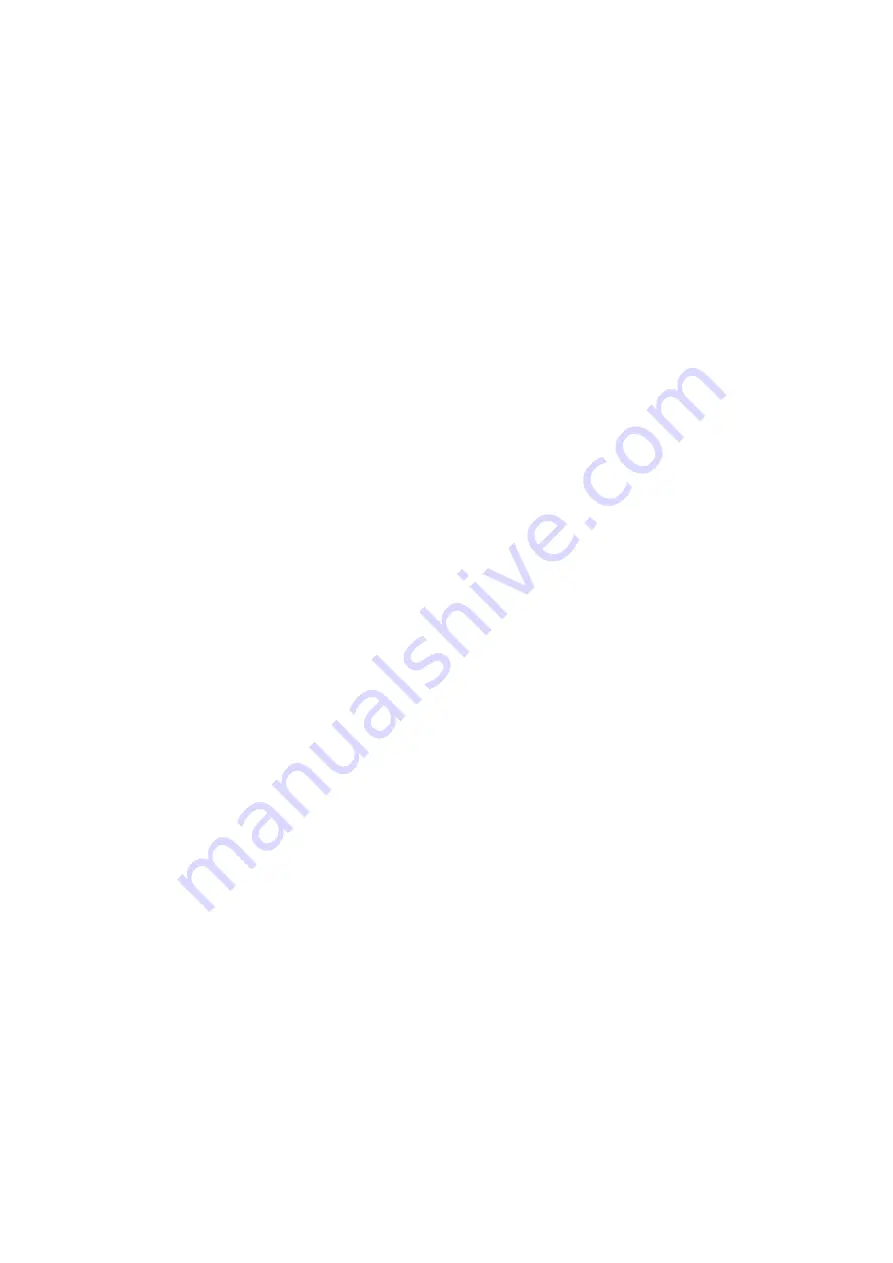
26/60 Installation
Bosch Rexroth AG
, A6VE Series 65 and 71, RE 91616-01-B/10.2014
▶
Avoid using a check valve in the drain line.
▶
To achieve favorable noise values, decouple all connecting lines from all vibration-
capable components (e.g. reservoir) using elastic elements.
▶
Make sure that the reservoir and return lines lead into the reservoir below the
minimum fluid level in all operating conditions. You prevent foam formation by
doing this.
▶
Make sure that the working environment at the installation site is fully free of
dust and foreign substances. The axial piston unit must be installed in a clean
condition. Contamination of the hydraulic fluid can have a considerable impact on
the function and service life of the axial piston unit.
▶
Use lint-free cloths for cleaning.
▶
Use suitable mild detergents to remove lubricants and other difficult-to-remove
contamination. Cleaning agents must not enter the hydraulic system.