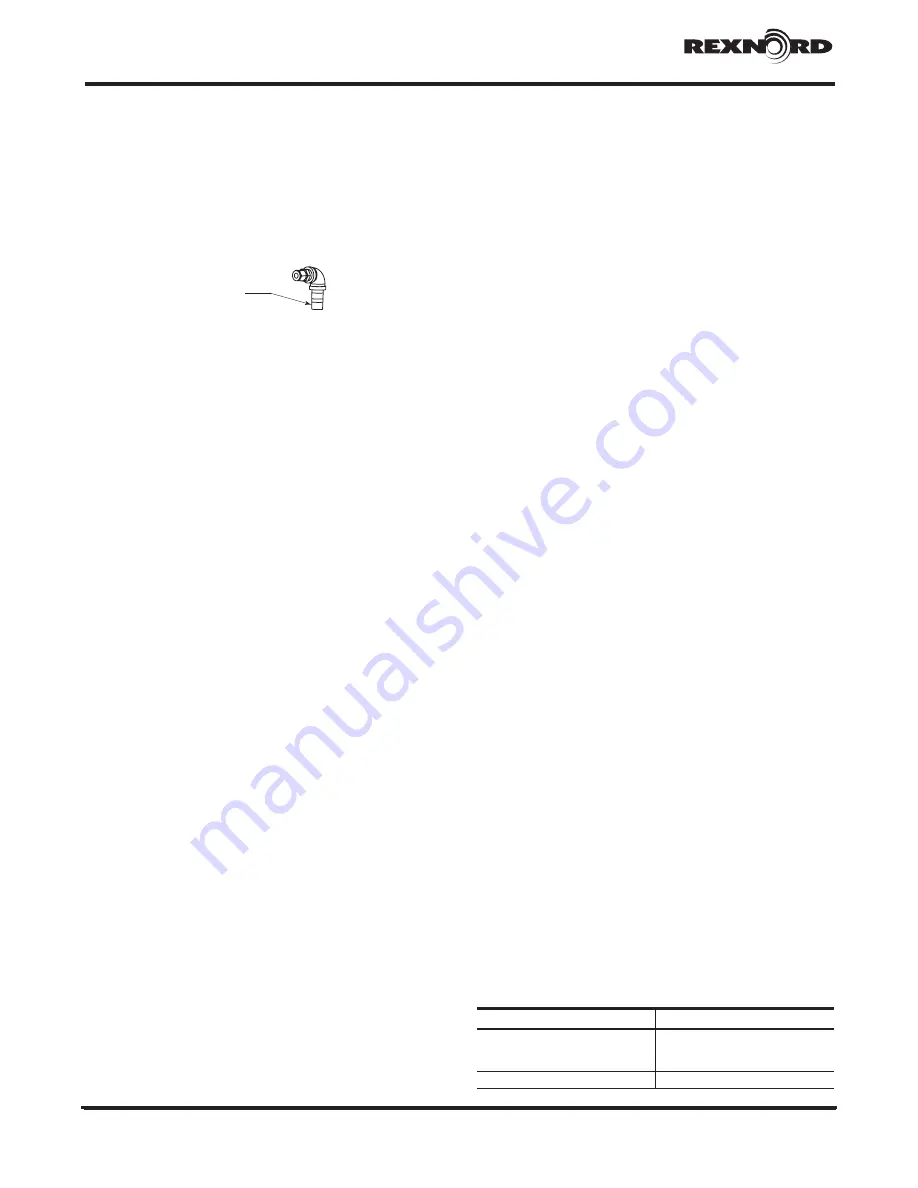
Appendix N • Falk Quadrive
Shaft Mounted Drives Model A
(Page 52 of 52)
Sizes 5215-5315
378-200
(PN-2128394)
Rexnord
January 2019
3001 W. Canal St., Milwaukee, WI 53208-4200 USA
Supersedes 04-17
Telephone:
414-342-3131
Fax:
414-937-4359
www.rexnord.com
4
AirMax Plus
— Prepare the AirMax breather for
installation by removing the two smaller red plastic
plugs from the bottom air vents located 180°F apart
Also, remove the large red plastic plug from the
breather mounting threads Thread the breather into
the pipe tee of the Reliability Package as shown in
Figure 1 Hand-tighten only to seal o-ring against pipe
tee For detailed breather installation and maintenance
instructions, refer to the literature included with the
AirMax Plus breather (GR3-002)
5
Lifting
— The drive can be lifted by using either a
sling with a longer housing flange fastener or a sling
wrapped around the seal housing and input shaft Lift
and mount the drive by following the drive installation
and lifting instructions provided in Section 1 (page 7)
of this Owner’s Manual
CAUTION
: To prevent damage to the hydraulic tubing, it
should NOT be installed until after the drive has been lifted
and mounted into position. Prevent debris from entering the
drive by covering the Lenz fittings of the subassemblies,
until the hydraulic tubing can be installed.
6
Hydraulic Tubing
— Install the hydraulic tubing by
following the steps outlined below:
1 Remove the nut and tapered split ring from the two
Lenz fittings
2 Slide the nut and the tapered split ring onto the ends
of the hydraulic tubing The large end of the tapered
ring should face the fitting
3 Apply oil to the O-ring
4 Insert the ends of the hydraulic tubing simultaneously
into the appropriate Lenz fittings Continue to push the
tubing into the Lenz fittings until the tube ends are
past each o-ring for proper sealing
NOTE
: The hydraulic tubing may have to be bent
slightly to install it properly into the Lenz fittings thus
ensuring the tubing extends past the o-rings in the
fittings
5 Once the hydraulic tube is positioned properly, slide
the tapered spit rings up to the Lenz fittings
6 Tighten the nut hand tight Then with a wrench
tighten one turn or until the rear of the tapered ring is
flush with the nut
7
Oil Fill
— Remove the oil fill pipe plug from location
#3 as shown in Figure 2 Using a funnel with a flexible
spout, fill the gearbox with an approved lubricant (refer
to Page 23 for Lubrication Recommendations; DO
NOT USE GMAX 6000 or other types of polyalkylene
glycol (PAG) lubricants which are not compatible with
the polycarbonate sight glass) Once the oil level
reaches the bottom of the fill hole, wait a minimum of 5
minutes for the oil to reach the oil level sight glass Add
additional oil to the gearbox and repeat the process
until the oil level in the gearbox and sight glass are
constant and the excess runs out It is recommended
to mark the sight glass with this final oil level
The oil level sight glass is intended to be used when
the gearbox is not running; in the static condition
Therefore, the sight glass contains a label that
indicates a static oil level
(oil levels tend to fluctuate
based on oil churning and are dependent on speed
and direction of rotation; for continuous direction, and
continuous speed applications it is recommended that
the oil level sight glass be marked once steady state
operating conditions have been reached)
Prepare the oil fill pipe plug for installation by applying
Loctite joint compound #1534294 to the threads
Reinstall the elbow subassembly into the Quadrive
housing at location #3 as shown in Figure 2
MAINTENANCE INSTRUCTIONS
AirMax Breather
— Falk AirMax Plus breathers have visual
indication when they need to be changed As the breather
functions, the silica gel material changes color from blue
to pink as it absorbs moisture When all the material has
turned pink in color, it is time to replace the breather
Breather life is dependent on operating conditions and
ambient conditions (humidity) Breather should be changed
every twelve (12) months regardless of color
Oil Sampling
— The oil sampling port that is
included allows users to easily draw oil samples for
lubrication analysis Refer to the Oil Analysis Report
section in Appendix A of this document for detailed
recommendations on oil content The oil sample port has
a screw on cover that needs to be unscrewed in order to
access the valve to the sampling port The valve can then
be actuated by screwing on the threaded oil sample port
adapter included in our Oil Sample Kit (sold separately;
see Table 2) The sampling bottle is composed of PET
(polyethylene terephthalate) which is compatible with
most industrial lubricants; however, user should confirm
compatibility prior to use It should be noted that the
cleanliness of the bottle can greatly affect the results of an
oil sample analysis; therefore user is cautioned to use care
to avoid contamination of the sample
The oil sample should be taken shortly after the unit has
been shut down to ensure the oil is properly mixed It is
important to initially purge some oil from the oil sampling
port and discard this purge, prior to collecting the sample
Be sure to check the oil level in the drive after the sample
has been collected (additional oil may need to be added to
ensure proper level)
TABLE 2 — Sample Port Adapter, Sampling
Kit and Breather for use by
Maintenance Professionals
Part Description
Part Number
Oil Sampling Kit (includes oil sample
port adapter, case of 12 sample bottles,
vacuum pump, 20' of tubing and labels)
10097025
AirMax Plus HG-1 Breather
10097978
3
Elbow Subassembly
— Prepare the elbow
subassembly for installation by applying Loctite joint
compound #1534294 to the male threads as shown
in Figure 4 Install the elbow subassembly into the
Quadrive housing at location #2 as shown in Figure 2
The galvanized elbow should be used to thread the
subassembly hand tight Using a pipe wrench, turn
the galvanized elbow an additional 2-3 turns so that it
is oil tight The elbow should be parallel to the output
shaft when finished as shown in Figure 1
APPLY LOCTITE
JOINT COMPOUND
#1534294
Figure 4 — Elbow subassembly